Electronic components inventory: How to do it right

Ioana Neamt
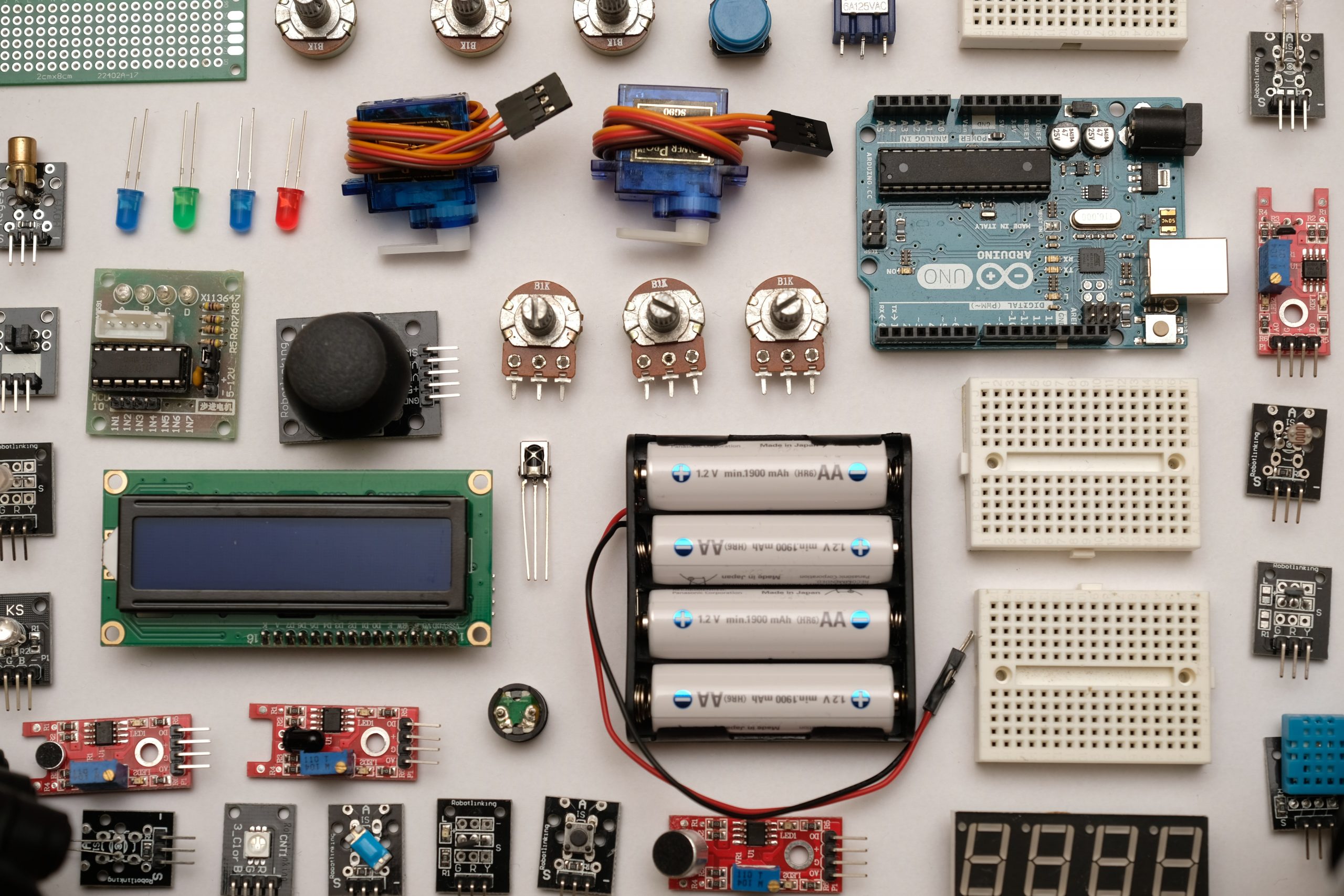
The COVID-19 pandemic caused a massive disruption to the electronic components industry. Lockdowns, lack of personnel, unforeseen weather events, and even a gigantic ship blocking the Suez Canal (remember the endless Evergreen-related memes?) had a big impact on businesses in the electronic components industry and the effectiveness of their supply chain. Add to that the global semiconductor shortage that followed, and suddenly numerous businesses found themselves with excess inventory related to electronic components.
