What is reverse logistics?
Reverse logistics occurs when a customer returns an item, for any given reason. What happens when the return is processed and the customer receives their refund? Learn about each stage of the process right here.

Ioana Neamt
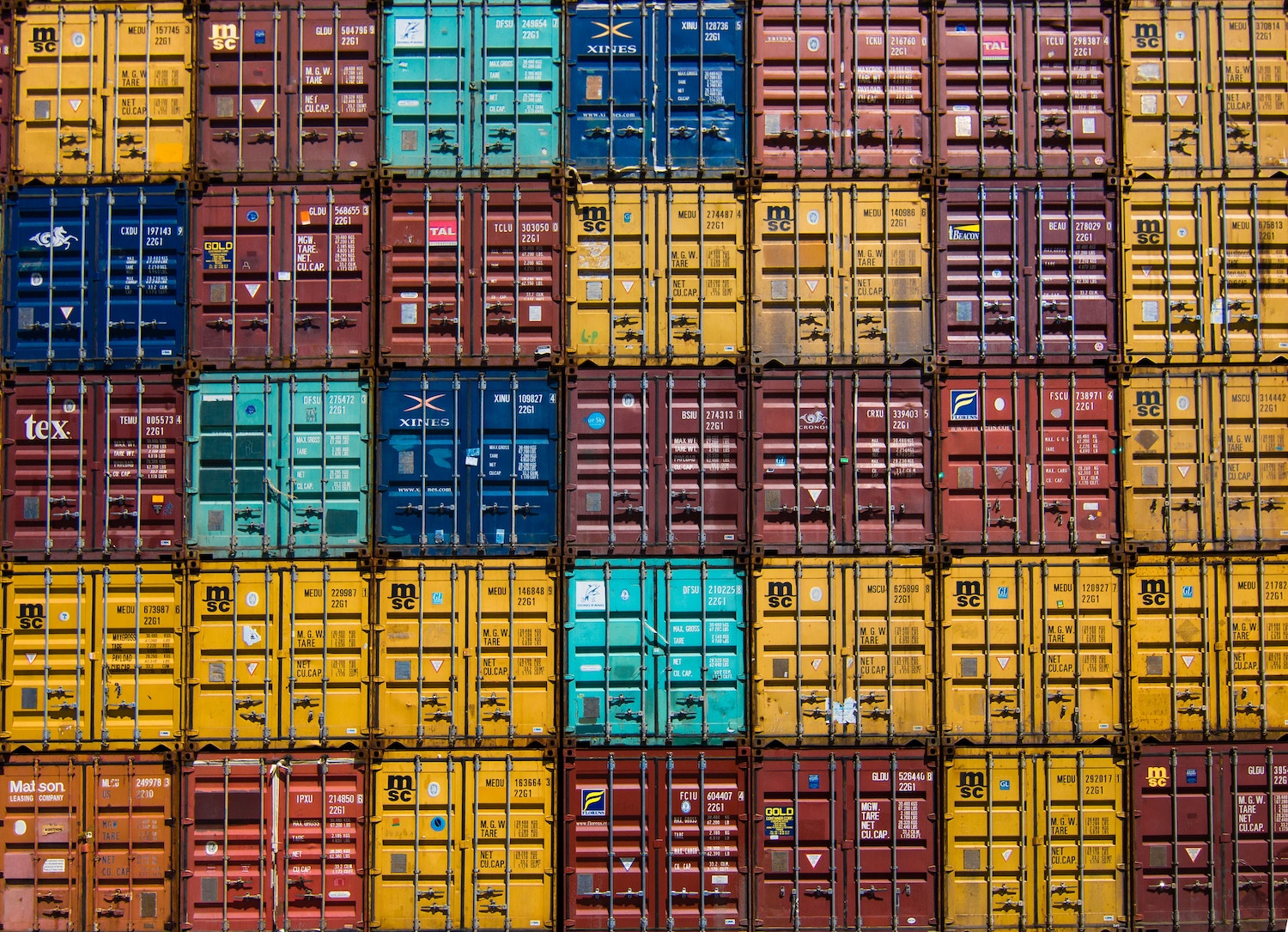
Reverse logistics — it sounds a bit fishy, doesn’t it? If you think it must be something tricky like reverse psychology, don’t worry — the truth is out there, and it’s much more straightforward than it sounds. Basically, reverse logistics simply means what it says: the logistics of reversing an order, aka returning a product to its point of origin.
