How to master bottleneck management in production process
Bottleneck management is essential to learn as bottlenecks occur in all manufacturing industries. Here, we explain what bottlenecks are and how to fix them.
Team Katana
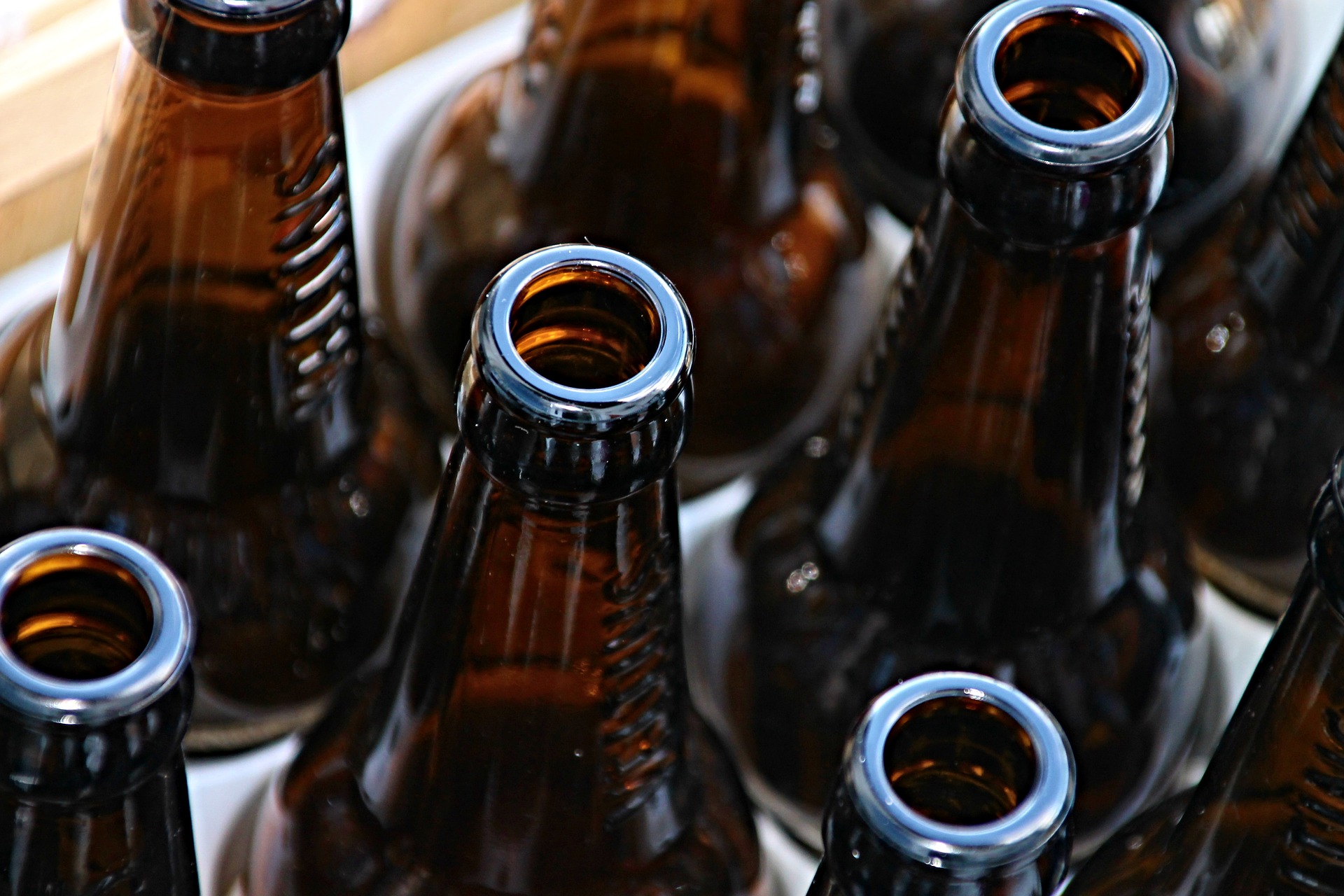
TL:DR: In this article, we’re going to explore the bottleneck definition, examples, and how you can fix them when they occur on your factory floor.
