Spark notes on how to create a BOM and best practices
Gain a detailed understanding of how to create a bill of materials (BOM), why it is essential to your manufacturing process, and what best practices to follow.

Ioana Neamt
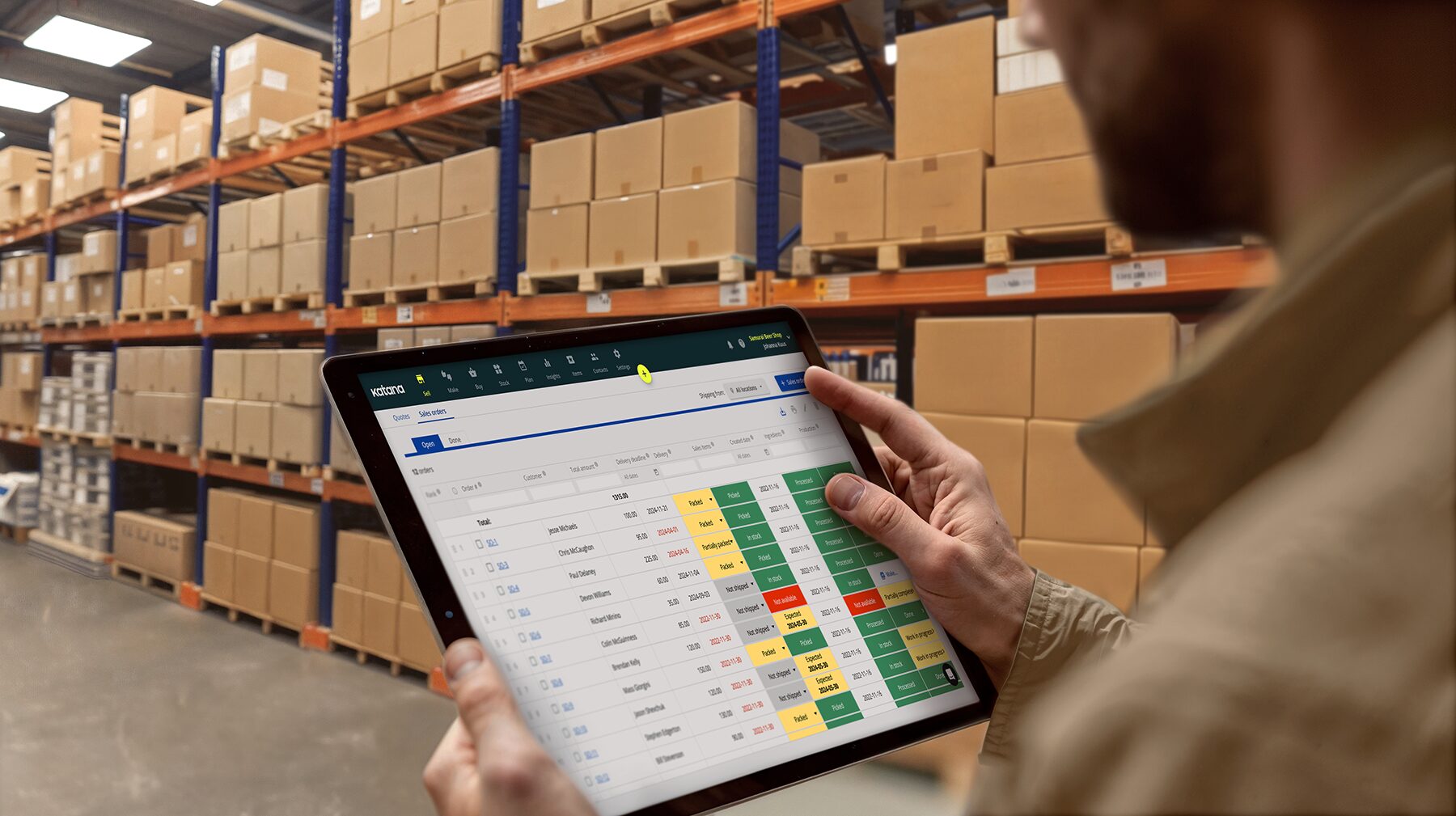
Can you imagine what it would be like to complete a puzzle with no instructions or a complete picture? That is kind of what it would be like to manufacture products without the blueprint — not impossible, but what a headache! With all the potential pitfalls and setbacks of a manufacturing process, you need to be up to speed with and well-versed in any essential tools and best practices that can help your business navigate to sustained success.
The bill of materials is the blueprint to get you there, but it comes with complexities and challenges of its own. Let’s break down what it is, why it is important, as well as what best practices to follow when creating one.
What is a BOM?