Reverse logistics is one crucial aspect of supply chain management because, whether we like it or not, not all customers will be perfectly satisfied with their orders. Its purpose is to move the items shipped to the customer back to their point of origin. More specifically, customers send items back to the manufacturer or seller for the purpose of returns, repairs, or proper disposal protocols like recycling.
This guide will go into the reverse logistics process and give you an idea of how complex returning an order really is. You will learn different types of reverse logistics and how the entire process works from start to finish. Let’s give you a sneak peek into a type of supply chain management you might have never heard of before.
Types of reverse logistics
Reverse logistics works in different but not-so-mysterious ways, and the process varies on a case-by-case basis. You could run into a few different scenarios, such as:
Returns management
Stop for a moment and think of the last time you returned something to the store. Do you ever wonder what happens after the transaction is successful or do you just ‘let it go?’ This is one potential scenario when it comes to reverse logistics. In this case, you deal with products that customers return for different reasons, from manufacturing defects to sizing or quality issues.
Next comes the inspection stage of the process, where the returned product is assessed and checked for damages and faults. The inspection takes into account the general condition of the product, as well as the reason for its return. The inspection process is one part of checking for damages while collecting and sorting out all items based on their condition and reason for return.
This type of reverse logistics results in minimized processing times, along with improving the entire returns experience. The main goal is retaining customer loyalty and overall satisfaction.
Remanufacturing
This process entails the disassembly and rebuilding of a returned product. The goal is to return the product to the customer as if it were brand new. The sad reality is that not all returned items come back to the seller in perfect condition, and in some cases, the product has to be ‘spruced up.’ Meanwhile, the manufacturer or seller utilizes this method to reduce waste while keeping resource consumption at appropriate levels.
Recycling
Sustainability is a major focus for companies nowadays and also a crucial aspect that can influence consumer behavior. That’s why so many companies are doing their best to embrace sustainable practices in their business, such as recycling used materials that can be utilized in the manufacturing of new products.
The process entails the extraction of recyclable materials from returned products with the intent of using them in the manufacturing of new items. But recycling isn’t the only sustainable practice that is popular nowadays. Another one pertains to manufacturers that want to create the best quality products without wasting a considerable amount of energy.
The best way to achieve this goal is for companies to invest in technology that makes the production process energy efficient. It is also important for companies to consider utilizing renewable energies in order to reduce their reliance on fossil fuels, resulting in a reduction of their carbon footprint.
Warranty recovery
If a customer returns a product for a warranty claim, then the product will go through a process that entails repairs or complete replacement. The end result is a reintroduction to the market or supply chain.
Asset recovery
