What is continuous manufacturing and can you use it?
Here’s a deconstruction of continuous manufacturing, weighing up the benefits and the risks for a small-scale manufacturer adopting this process.
Team Katana
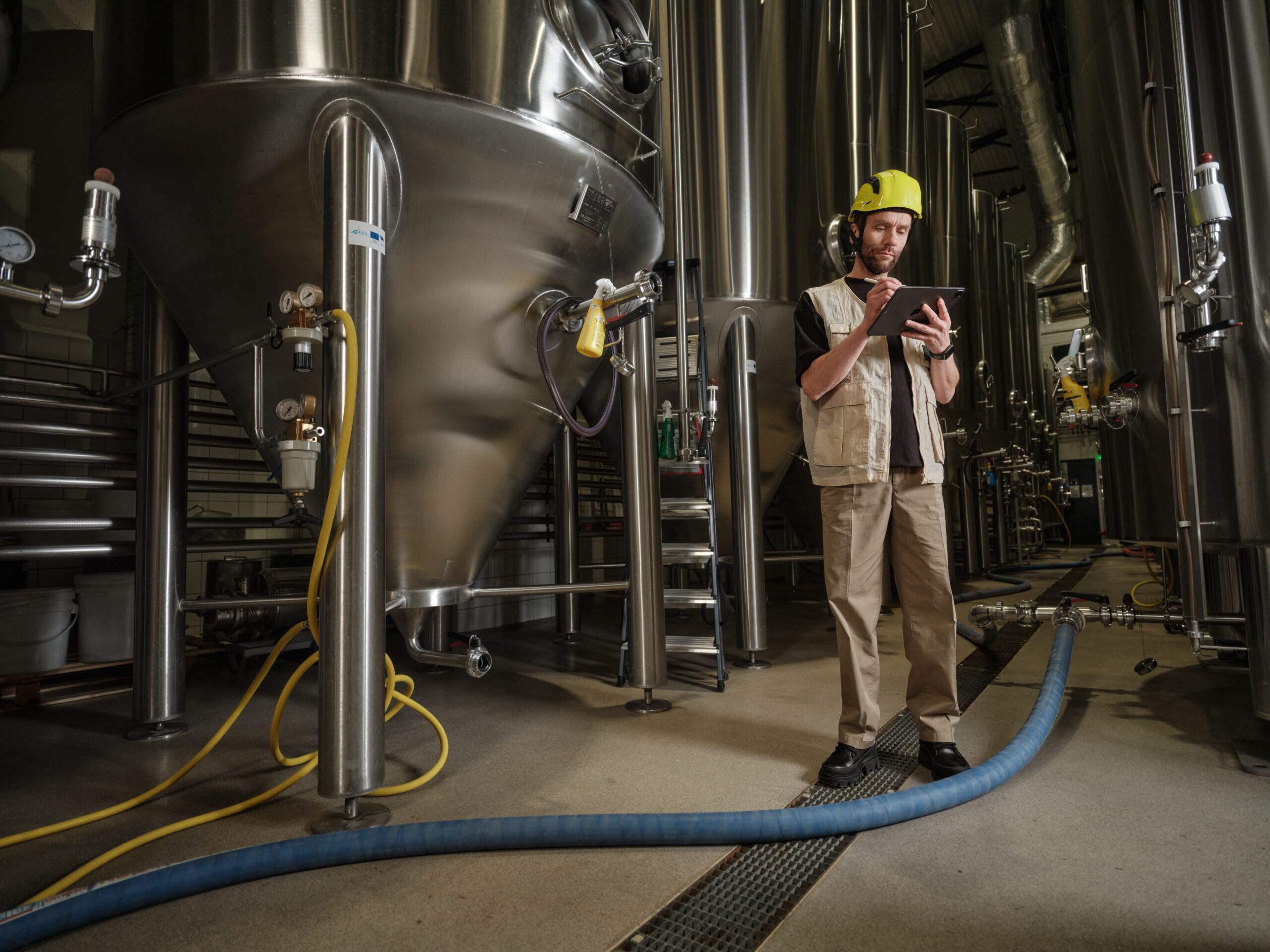
Churning out, conveying, non-stop, lines, machines, rattling, etc. Just a few connotations that spring to mind when thinking about an operation that uses a continuous manufacturing process.
For smaller manufacturers, the non-stop clattering of machinery might not be the best approach to manufacturing products.
But don’t panic, as we can help you find an operation from the five types of manufacturing processes your business can incorporate instead.
However, to satisfy your inquisitive nature, let’s go ahead and look into what is continuous manufacturing.
Take your business to the next level. Production scheduling software tracks your sales and inventory data in real-time to ensure all your teams are up-to-date and have the live insights they need to spot shortages before they cause trouble. Book a demo with Katana, and take your manufacturing business to the next level.
What is continuous manufacturing?