Everything might seem splendid in your manufacturing business, and as you plod along with your operations, you may even take certain issues you encounter at face value.
Perfection isn’t achievable, so why waste resources on trying to chase an impossible goal?
If that is a question you’ve asked yourself, you’re possibly in danger of becoming compliant, which will slow down your production flow, generate waste, and even increase your manufacturing costs.
But have no fear, by reading this article you’ll have taken the first step toward improving your production workflow as we’re going to investigate bottleneck management and how you can do your best to tackle them.
A basic bottleneck definition would be a point along your manufacturing route in which production flow becomes constricted, slowing down or even halting your other production operations.
You might be wondering; bottlenecks exist in which type of manufacturing processes? But every manufacturing business will experience a bottleneck, from horsey-seesaw makers to chemical processing plants.
And a lot of manufacturers just accept that this is an occupational hazard of producing products.
Which is true, a bottleneck in production is inevitable. However, that doesn’t mean you shouldn’t be vigilant and debottlenecking along your production line every chance you get.
So, in this article, we’re going to explore bottleneck management, debottlenecking, and what tools you can use to optimize your productions workflow.
PRO TIP: Want to get an immediate head start on better managing your manufacturing business’s inventory? Then be sure to check out our comprehensive breakdown on small business inventory which will help you on the path to practicing leaner manufacturing processes.
So, without further ado, let’s dig into the bottleneck definition.
What Does Bottleneck Mean in Production?
A bottleneck definition is a congestion point along a manufacturers production line. It’s also a term used in different industries, but for this article, we’re going to look at bottlenecks in manufacturing.
The name, bottleneck, is inspired by the function of a bottleneck (on a wine bottle for example) which is to stop the content of a bottle quickly spilling out should it be knocked over. A bottleneck provides a point in which something passes through slowly.
A bottleneck in production isn’t a congestion point limited to just your production line. A bottleneck could occur from your resources, such as:
- A machine that needs regular maintenance;
- A worker who needs training; or
- A computer with outdated software.
Regardless of where the bottleneck occurs, it happens due to workloads arriving at a stage of production too early or the workstation struggling to handle the workload.
So, as you can imagine, knowing how to identify a bottleneck in production is extremely important to begin the debottlenecking process as soon as possible.
The reason it is important to identify a production bottleneck is that it’s going to greatly affect your manufacturing lead time and increase your manufacturing costs significantly.
According to Eli Goldratt, in his book The Goal, bottlenecks in manufacturing aren’t a thing of evil, just an unavoidable fact of manufacturing that you’ll need to find a solution too.
But before we move on to a bottleneck process example, it should be quickly mentioned that bottlenecks are sometimes confused with manufacturing constraints.
The difference between bottlenecks and manufacturing constraints is that a constraint is a long-term, persistent limiter to your production flow. So, a constraint would be if your processes are running at their maximum output and can’t be optimized any further.
A Bottleneck Process Example
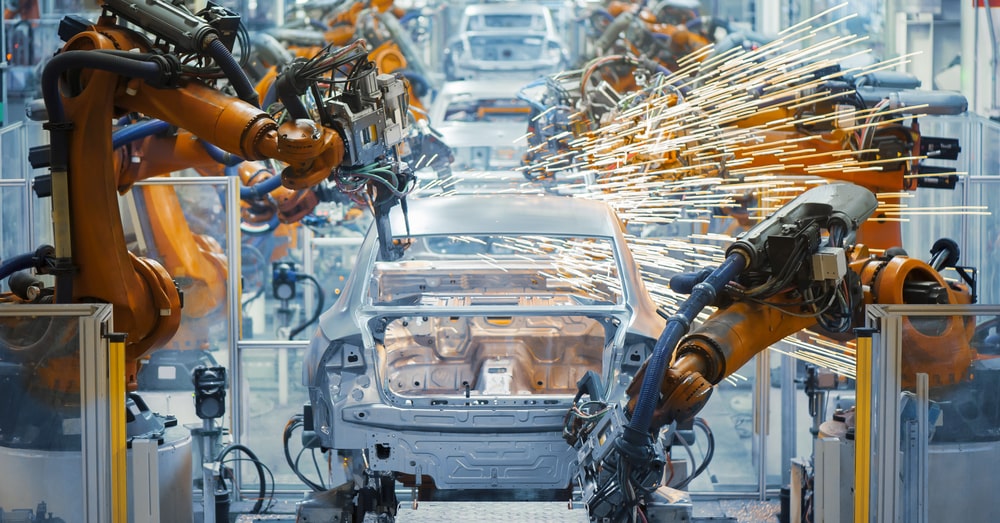
As everyone and their grandmother seems to be an avid gamer nowadays, we’re going to use a bottleneck process example that might be encountered by a vehicle manufacturer, but use the strategic tips offered by an economic simulation/strategy game.