The impact of the past few years (we say few because honestly, time doesn’t work the same as it did before 2020) is still felt today, as excess electronic component inventory remains a challenge for many business owners. So, what are some steps you can take to ensure that you don’t end up in the same situation, or that you find your way out of it quickly?
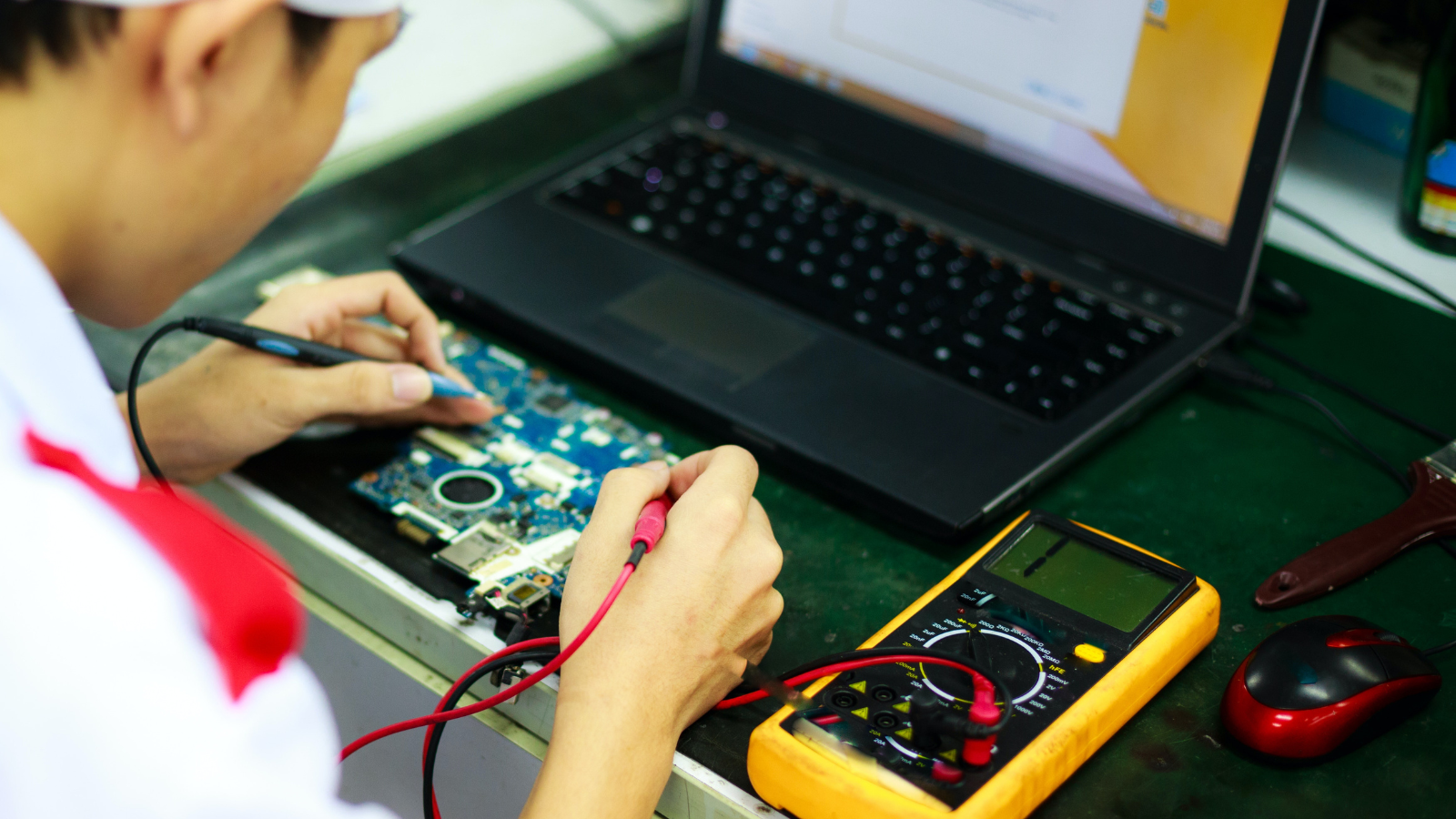
What is electronic components inventory, exactly?