Continuous manufacturing, also referred to as Process Manufacturing (continuous), is a production line that operates 24/7. The raw materials used for the manufacturing process consist of gases, liquids, powders, or slurries. Unlike other production lines that use more physical components like those found in repetitive and discrete manufacturing.
The aim of the continuous manufacturing flow is to produce a flow production to manufacture, produce, or process materials uninterrupted.
The reason it is called a continuous process is that the materials, which can also be fluids, are being perpetually processed. During the process, materials will experience chemical reactions or mechanical or heat treatment.
The difference between continuous manufacturing and process manufacturing (batch) is that instead of different stages of production being handled in a different area or even by another company, the entire process goes through one movement in one location, whilst being monitored for ongoing evaluation to improve the process.
The material is added at point A and leaves as a finished product further down the line at point B. Although, there might be offshoots as the same material can produce different products. The material may enter at point A, with some leaving at point B and the rest leaving at point C, to make two finished products.
We’ll go into this a little later with some examples.
This type of process is used by companies that deal with oil refining, metal smelting, power stations, sanitary wastewater treatment, and many more.
Other industries, such as the pharmaceutical industry, are catching on to the benefits of having a continuous production process where your items can be on store shelves on time, at the lowest possible cost whilst also minimizing waste.
Continuous manufacturing examples
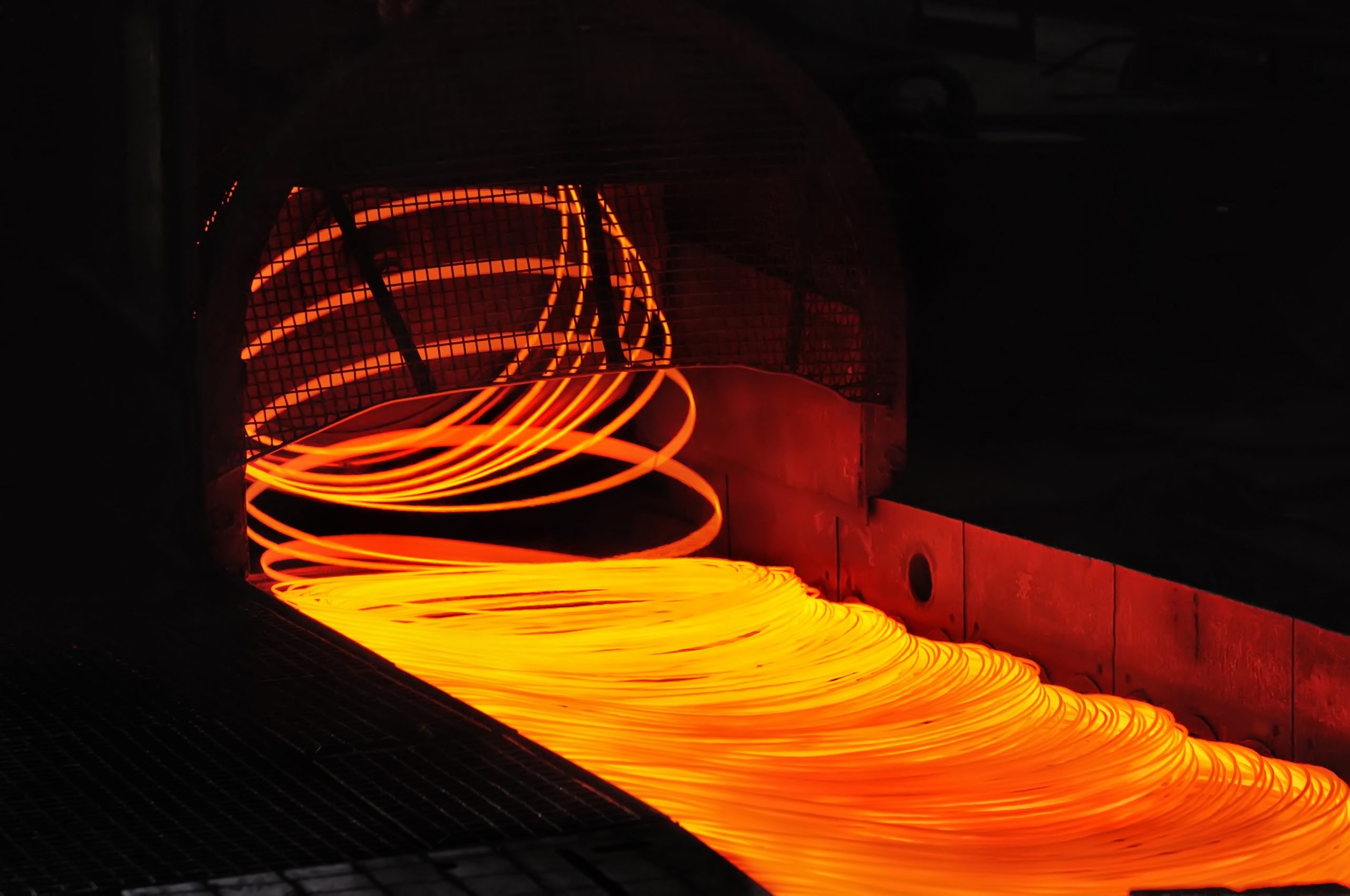
The idea of continuous manufacturing is to create large volumes of standardized products.