Think of a bill of materials as you would of a blueprint — specifically, a blueprint for production. It is an essential instrument that captures information about the quantity, type, and specifications of an item. For any particular product, a BOM lists all of the components, assemblies, and sub-assemblies that go into the manufacturing of that product.
Why is it important to create a BOM?
The bill of materials is a document of extensive importance. It serves in many aspects of your process, including the following:
- Inventory management — Make sure that you have sufficient stock of components available
- Costs — You can have a pretty good estimate of the total cost of the product
- Purchasing — Creating a BOM gives you a good guide for the procurement of necessary materials
- Manufacturing — A BOM can also serve as an instrument of instruction for assembly and production
- Quality control — You can use a BOM to verify the accuracy and completeness of the final product
What should you include when you make a BOM?
The contents of a BOM depend to a degree on the complexity of the product it supports. For instance, in the case of very complex products, a BOM includes not just assemblies but also sub-assemblies.
Consequently, it shows how they are supposed to come together, which means the bill of materials also serves to visualize the product’s structure and how to manage components effectively.
But let’s go through some of the somewhat standard elements that you should include when you make a BOM:
- Item number — Include a unique identifier for each component on your bill of materials
- Description — A detailed description of the component, which explains its function and specifications
- Quantity — How many units are required to manufacture the final product
- Unit of measure — The measurement unit employed to express quantity, such as pieces, inches, or ounces
- Drawing number — This is a reference to the engineering drawing or blueprint for a component
- Material — The specific material that is used to manufacture a component
- Supplier — The name and contact information for the supplier of a component
- Lead time — An estimated time that it takes to obtain a component from its respective supplier
- Costing — The unit cost of a component
- Revision level — This is to specify any subsequent changes or updates made to the BOM
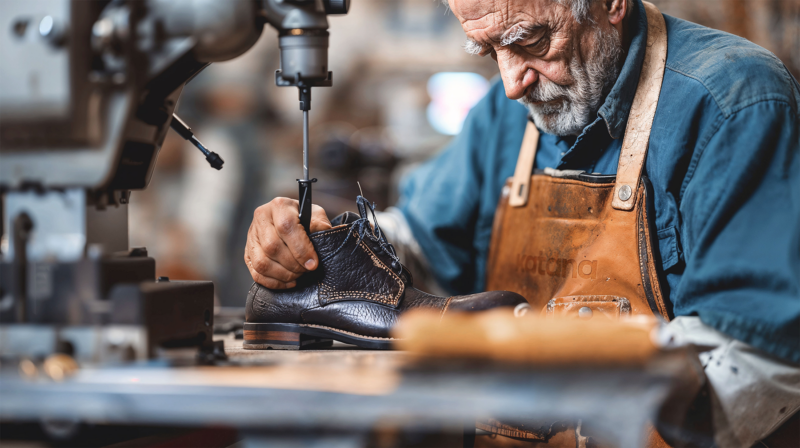
What you should know before creating a BOM?
There are, of course, some factors to consider before making a bill of materials, so that the BOM you create is efficient and accurate enough to support the successful manufacturing of any product. Specifically, it would be in your best interest to have a good understanding of the following:
- Product design — You should be very familiar with the complete specifications, dimensions, and functionality of the product that the BOM supports.
- Manufacturing process — It is also essential to understand the steps involved in making the product, down to methods of assembly and equipment required.
- Availability of components — You should have a good idea of the general availability and lead times for all components that go into making the product, including details such as potential suppliers and appropriate alternatives to fall back on.
- Cost — It is important to be well aware of the budget that can be made available for the product’s manufacturing, as well as the target sale price.
- Quality standards — Be clear on the desired level of quality, as well as any relevant industry standards or certifications required.
- Regulatory compliance — It is also essential to be up to date on any applicable regulations or certifications that your product and the manufacturing process have to meet.
- Inventory management — Having BOM inventory management ensures you always know the current stock levels of components.
- Risk assessment — Take into account any potential risks and challenges associated with the product’s manufacturing process and associated supply chain.
BOM management software
Katana is a cloud-based inventory management software that makes creating BOMs easy. Get a demo to learn more.
EBOMs vs. MBOMs: what are their differences?
EBOM and MBOM refer to two kinds of bills of materials that are used in product development and manufacturing. EBOM stands for engineering bill of materials and it serves to provide a general overview of the components required for a product. MBOM stands for manufacturing bill of materials and its purpose is to provide the specific instructions and information that are required to manufacture the product.
There are three main differences between an EBOM and an MBOM:
- The level of detail — MBOMs are more detailed than EBOMs, as they focus on the specific requirements of the manufacturing process.
- The purpose of the document — EBOMs support product design and development, while MBOMs are used for production planning and execution.