Exciting, eh?
Anyway, let’s imagine you’re in the big leagues, manufacturing vehicles. You use a repetitive manufacturing process to make the chassis and most of the other components needed for the vehicles.
However, you also produce a line of environmentally friendly vehicles which take up a considerable amount of time to install the electronics for one vehicle.
At this stage, it is easy for a chokepoint to form since the other processes have a smooth production flow, but this particular part of the production line has all its resources dedicated to the production, meaning that unfinished vehicles are stuck in waiting before they can be completed.
This part of the factory is where the bottleneck is occurring, and you’ll need to find a solution to deal with this.
And before we delve into the process of what is debottlenecking, below you can find a video from Positech, which details eight production line strategy tips that you can use to optimize your vehicle manufacturing business in their videogame Production Line.
You might be casting a cynical eye, but yes, this videogame presents the same challenges real-life manufacturers often face, and we recommend skipping to minute 7:10 – Tip #5 – Faster Conveyor Belts (aka a way to fix a bottleneck operation).
How to Identify Bottlenecks in Manufacturing
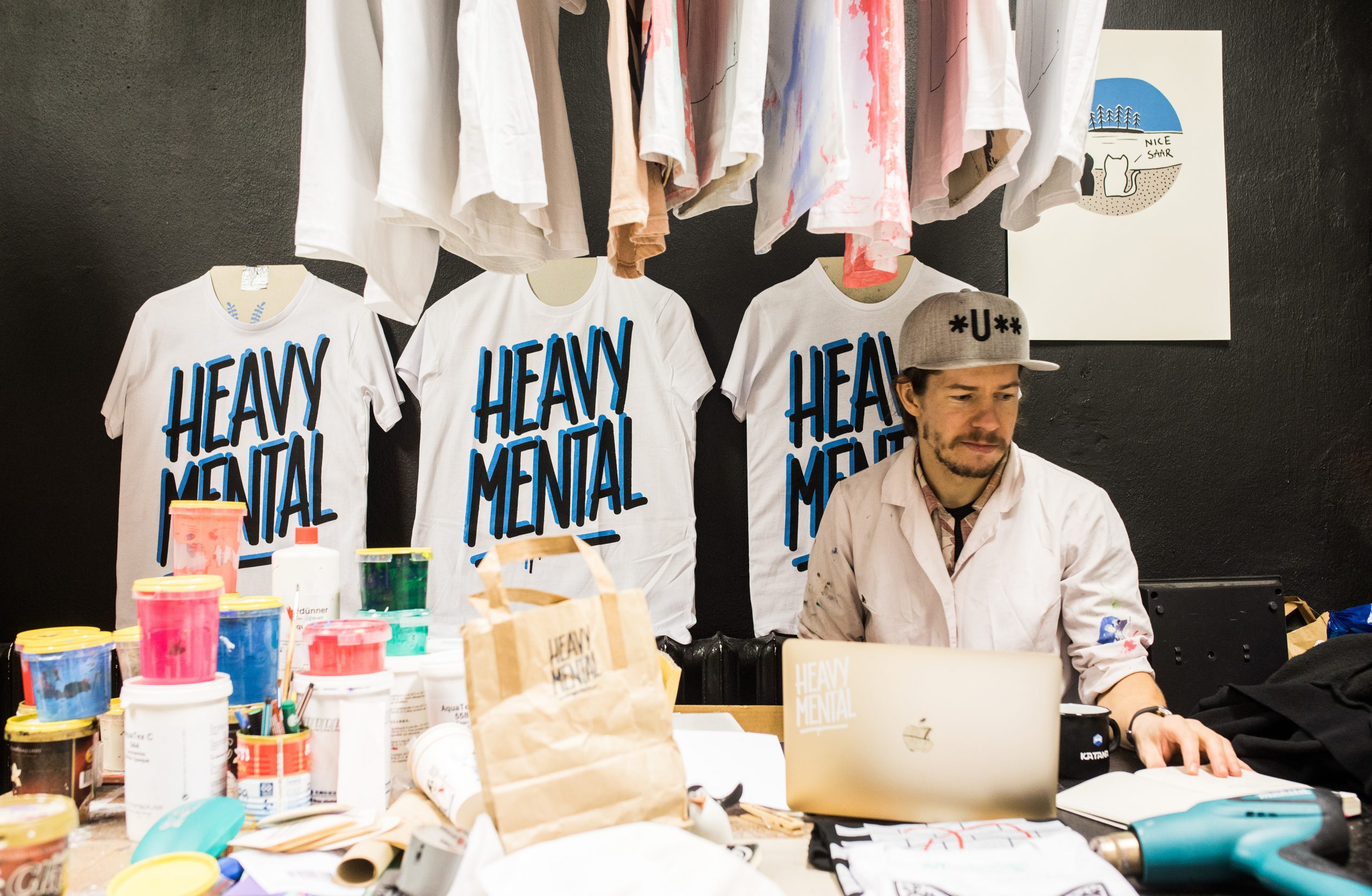
When looking into your production processes, you need to monitor any point which has an unpredictable workflow.
And you can do this by following one of the tactics below when investigating improvements to make to your bottleneck management:
1. Accumulation
Is there a point along your process steps where a long queue of unfinished products accumulates? If you produce only one type of product, it can be easy to identify where the accumulation is occurring because you simply walk along the manufacturing route until you find where the buildup is.
2. Throughput
Another way of identifying where bottleneck manufacturing is appearing is to increase the manufacturing throughput of each of your workstations because theoretically, bottlenecks affect your throughput time, so if a machine is prone to bottlenecks the throughput will increase, and it’ll affect the overall production rate.
3. Full Capacity
Each of your workstations will have a utilization limit. If there isn’t a bottleneck along the production line, all workstations will be operating at a similar capacity, let’s say 50% of its total work capacity. If a bottleneck operation develops, one workstation will be operating at a higher capacity, perhaps 80%, while the percentage of utilization drops at other stations, to 45%.
4. Wait times
Finally, we have wait times, which is a pretty simple tactic to implement for identifying a bottleneck in manufacturing. All you have to do is look at the downtime’s or waiting times for workstations.
A workstation with a long waiting time means the point prior is where the bottleneck is occurring, as the bottleneck process is taking too long to finish an operation and is holding up the rest of the production.
So, once you’ve identified where the bottleneck is occurring, now you need to figure out how to stop the bottleneck resource.