This type of reverse logistics pertains to businesses that sell high-value assets. Specifically, this will consist of recovering and redeploying the item once its initial purpose is complete. Companies can hire an agency that handles this purpose by arriving at a specific location to pick up the item. It can be recycled for the purpose of reuse or can be disposed of properly if there is no longer potential for further use.
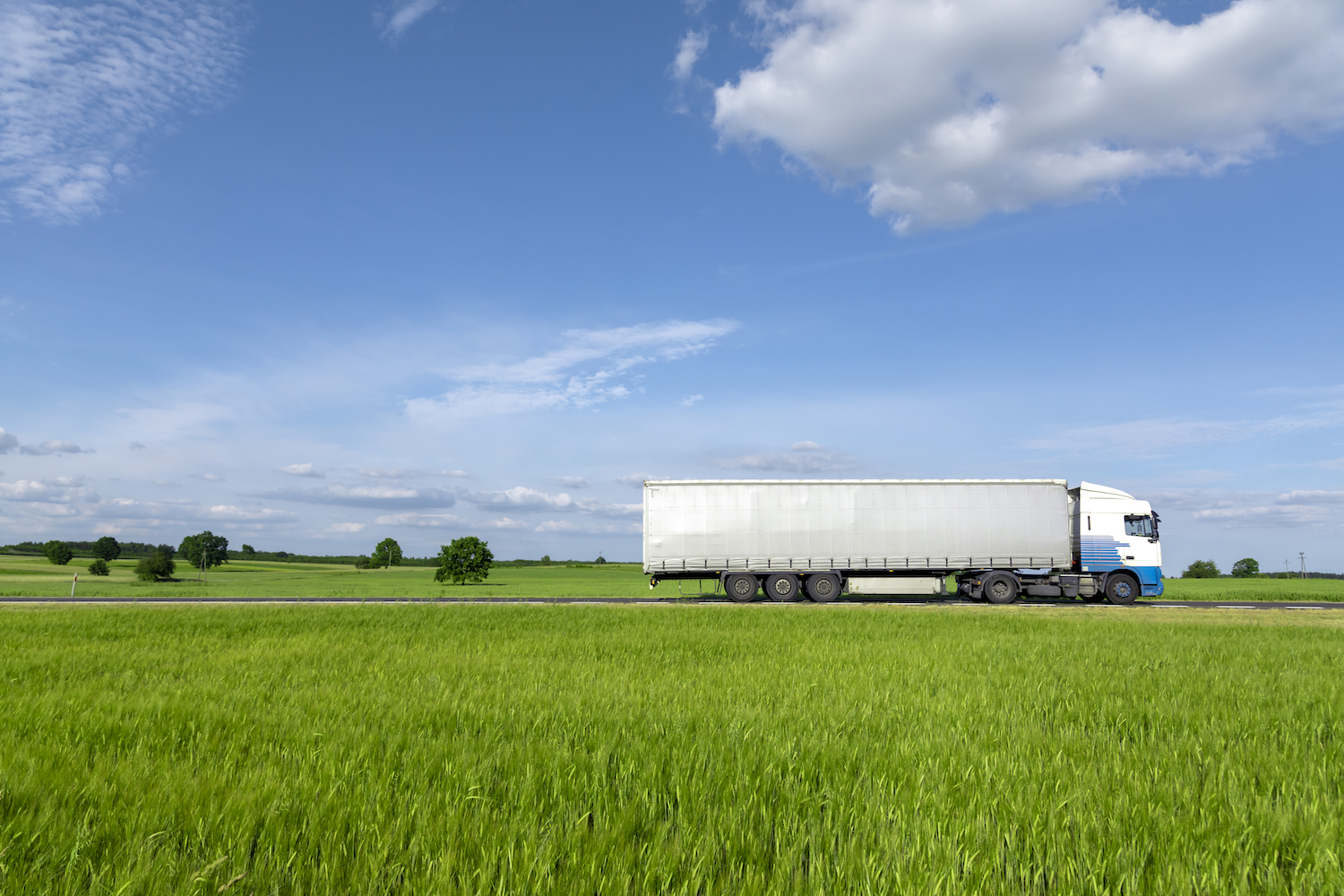
How reverse logistics works
Now, we will be going into the meat of the reverse logistics process. Below is a breakdown of each stage.
Returns processing
This involves returning the item along with an inspection for damage. If the product is in acceptable condition, you approve the refund and return the money to the customer. If necessary, scheduling of pick-up and transportation is also included in this process.
Sorting and inspection
At this point, the returned item undergoes a sorting process based on several factors. Potential outcomes include repairs, reselling as a new item or a return, refurbishing, or proper disposal like scraping or recycling. The next major decision will depend on the categorization of the returned product.
Refurbishing/remanufacturing
The products marked for this purpose undergo the proper procedures. For example, let’s take a look at the refurbishment process. An item that was previously used will need to be cleaned thoroughly. If there are any components that are damaged, they are replaced with newer ones.
Next, the device will be reassembled. If the item is an electronic device, the storage will be wiped clean and returned to factory settings. Finally, the item will be tested for functionality before it is repackaged and back on the market.
The main goal is to restore them to their original or near-original condition, whichever is possible.
Recovery of value
This intends to extract as much value as possible from the product. Possible approaches in this stage of the process include reselling, recycling, or the reuse of some of the product components.
Transport
Now, you’re moving the product back to its point of origin — which may be the manufacturer or the seller. Otherwise, it may go to a facility for refurbishing or a designated place for the next phase of the process.
Disposition and resale
If the product undergoes refurbishment, it is resold on the market as such or returned to the supply chain. The price of the product is either considered “as-new” or reduced to “as refurbished” — whichever is relevant.
Reverse logistics examples
Let’s take a look at examples of reverse logistics at work.
What major brands are doing
Plenty of major brands and global companies are already focusing on reverse logistics as a priority. They do this not only to streamline the supply chain process but also to reduce waste. Here are some examples of major brands and their approaches:
- Levi Strauss — Improving sustainability in textiles by repurposing their jeans, along with recovering and reprocessing fibers for the manufacturing of new clothing
- Kohl — Partnership with Amazon to streamline their returns process, including the screening and returns management
- Procter & Gamble, Unilever, and many more — Utilize reusable packaging for consumers to return after use of products
- Microsoft — Handling products that are no longer functioning due to “end-of-life,” which includes recycling materials for manufacturing use
What various industries are doing
- Automotive industries remanufacture components in order to extend the life cycle of high-value vehicle parts, including engines and transmissions
- Electronic manufacturers recycle old devices while recovering any materials of value and reducing waste
- Ecommerce businesses that manage a high volume of returns will use reverse logistics to minimize losses and expedite the return of items fit for resale.