As the name suggests, electronic components inventory, or ECI, encompasses all the various electronic parts and components used to manufacture and assemble different electronic devices. Think of things like:
- Connectors
- Switches and relays
- Transistors
- Capacitors
- Resistors
- Inductors
- Crystals and oscillators (not those that astrology-loving influencers are advertising on Instagram)
- And anything else that is used in electronics manufacturing.
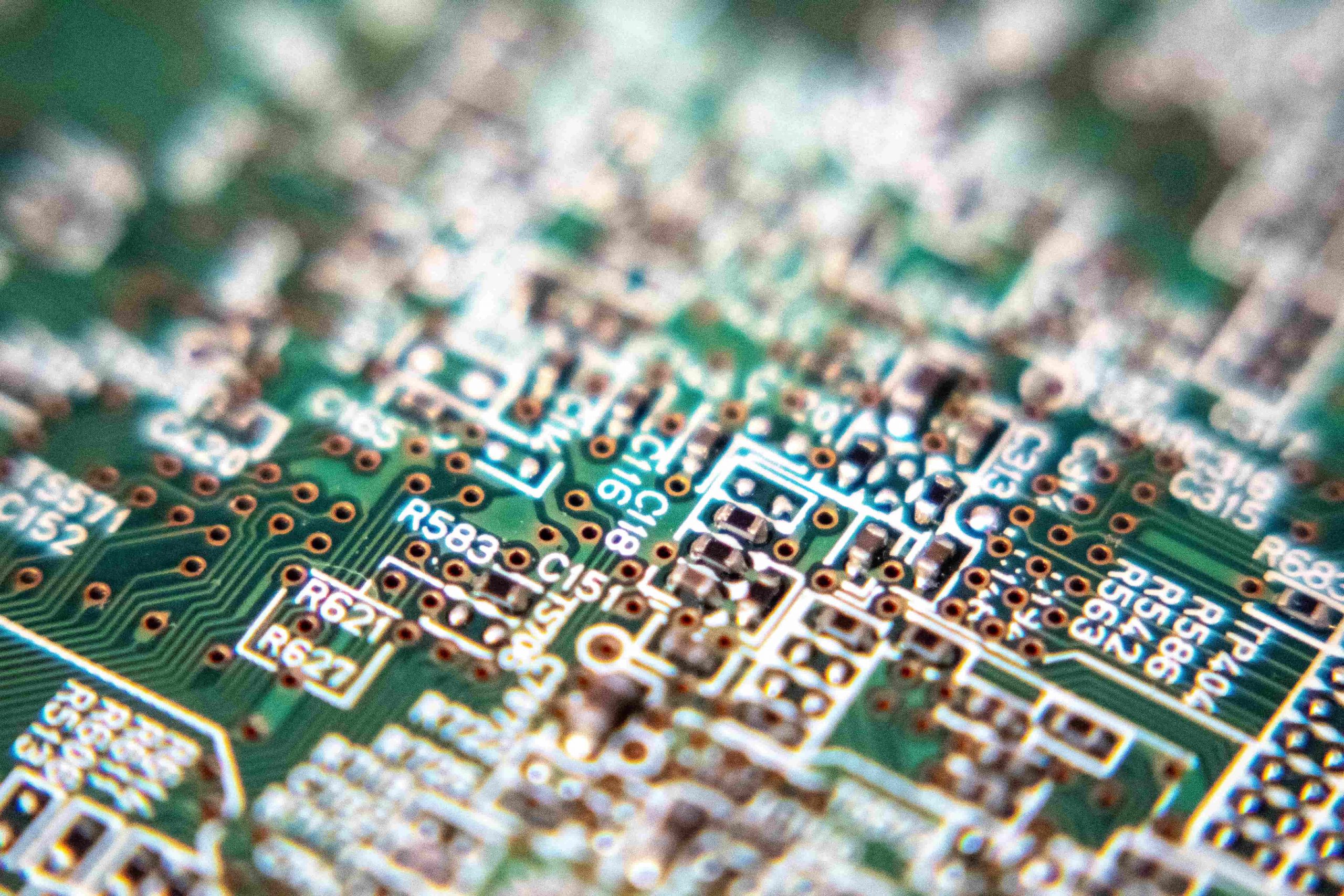
Why is electronic components inventory important?