Take for example a steel manufacturing plant that produces 100 million tons of steel annually.
Liquid steel will be prepared for casting at one end of the factory, and at the other end, thin steel slabs will be rolled out and shipped off.
The steel will move along the plant, undergoing different treatments, on machinery that is rarely modified, to achieve an uninterrupted journey in the most cost-effective manner possible. Technically, all this will be happening at one time as the process is constant.
Here you can find a visual presentation of a steel manufacturing plant. But be warned, the quality and the content of the video will be like one of the videos you would have been forced to watch in school.
If you listen closely, you can hear the TV trolley wheels still squeaking.
So, let’s use another example of a more contemporary and fun, depending on if you can eat it, continuous manufacturing process: making peanut butter.
The peanuts will arrive at the peanut butter factory, already deshelled.
First (at point A), the nuts will travel along a conveyor belt to be roasted at 204 degrees. At the same time, the machinery will have a skipping function, to juggle the nuts and roast them evenly. This particular machine might roast up to over 3600kg of peanuts every hour. That’s a lot of nuts!
From there, the peanuts will move to the next process which will be a rapid cooldown as to not ruin the product.
Next, the outer skins are removed, along with the peanut’s hearts (yikes!). However, as is the aim of continuous production, the removed parts of the peanut will not go to waste. The skins will go into pig feed (point B, first product) and the hearts will be used as bird feed (point C, second product).
What remains of the peanut will be ground into a paste, along with the other, non-peanut, ingredients.
Once the paste is heated and goes through a second cool-down phase, it is then placed into jars.
Finally (at point D), but before it’s sent out for delivery, it goes through capping, and the application of an aluminum adhesive seal has been applied to air-tightly seal the peanut butter (the third and final product manufactured from the process).
You can watch a mesmerizing video on the peanut butter manufacturing process here.
This process is almost completely automated, leaving no wastage and the process is (as the name suggests) continuous to maximize the plant’s efficiency and profit.
Two types of continuous production
Continuous production is slightly different from continuous manufacturing, as continuous production includes operations like assembly lines that manufacture products with sub-assemblies, which is a manufacturing technique used in repetitive manufacturing and discrete manufacturing.
But, two types of continuous production can be utilized in continuous manufacturing. This is:
Mass production
Mass production is the manufacturing of large quantities of a standardized product. Process, materials, machines, and an uninterrupted flow of materials are the key characteristics of continuous manufacturing.
Process production
In-process production, the demand for the product is continuous and high. The materials can create different products at different stages of manufacturing. Like in an oil refinery, this can be kerosene, gasoline, etc. Or, like making peanut butter, can also make pig and bird feed.
This workflow production can be categorized as:
- Analytical Process of Production – When raw material is broken down into different products. Like how the peanuts were used to make three different products.
- Synthetic Process of Production – This involves mixing together two or more materials to manufacture a product. Like how sugar and oil are added to the peanut paste to make peanut butter.
Katana production scheduling software
Production planning doesn’t have to be complex. Stop spending hours updating spreadsheets or flipping through a manual with intuitive software that connects your inventory, purchasing, and production in one platform.
Continuous manufacturing advantages and disadvantages
Just like most processes, there are ups and downs to using this particular manufacturing process. However, first things first, the scale of your business or the demand for your product might not justify this type of method (especially if you’re a scaling manufacturer).
But nevertheless, here are the pros and cons:
Advantages
- Cheaper labor rates since production will rely mostly on machinery than any other resource
- High accuracy from using machinery
- Easy and simple to organize this type of process
- Minimize your wastage
- Easier to manage inventory
- A high return on investments
Disadvantages
- Can experience a huge amount of loss if demand falls completely or dips through different periods
- Continuous monitoring and maintenance of machinery and equipment
- No option for customers to customize their products
- Difficult to evolve to new situations and specifications. Shutdowns or reconfiguration can take time and be costly
Once again, a more hands-on crafter might not find much use for continuous manufacturing. Though, it doesn’t hurt to understand the competition and what is manufacturing in general. Why not research the different types of manufacturing processes to see what is best for you.
Whichever workflow you decide to use, Katana can help you with getting your business organized and working at its most efficient. Request a demo and see it for yourself.
Team Katana
Table of contents
Get inventory trends, news, and tips every month
Get visibility over your sales and stock
Wave goodbye to uncertainty with Katana Cloud Inventory — AI-powered for total inventory control