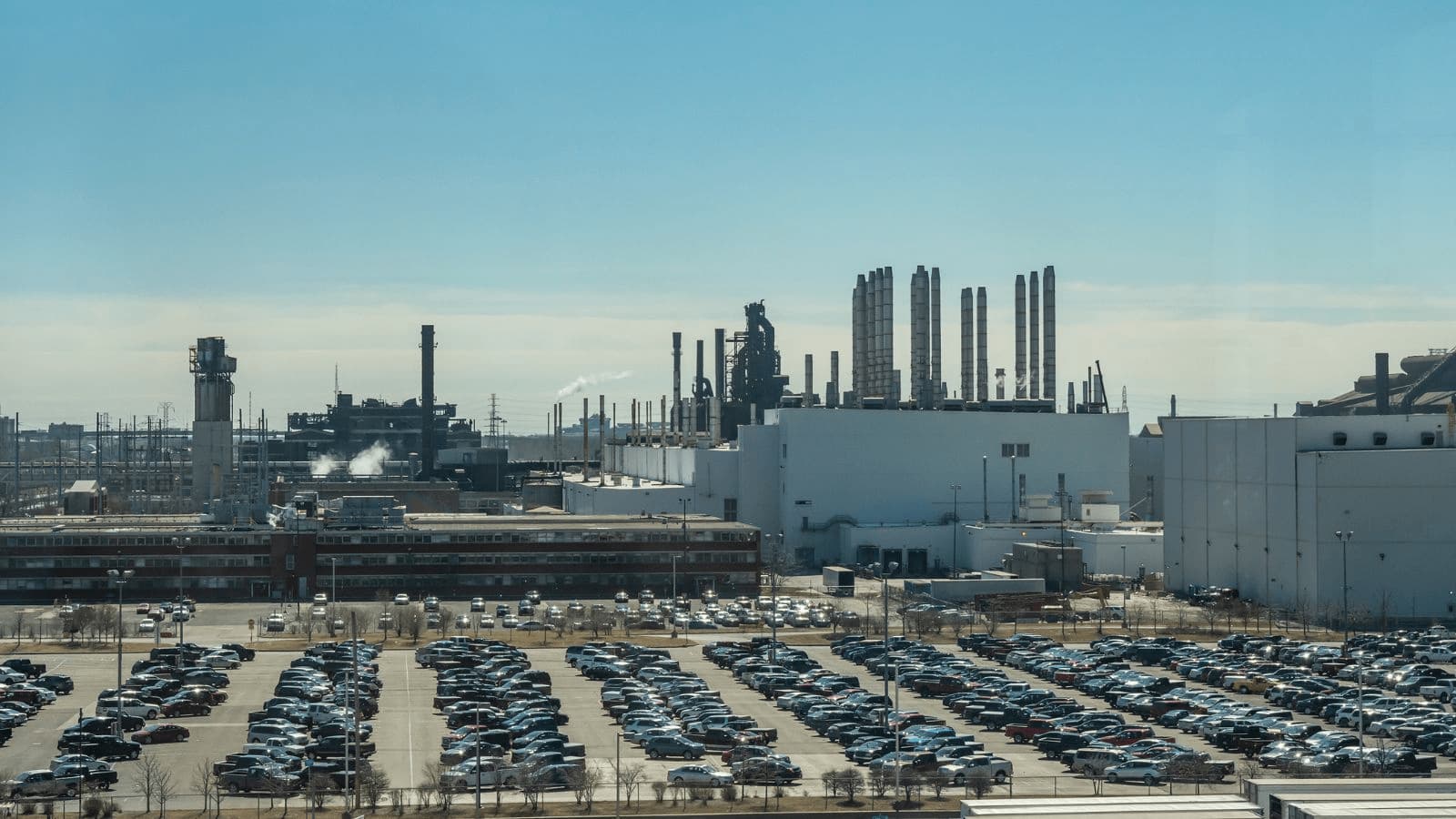
The importance of reverse logistics for your business
Why is reverse logistics important for your business? There are plenty of benefits that you can get out of the entire process. The same applies to your customers, making it a win-win for both parties involved. Let’s go over the benefits it brings.