Monitoring electronic components inventory in real time is crucial to effectively manage the items you have in stock and ensure the timely delivery of products and services. Without proper stock management processes in place to keep track of every single electronic component in the supply chain, businesses run the risk of overstocking or stockouts. This in turn can significantly disrupt internal processes, lead to storage issues, order processing delays, dissatisfied customers, and it can ultimately hurt your bottom line and profit margin.
The other crucial thing to note is that the electronics components industry is constantly evolving, and technologies are always being updated to new, better versions. This means that some of the items in your unsold inventory might soon become obsolete or reach their expiration date as they sit there gathering dust in your warehouse.
This is what effective inventory management strategies are meant to prevent — ensuring that you don’t end up with excess inventory at the end of the fiscal year. But things are not always this simple, because so many factors are out of your control, including unpredictable weather events, supply chain disruptions, market volatility, economic shifts, rising costs, scarcity of materials, and even crazy things like global pandemics and wars. Still, there are things you can do to mitigate these risks and ensure you’re at least partially prepared for whatever life throws at you.
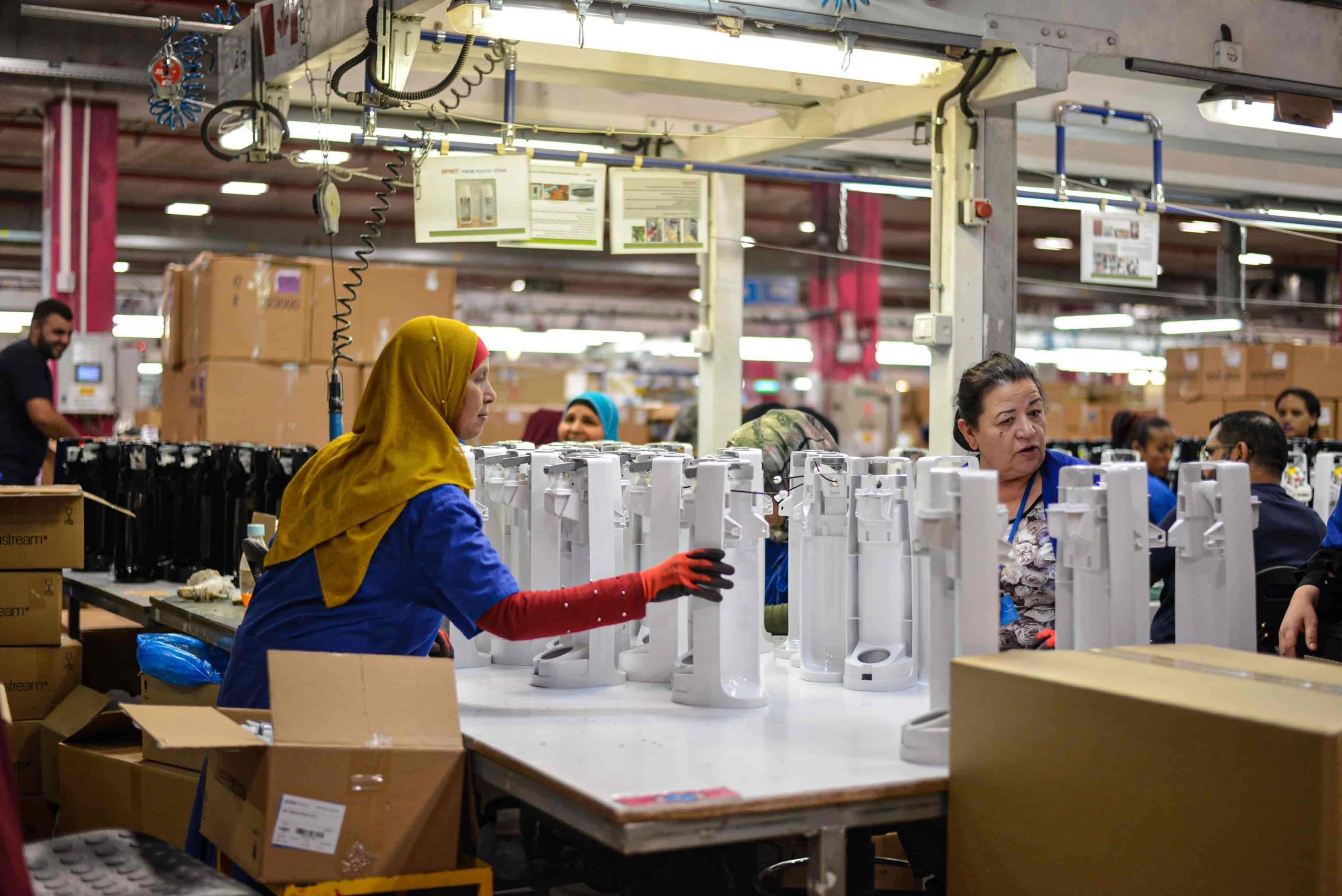
Avoiding excess electronic components inventory
There is no way to completely eliminate risk when it comes to inventory management, but a good software solution (like Katana) can help ensure you are prepared to deal with those challenges if and when they should arise.
Basically, inventory management is your best friend in this situation. Inventory management software enables you to monitor your electronic components in real time, while also using data to predict potential shifts in consumer behavior, market conditions, and more, helping you to plan for demand. Keeping a close eye on your product flow, sales data, pricing fluctuations, and demand, allows you to be better prepared for unforeseen situations and optimize the flow of goods within your inventory.