How to Start Debottlenecking Your Business
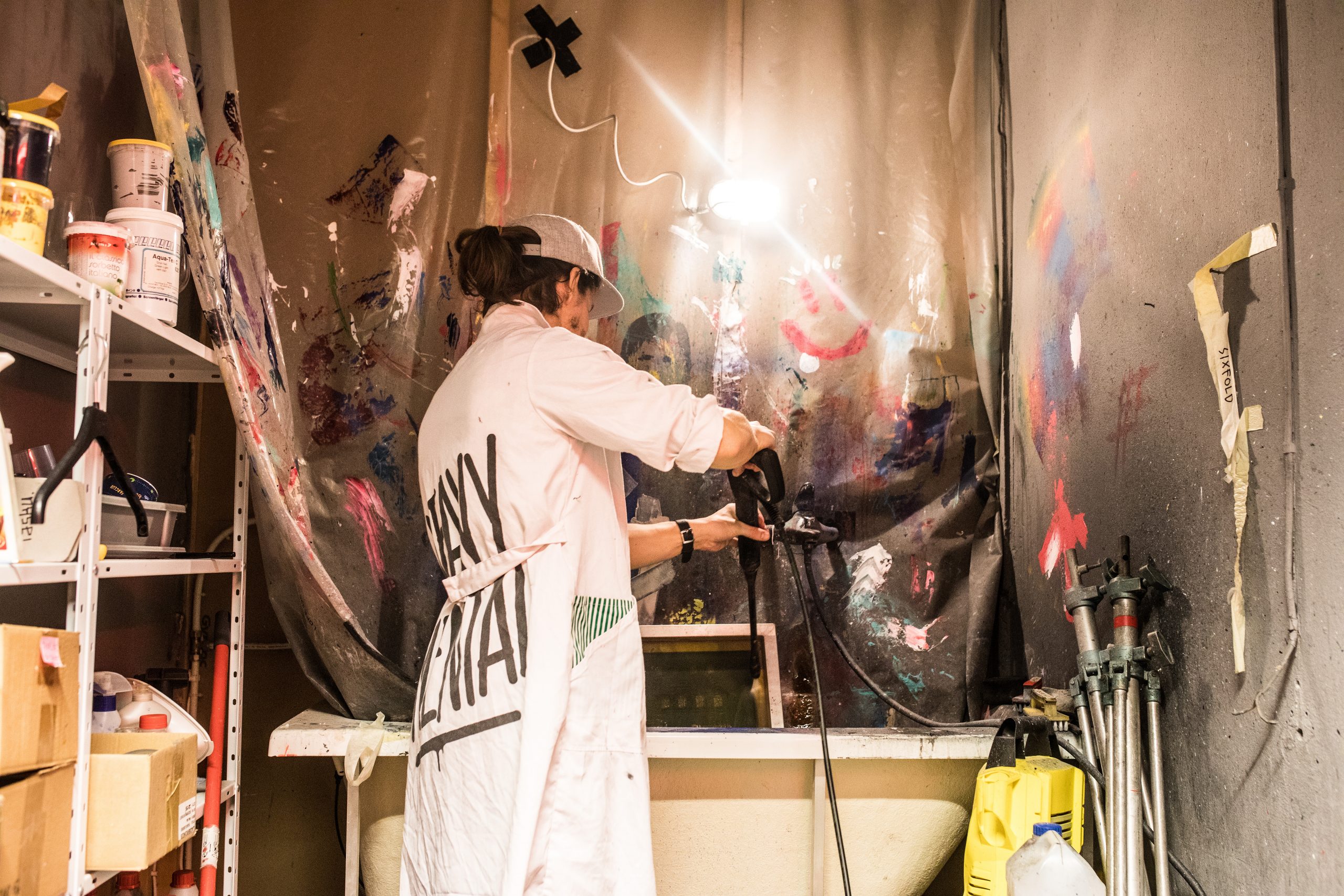
With the know-how to easily identify a bottleneck in manufacturing process, you can now begin the process of debottlenecking.
And, you’ll be happy to know, it’s relatively easy to fix a bottleneck. However, the issue is it will eventually come back, and the biggest challenge is quickly catching it before it drives up your production costs.
But, once you’ve caught it, you can begin debottlenecking by:
1. Redistributing resources
It might be as simple as redesigning the set-up on your factory floor or simply diverting more resources into the production bottleneck. Elevating the capacity (more workers or machines) of the bottleneck could allow the workstation to catch up with the backlog during a high period of demand.
2. Decreasing your resources
It might be that a bottleneck is occurring because your resources are all dedicated to processes which spend most of their time waiting.
For example, let’s imagine you make custom electronic skateboards. You have a workstation that is dedicated to building the board operating at 20%, and a station dedicated to electronics operating at 80%, this would suggest that first station is mostly idle and raising production costs.
3. Subcontracting jobs
Contract manufacturing is the process of hiring another third-party manufacturer to help you manage your workflow and easily remove the bottleneck by relieving pressure from a workstation.
