A quick guide to bill of materials (BOM) inventory management
Discover the pivotal role of the bill of materials (BOM) in inventory management. This blueprint outlines raw materials and components, streamlining production and guiding businesses through the complexities of supply chain management.

Ioana Neamt
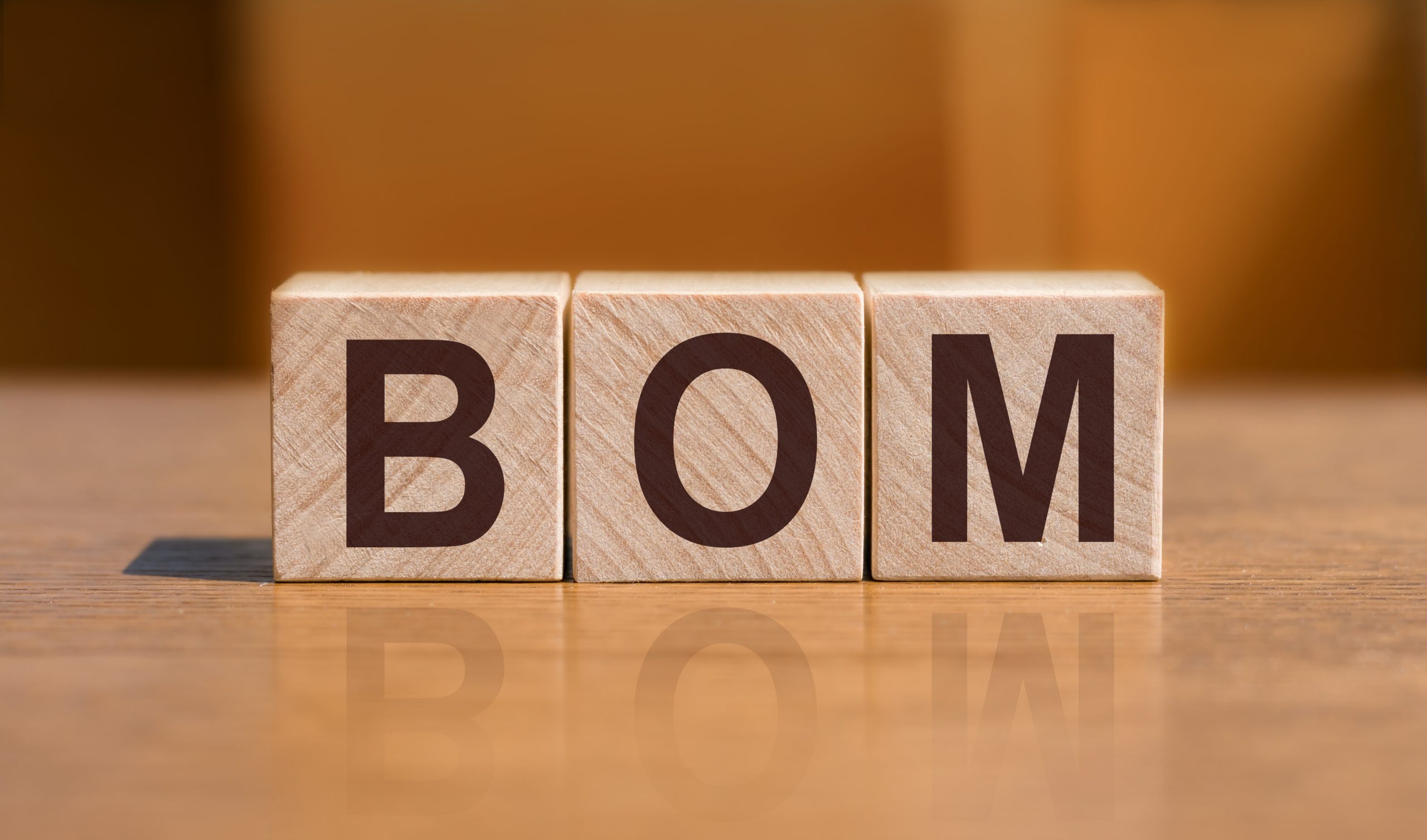
Managing inventory is like a complex game of chess, where you’ve got to plan ahead and keep track of all your moving parts at all times because any misstep could throw you off your game. This is where a bill of materials, or BOM, can come to the rescue and help you keep your business organized and your processes streamlined and optimized for success.
Using a bill of materials for your inventory management needs can unlock various opportunities and save you a lot of time and effort in the long run. But it’s important to know how to use it to your advantage, otherwise, it might become just another time-consuming, stressful task on your endless to-do list. How can you achieve that?