This is done through:
- Real-time product tracking and product management
- Analysis of historical data
- Analyzing the competition and your particular niche
- Customer demand and satisfaction
- And more — which is something that inventory management software like Katana can provide
Optimize your inventory levels with Katana
Katana Cloud Inventory Platform gives you everything you need to track each electronic component in your inventory. Get a demo to see how it all works and have your questions answered.
Tips for effective electronic components inventory management
So far, everything seems clear — you need to implement a good inventory management solution to keep track of your electronic components and avoid things like stockouts or excess inventory (You can find some great options from this list of 7 best inventory management software) That’s great, but how exactly can you achieve that, and what are some tips to keep in mind to make sure you’re on the right track?
Reselling or trading excess inventory
One of the best ways to get rid of excess electronic components inventory is to resell it to other electronic manufacturers to regain some lost capital — a classic win-win situation. You might have to lower the price, though, so you’ll probably end up at a loss, but it’s still better than throwing inventory away and losing everything you paid for it. Another option is to trade inventory with other partners and collaborators, but in this case, the planets really have to be aligned. This means that your inventory needs to be in high demand in other markets, and the products offered in the trade must also work for you, otherwise you’ve solved nothing.
Returning excess inventory
If you have the option to return some of the products that make up excess inventory sitting around in a warehouse, that’s the best possible scenario to find yourself in. Unfortunately, very few suppliers allow cancellations or returns, because it’s also a risky business move for them. However, in some cases, it might be possible, although usually you’ll also have to pay a fee for the return. It’s worth planning ahead and seeing if there are suppliers you can collaborate with that offer this possibility, as it’s a good way to minimize risk in case of market volatility.