4. Automating your business
Finally, as mentioned several times prior, bottleneck management is a continuous process. Bringing automation into your business, in the form of autonomous machines or a piece of bottleneck software, is going to help you easily monitor your production flow, to identify bottlenecks, and make the necessary arrangements to fix them.
Automation is probably the most important part of tackling bottlenecks.
Yes, you can easily address a bottleneck in production, but the trick is quickly finding it before it does major damage to your profits.
PRO TIP: By adopting a production schedule software into your business, you can quickly identify bottlenecks in manufacturing and develop a production workflow to address this issue.
Cloud Inventory Software for Bottleneck Management
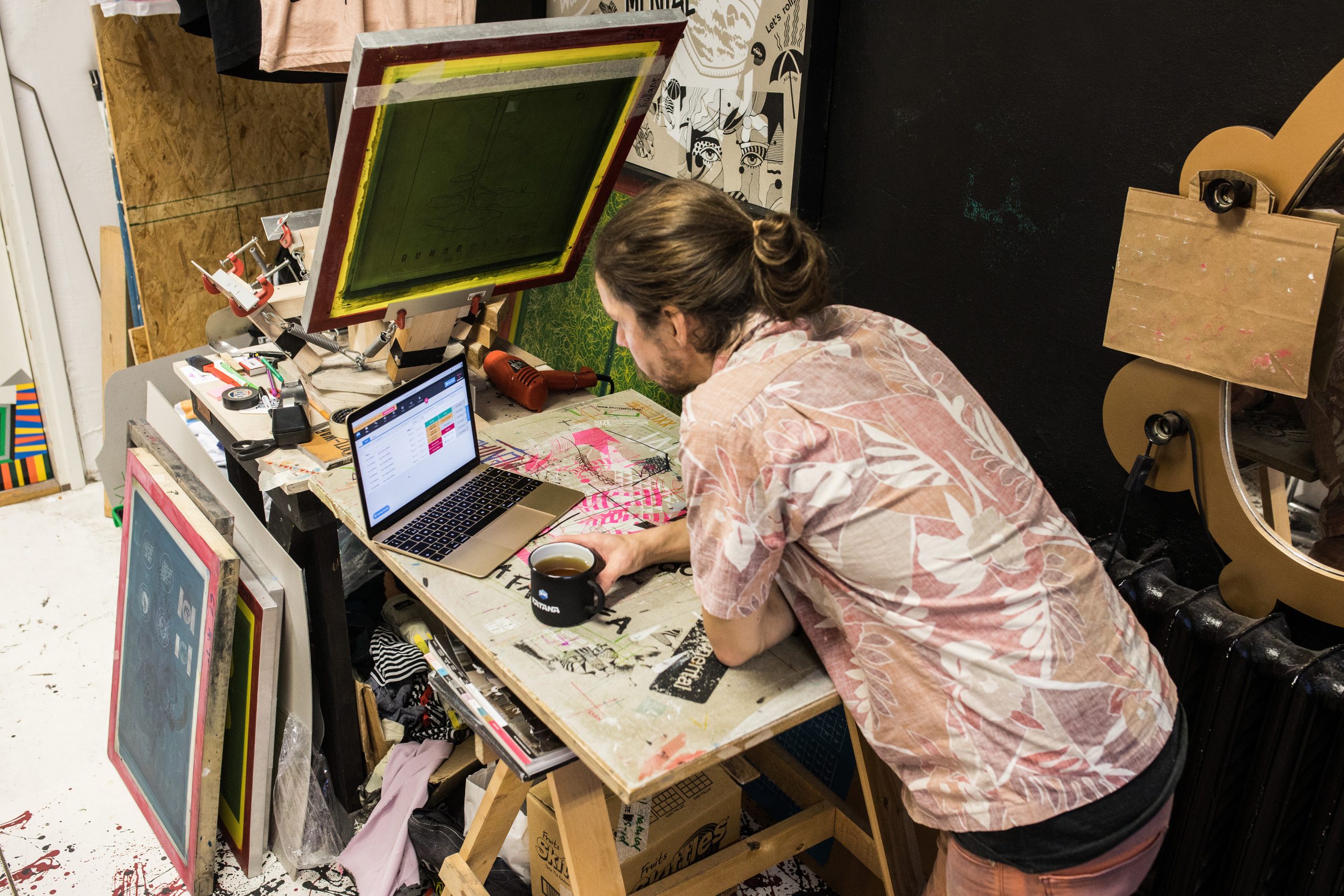
Katana’s cloud inventory software is perfect for helping businesses identify bottlenecks in production.