Enhanced customer satisfaction
Handling returns in an efficient manner is key to customer satisfaction. At the same time, customers expect and appreciate timeliness. So, handling the returns process in a timely manner is key to achieving customer loyalty.
Brand reputation
Your brand reputation is vital because what you do for customers reflects back on you, especially in a situation where reverse logistics comes into play. For example, you could be known for having a return policy that is easy to navigate while getting the job done fast.
Cost savings
Every business looks for ways to save on costs. Reverse logistics makes it possible by way of several methods. This includes the item return process, recycling materials, and reducing waste.
Compliance and regulations
Today’s society is heavily focused on the issue of sustainability. The goal is to make sure every company adheres to environmental regulations to enhance their company’s reputation for the long term. In reverse logistics, this includes the practice of recycling and proper disposal of scrap materials from manufacturing, materials from products no longer in use, and components that have reached their end-of-life stage.
Benefits of optimized reverse logistics
These are the benefits businesses get out of an optimized reverse logistics system:
- Reduced costs — Cost reduction tied to returns, transport, and waste disposal is essential. This allows businesses to recover as much value from returned products as possible.
- Improved sustainability — Using recycling and remanufacturing, a business contributes to the sustainability process. The overall result is reducing waste and promoting a circular economy.
- Enhanced customer loyalty — With a return process that is ‘no frills or fuss,’ the overall customer satisfaction levels rise. This leads to elevated customer loyalty.
- Streamlined operations — Streamlining operations through quick assessment, refurbishment, and reintroduction of products is efficient for all businesses.
Challenges of reverse logistics
While reverse logistics brings forth various benefits and opportunities for businesses across industries, it also poses certain challenges. You know what the kids say nowadays: ‘With great power comes great responsibility.’ Let’s take a look at the following that relate to reverse logistics.
Operational complexity
The reverse flow of returned items can make the supply operations complex. One of the things that come into question is whether or not you have enough space to handle a large influx of returns. Another complexity pertains to time and cost and whether the company can afford it in situations where they deal with more returned items than normal, such as certain times of the year or the end of the holiday season.
Quality control
It is important for businesses to maintain quality standards, and this to the refurbishment process. Keep an eye out for potential inconsistencies that arise during the process so you can prevent customer dissatisfaction while keeping return numbers low.
Transportation and logistics
If you run an ecommerce business, chances are you serve customers across different territories, countries, and even continents — which comes with another set of logistics challenges. They can be in one part of the country that is farther away from a manufacturer or seller. The timing of transportation and logistics differ due to different geographical locations.
Technology integration