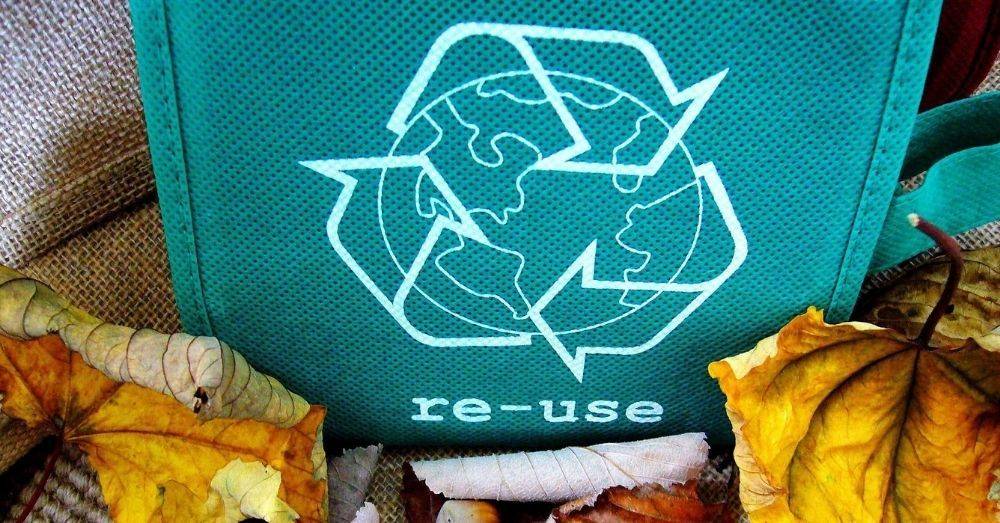
Recycling excess inventory
Recycling is all the rage right now, and for good reason. It’s a win-win situation for businesses, consumers, and, of course, the environment. If some of the electronic components in your excess inventory can be reused or recycled for different purposes, you can use them in a different production line and make the best of the situation.
Optimizing storage space
This goes without saying, but proper storage management is essential in effective electronic components inventory management. You need to make sure you have enough space for all the products in your line, with some extra wiggle room for unsold inventory or new products you might add to your offering.
It’s critical to properly optimize this space, setting up separate areas for incoming inventory, organization, and outgoing inventory, always prioritizing high-demand products, and putting the slow-selling items further in the back. Use whatever tools you have at your disposal to help in this mission, from bins, racks, and shelves, to labeling and scanning products with ease. This way, you won’t lose track of what you have in your inventory, and you’ll ensure efficient order management and customer satisfaction. At the same time, ensuring the right storage conditions to keep products in your inventory from being damaged is also critical, as you won’t be able to get rid of obsolete, expired, or altered inventory without suffering capital loss.
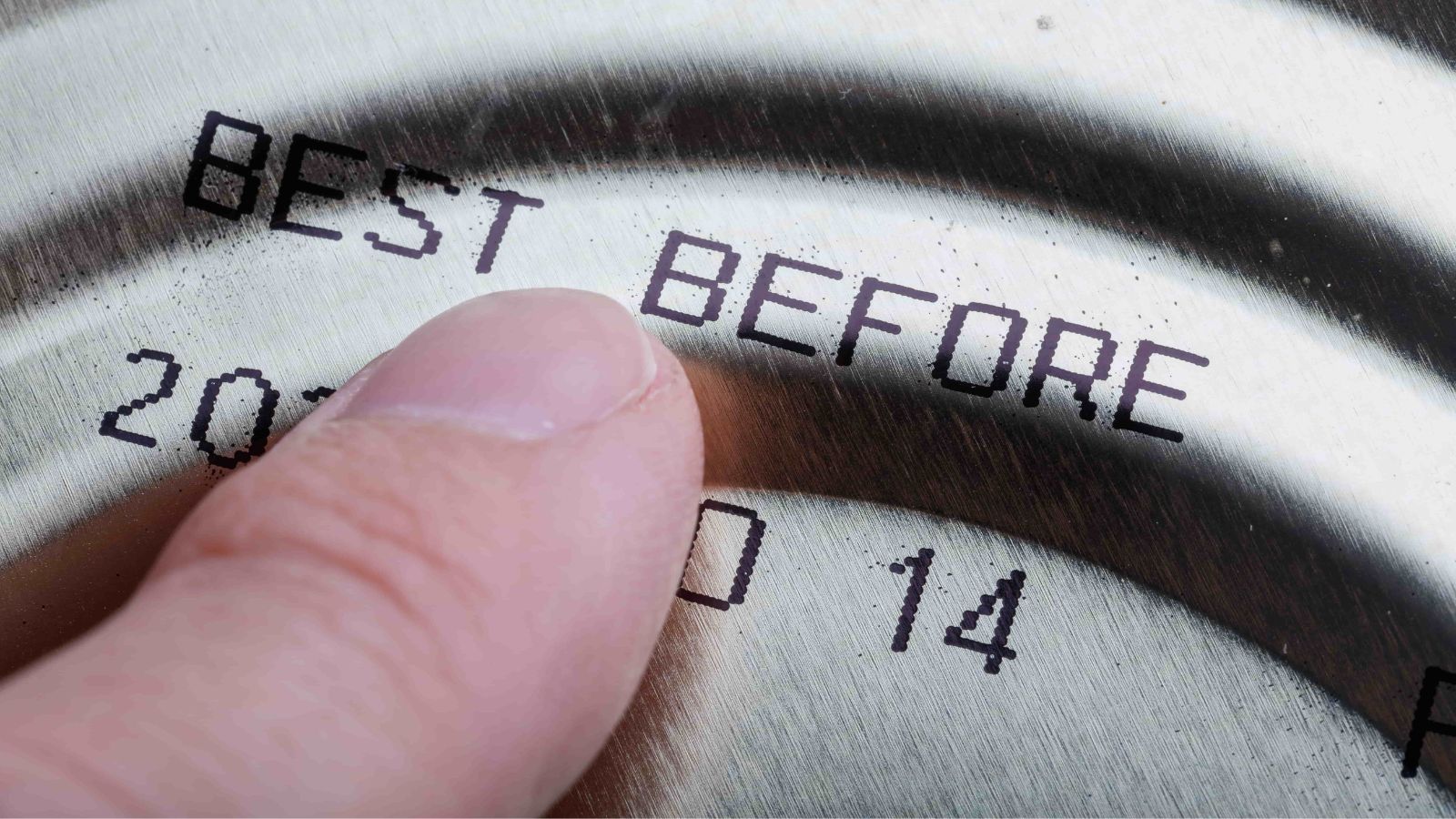
Tracking inventory in real-time