- The document creator — EBOMs are created by an engineering specialist or team, while MBOMs are created by a manufacturing specialist or team.
To put this in a more practical perspective, let’s look at what each of them would include. An EBOM breaks down all components, assemblies, and sub-assemblies required to design and manufacture the product and would contain such information as:
- Item number
- Description
- Quantity
- Unit of measurement
- Drawing number
- Material
- Supplier
- Lead time
- Cost
- Revision level
Meanwhile, an MBOM builds on that and offers a more detailed picture that supports the manufacturing process and would include information like:
- Assembly sequence
- Manufacturing instructions
- Tooling or equipment requirements
- Inspection criteria
- Work-in-process (WIP) inventory levels
Download a free BOM template
If Excel is currently sufficient for you, feel free to download this free BOM template to get you started.
Best practices to follow when creating a BOM
As we have established, it is important that a bill of materials is accurate, comprehensive, and supports the efficient manufacturing of a product. So, what are the BOM best practices that you should always apply for best results? Let’s go over some of the key guidelines, below.
- Clarity and consistency
- Accuracy and completeness
- Hierarchical structure
- Supplier information
- Cost estimation
- Version control
- Digital tools
- Regular review and updates
1. Clarity and consistency
You should assign a unique identifier to each item of the BOM, so that it is easy to follow and you avoid confusion. It is important to use brief and descriptive language when defining each component. Be consistent with units — make sure that all quantities are measured using the same units. Additionally, make sure you adhere to a consistent standard format for BOMs, in order to ensure good or very good readability.
2. Accuracy and completeness
Always double-check to verify the accuracy of quantities so that you avoid facing either shortages or excesses. Make sure that all necessary components are listed, no matter how small — don’t leave out items like fasteners, gaskets, and labels. Additionally, remember that revisions are your friend! You should regularly review and update the bill of materials to reflect any changes in the design or manufacturing process.
3. Hierarchical structure
Use assemblies for complex products — break down components into assemblies and subassemblies so that your BOM is well organized. Make good use of indentation for an easy-to-follow visual representation of the hierarchy of components.
4. Supplier information
Include supplier details, such as the name, contact information, and lead times for each supplier of any item listed. Make sure you regularly evaluate supplier performance so that you always employ the highest reliability and quality.
5. Cost estimation
It is essential to work with accurate cost data for each component in order to have a good estimate of the total product cost. Don’t forget to consider cost drivers such as quantity, material, and the manufacturing process, throughout.
6. Version control
It is healthy for your process to diligently track all changes to the BOM and maintain different versions for reference. To that end, it is very useful to employ version control software to help you manage BOM revisions effectively.
7. Digital tools
Employing specialized BOM software helps you automate tasks and improve accuracy. It is also important to integrate the BOM with other systems for seamless data flow, such as with an enterprise resource planning (ERP) or product lifecycle management (PLM) tool.
8. Regular review and updates
Regularly review the BOM to catch any potential issues and identify areas for improvement in a timely manner. It is also important to keep the BOM up-to-date with any design changes or modifications to the manufacturing process.
Master your BOM management with Katana
It’s easy to manage production, procurement, costing, and more with bill of material software designed by Katana. We understand that the success of any manufacturing business hinges on the quality of inventory management and production, so we offer the tools you need to run the best business you can.
Our bill of materials software supports you not only in real-time master production planning, production scheduling, and raw materials management, but can also enable you to manage your entire business.
- By centralizing your business to one easy-to-use platform, you save significant time and money in the long run
- Our software serves manufacturers both big and small to track production progress, changes to design and engineering, as well as usage of raw materials
- Meet deadlines effortlessly with automated allocation of raw materials and products, as well as live insights on resource optimization and production scheduling
- Make the most of costing features that were built for precision and accuracy
- Create your own workflows and integrations between Katana BOM software and third-party tools
Contact us for a demo to find out all the ways in which Katana software can support the success of your enterprise.
FAQs
This document is essential in product design, manufacturing, and inventory management. You compile a very detailed and comprehensive list of everything that goes into a product, as well as how that product comes together. Digital tools such as the bill of materials software from Katana are an excellent aid in creating accurate BOMs.
In enterprise resource planning, a bill of materials defines the structure of a product by detailing and describing all of the components, assemblies, and subassemblies (if that is the case) that are required to manufacture the product.
The bill of materials details every single thing that goes into making a product ready for shipping. This would also include any and all packaging components that are required in order to get the product safely to a customer.

Ioana Neamt
Table of contents
bom-template
BOM template
Get inventory trends, news, and tips every month
Get visibility over your sales and stock
Wave goodbye to uncertainty with Katana Cloud Inventory — AI-powered for total inventory control