What is a bill of materials (BOM)?
First things first — what is a bill of materials, and why do you need it for your business? A BOM is essentially a comprehensive list of components, raw materials, assemblies and sub-assemblies, and any other parts needed to manufacture a product.
Think of the product as a dish you want to cook: the BOM is the list of ingredients and tools you’ll need to get the job done. So, naturally, you want to make sure your list is complete and accurate because using the wrong ingredient or skipping a crucial ingredient entirely might result in something that your tastebuds will not be too happy with.
Just like a cooking recipe, the BOM will include the basic instructions to use the ingredients (aka materials) and the techniques required to combine them.
As an example, think of a mountain bike manufacturer that wants to produce 1,000 bikes. The BOM will include all the basic parts, components, and accessories required to build it, from chains, pedals, handlebars, and seats to brakes, wheels, tires, mudguards, and more. The BOM will also include the quantities for each part or component, along with the costs.
The importance of a BOM
We think that by now, the importance of having a BOM for any product you manufacture is crucial to running a successful business and ensuring customer satisfaction.
A well-structured, detailed, and accurate BOM will help you plan and schedule purchases of raw materials, estimate costs, manage inventory, reduce waste, and much more.
By enabling transparency into what is needed to produce the items in your inventory, you can keep track of your inventory levels in real time and gain visibility into the entire production process.
Forecasting for bill of materials inventory
Look, you’re not Nostradamus — you can’t predict the future and know where your industry and your market will be in 10 years, or even five. But you can anticipate certain shifts in market trends or consumer demand, highs and lows related to seasonality, and other similar situations.
Using a BOM is crucial for this purpose because it allows you to forecast fluctuations in demand and order the right amount of components to ensure you can meet this demand. This, in turn, will enable you to prevent issues like overstocking or stockouts.
A BOM is structured like a pyramid, with the finished product sitting at the top and the ‘child parts’ sitting below it. Obviously, the forecast for each component will depend on the existing demand for the finished product because if nobody wants to buy a mountain bike, there will also be no demand for mountain bike gears.
Download a free bill of materials template
This template is a great starting point for creating a BOM that works for you.
Automated BOM inventory management
You need a well-defined BOM to help you get an accurate picture of all the components you need, and there are two ways of going about this. You can go the manual route, using spreadsheets to keep track of stock levels, sales data, finances, and other activities. Of course, this means you’ll need everyone working on your team to fill in that data without error and without delays, and therein lies the problem.