Keeping tabs on all of the products in your electronic components inventory is a no-brainer. Implementing an inventory management software solution like Katana can help monitor the exact location, quantity, status, and expiration dates of all products in real time. Tracking serial numbers, lot numbers, RFID tags, and other similar things can enable visibility throughout the lifecycle of a product, allowing you to make informed business decisions. By properly and accurately tracking your electronic components inventory, you can avoid problems like inventory discrepancies, stockouts, shipping delays, product waste, or obsolescence.
Optimize your electronic components inventory with Katana
To streamline and optimize your electronic components inventory management methods, you need a powerful, reliable partner — enter Katana. It equips your business with the tools and resources it needs to navigate the challenging waters of the high-risk electronic components industry.
With Katana inventory management software, you can lower the risk of disruptions and avoid things like overstocking, stockouts, excess, unsold, and obsolete inventory. Electronic components have a short shelf life because technology is constantly evolving at a fast pace, so keeping tabs on your inventory in real time can make or break your bottom line.
Seamlessly integrate with your existing systems, leverage the power of data to make informed business decisions, optimize workflows and ensure effective order management, and predict shifts in consumer demand to optimize stock levels — you can do all of this, and much more, with Katana.
Get a demo now to see the product in action!

Ioana Neamt
Table of contents
Get inventory trends, news, and tips every month
Get visibility over your sales and stock
Wave goodbye to uncertainty with Katana Cloud Inventory — AI-powered for total inventory control