But how would it assist you? You might be wondering.
Katana can help you begin debottlenecking with its:
1. Visual and Intuitive Dashboard
Katana’s ridiculously easy-to-read, color-coded, visual dashboard centralizes your entire business (from your sales to production), so you can get a quick breakdown of your business’s performance.
Katana also allows you to organize your resources with its task list, so you can track the progress of an operation, and quickly determine if a bottleneck is occurring.
2. Priority-Based Production Planning
Katana’s nifty drag-and-drop feature allows you to easily reconfigure your production schedule in case you notice that a bottleneck is slowing your entire workflow. That means you can continue to fulfill orders as you implement a solution to the choke point.
But, to make things easier for you, Katana has a unique real-time master planner, which means if you do reorganize your workflow, Katana will redistribute allocated and available inventory, following the new workflow.
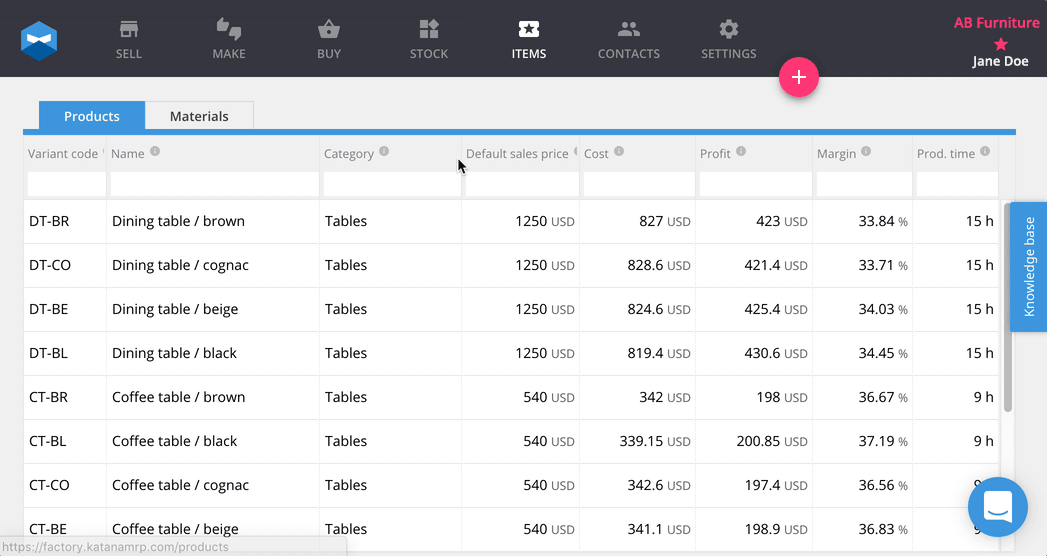
3. Smart Inventory Management
Get complete control over your finished goods and raw material inventory to avoid the most common bottleneck issue of all, material acquisition. With Katana, you can know exactly if you have enough inventory to fulfill orders and immediately place orders for manufacturing or more material should stock levels begin to drop to avoid a production stoppage.