There is no surefire way to eliminate the possibility of human error completely, and even the smallest errors could lead to an inaccurate BOM. This, in turn, can lead to a lot of wasted time, a lot of effort required to fill in and manage spreadsheets, delays, lost sales, and other not-so-great scenarios.
So, what’s the other way? Automated BOM inventory management.
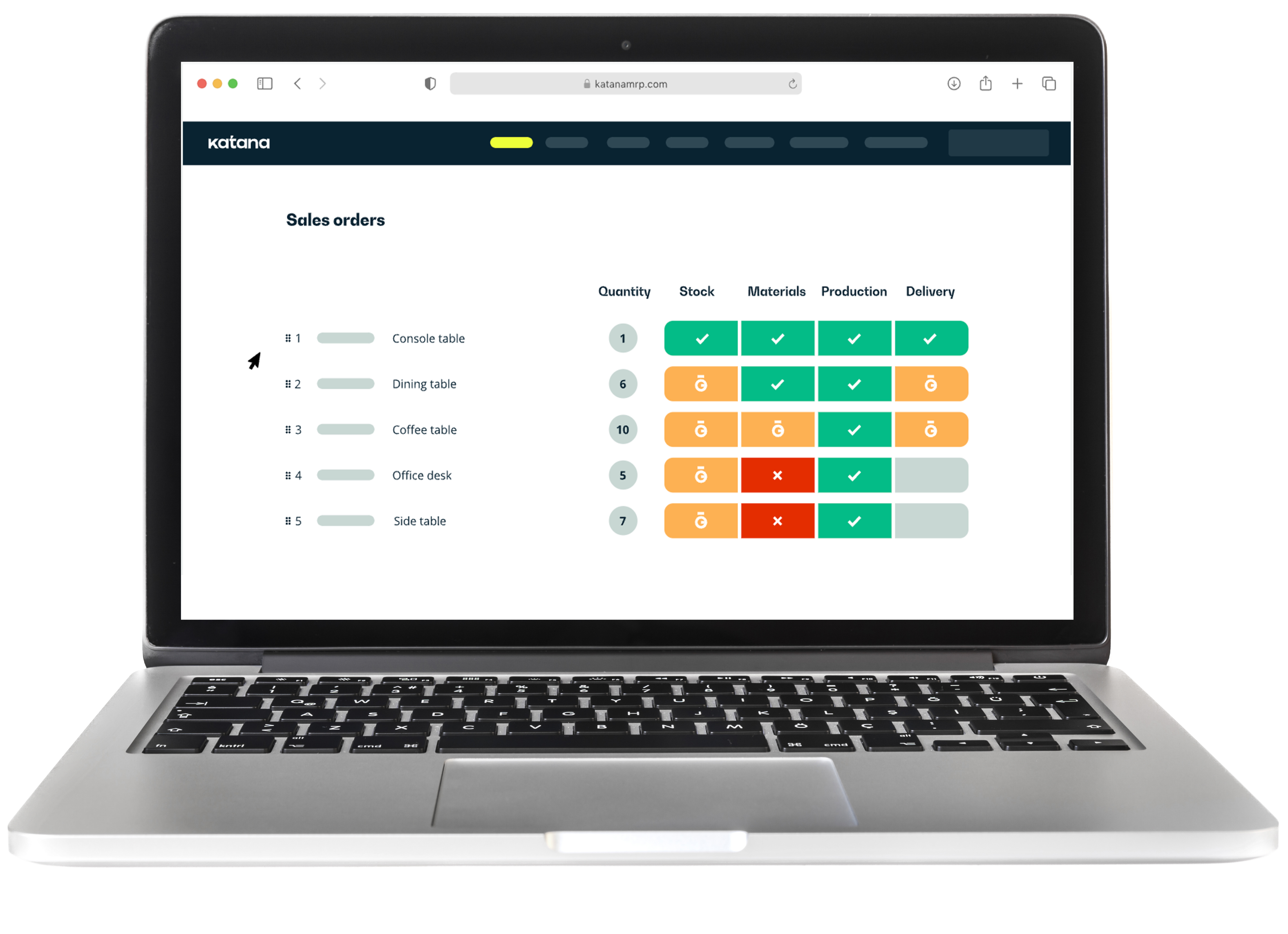
The benefits of automated BOM inventory management
We hate to be the bearers of bad news, but Excels are part of life, and you can’t get rid of them completely. However, in the age of technology, digitalization is your best friend, so why not allow it to take over some of the grueling tasks related to BOM inventory management?
- Accurate forecasts and ordering
An inventory management software like Katana can automate many tasks related to BOM tracking, ensuring that your data is up to date and eliminating human error. Such software can track, analyze, and interpret sales data and inventory numbers to forecast demand and ensure that everything on your BOM list is in stock in the right quantities.
- Improved efficiency
Your staff won’t have to waste valuable time working with spreadsheets to calculate forecasts, freeing them up for other, more important tasks related to inventory management.
At the same time, automated BOM inventory management will give your staff the power of data. Sure, it sounds dramatic, but it’s true. Having access to accurate and real-time inventory data, sales data, forecasts, and consumer behavior data will enable you and your employees to make informed decisions that can streamline processes and boost profits.
- Help prevent stockouts
Keeping an accurate BOM list helps you have a clear idea of the materials you need, the amount you need, and when you need it, based on sales and demand forecasting. This way, you’ll minimize the risk of stockouts and ensure that you are able to deliver your orders in a timely manner and keep customers satisfied.
- Less waste
If sustainability is one of your main concerns, an automated BOM can help you run a lean production process and eliminate waste by preventing issues like overstocking or unsold inventory.
By keeping an accurate and up-to-date BOM, you can avoid production errors and optimize stock levels to ensure you find the right balance between demand and supply.
Download the ultimate guide to inventory management
A comprehensive ebook with everything you need to know about inventory management.
Automate your BOM inventory management with Katana
With Katana, keeping accurate and error-free BOMs becomes easy and stress-free. By implementing our inventory management software, you can keep track of your inventory and manage stock levels in real time, minimizing the risk of overstocking or stockouts.
Take control of your inventory and optimize your bill of materials inventory management with our best-in-class software solution that helps you streamline your operations and keep staff and customers satisfied.
Reach out to our team for more information or to request a demo and see Katana in action!

Ioana Neamt
Table of contents
Get inventory trends, news, and tips every month
Get visibility over your sales and stock
Wave goodbye to uncertainty with Katana Cloud Inventory — AI-powered for total inventory control