Today’s digital world offers technological solutions for product tracking and order management. This will require a significant investment while satisfying the need for seamless integration with any existing systems a business uses. However, while investing in technology can be daunting at first, it will all be worth it in the long run.
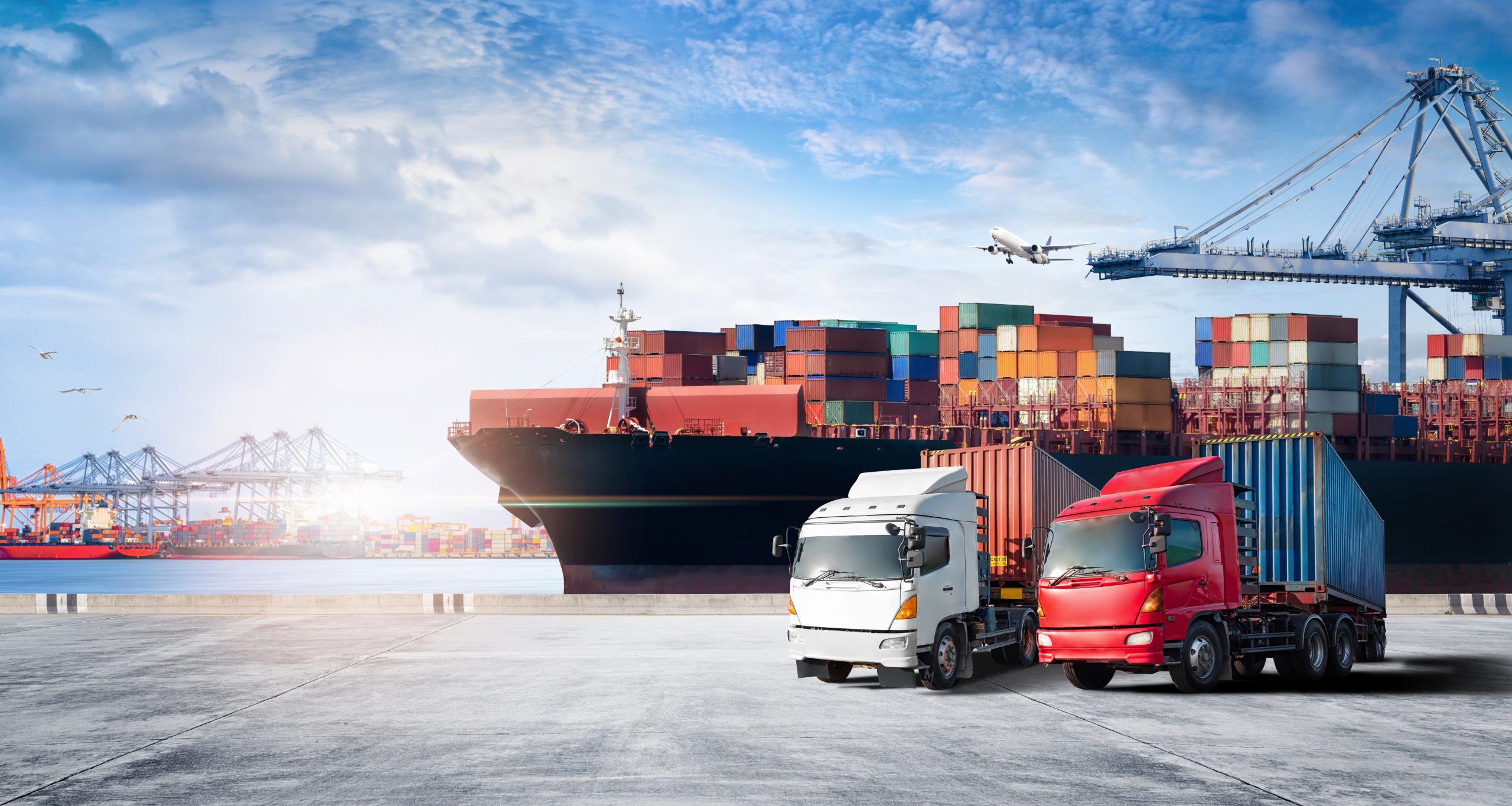
7 strategies to optimize reverse logistics
Did we manage to convince you that the reverse logistics process is a crucial part of any business operation? If that’s the case, then here are a few ways that you can optimize this process to ensure customer satisfaction and keep clients coming back for more.
1. Invest in technology
This includes necessary technology such as tracking and management software to keep an eye on the entire process from start to finish. One such option is Katana, which can really give your business that edge in handling the whole process.
2. Streamline the returns process
Businesses should make the process simple for both themselves and their customers. This includes providing clear instructions for packaging and shipping should the customer decide to return the item for whatever reason. Adding a form allowing the customer to explain the reasons for the return can make the categorization process smoother.
3. Ensure good supplier collaboration
You can work with suppliers and partners that are key to the reverse logistics process. They can be useful in performing certain tasks, such as improving the design of the product, implementing warranties, and waste reduction. It will also make the entire reverse logistics process less of a headache for you.
4. Run centralized return centers
Centralized return centers make the sorting of returned products easier. It will simplify the identification process to determine the best course of action fast. Centralization can help minimize errors — with a common one being items requiring much-needed repairs never getting them due to “false labeling” of certain issues when, in reality, they need to be fixed.
5. Consider logistics and transportation options
Review your current process for logistics and transportation. Decide if it’s feasible to include new processes and transit options. One idea is to see if delivery drivers are able to transport empty pallets while also delivering full ones.
6. Make sustainability a priority
Adopting sustainable practices, such as a recycling program or similar disposal methods that don’t harm the environment, is a must.
7. Automate where necessary
Today’s digital age offers the opportunity to automate any tedious tasks to streamline the entire operation. Consider investing in cloud-based software that serves a specific purpose, such as logistics, asset recovery, or other activities.
How to integrate reverse logistics with Katana
The reverse logistics process with Katana equals simplicity. We can make sure your operation runs smoothly with real-time tracking and data, all in one platform. From shipping to analytics (and everything in between), this software has your bases covered.
It will be a huge help, especially when dealing with the returns, refurbishment, resale, and recycling process. That all equals out to a streamlined process that results in less waste, less money spent, and more customer satisfaction. Reach out to us to learn more and see Katana in action.

Ioana Neamt
Table of contents
Get inventory trends, news, and tips every month
Get visibility over your sales and stock
Wave goodbye to uncertainty with Katana Cloud Inventory — AI-powered for total inventory control