If you want to know more about how Katana works, be sure to check out the video below:
Conclusion
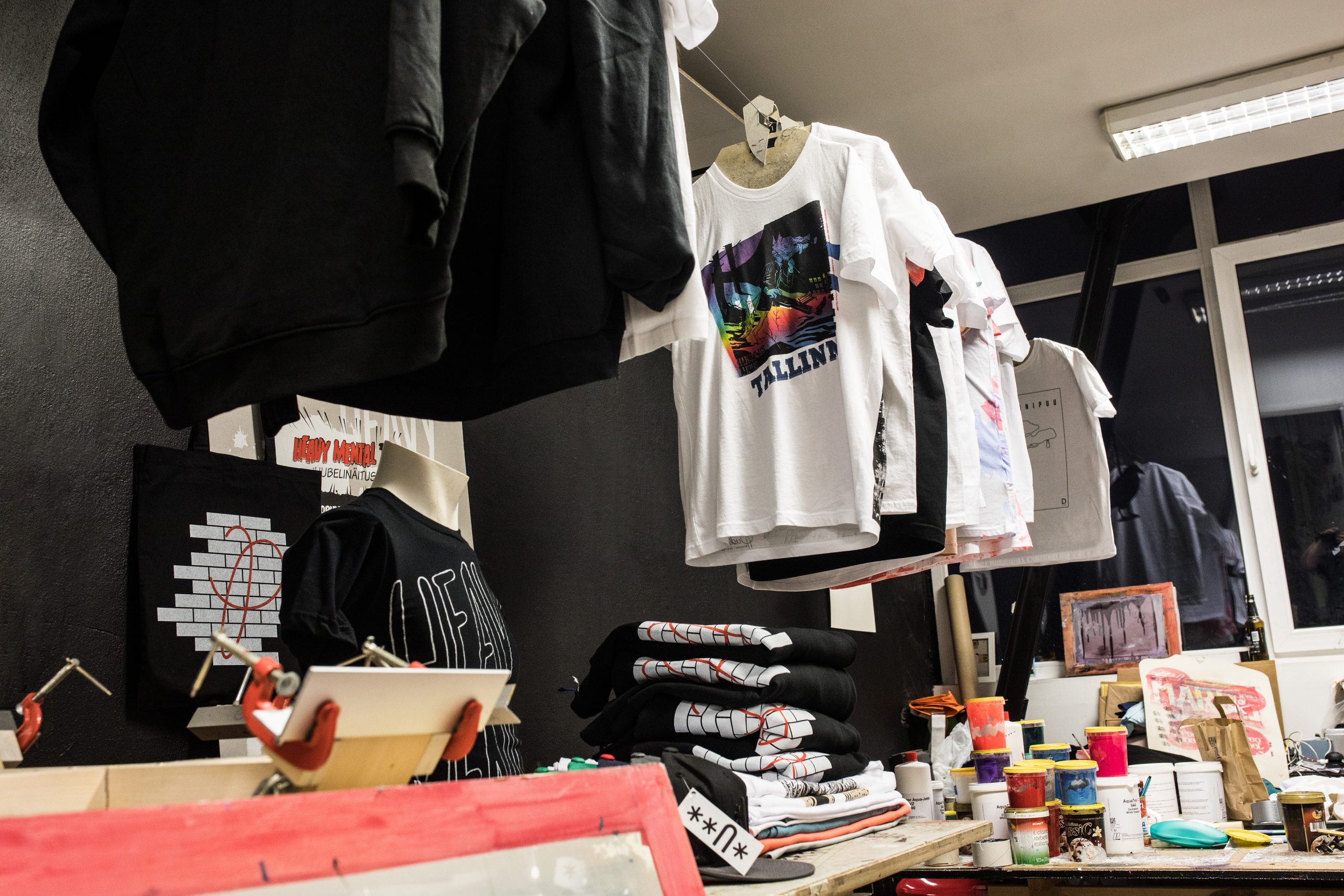
So, if you diligently followed along you should now understand that a workstation in a process is a bottleneck if its capacity is being pushed more than other workstations and the waiting times on products during this stage of manufacturing is high.
Yes, according to the bottleneck definition, this is an unavoidable fact a manufacturer must learn to overcome.
But, always remember what is the principle of bottleneck management? To reduce the effect of congestion on your factory floor.
If you can master detecting a bottleneck as it forms, you can quickly use the above solutions to debottleneck.
And the best way to monitor your production workflow is to implement inventory software like the one offered by Katana.
To see it in action, reach out to our sales team and request a demo.
We hope you found this article useful and until next time, happy manufacturing.
Team Katana
Table of contents
Get inventory trends, news, and tips every month
Get visibility over your sales and stock
Wave goodbye to uncertainty with Katana Cloud Inventory — AI-powered for total inventory control