All you need to know about electrical discharge machining

Ioana Neamt

We’re about to blow your mind and tell you that everything you thought you knew about EDM is wrong. Sorry to break it to you, but EDM does not, in fact, stand for ‘electronic dance music.’ That’s right, you heard it here first: EDM actually stands for ‘electrical discharge machining,’ and it’s a real banger in the industrial manufacturing sector.
All jokes aside, electrical discharge machining, otherwise also known as EDM, has nothing to do with parties or dancing to electronic music. Although, some might see the process as a complex dance among different parts and materials. Let’s get right into it.
What is electrical discharge machining?
Electrical discharge machining, or EDM, is an elaborate manufacturing process that involves cutting or shaping hard materials using electrical discharges between electrodes that are submerged into dielectric fluid. It’s mainly used to shape materials that are difficult to machine using conventional methods, like titanium, Inconel, steel, graphite, or tungsten carbide, to name a few.
Since EDM does not require the use of mechanical force to remove or shape raw materials, it’s considered a non-traditional or non-conventional manufacturing method. It only works on materials that are electrically conductive, as it relies on electrical discharges to accomplish its task.
A short history of EDM
Electrical discharge machining sounds like a terribly complex process, so you might be wondering who on Earth came up with it and how? The origin story of EDM goes back all the way to 1770, when British physicist Joseph Priestley observed that electrical discharges had an erosive effect on hard materials.
Then, in the early 1940s, two Soviet scientists were trying to see if they could prevent erosion of tungsten electrical contacts that occurred due to sparking. Spoiler alert: they failed to figure it out, but they discovered something else in the process, namely that they could control the erosion and manipulate it, if they submerged the electrodes in dielectric fluid. Then they developed the first die-sink EDM machine that could work on materials like tungsten in a controlled and effective manner.
Of course, competitive as they are, Americans were doing their own research at the same time as the Lazarenkos. Harold Stark, Jack Beaver, and Victor Harding developed their own EDM machine that could work on aluminum castings. And there you have it, that’s how the first EDM machines were created!
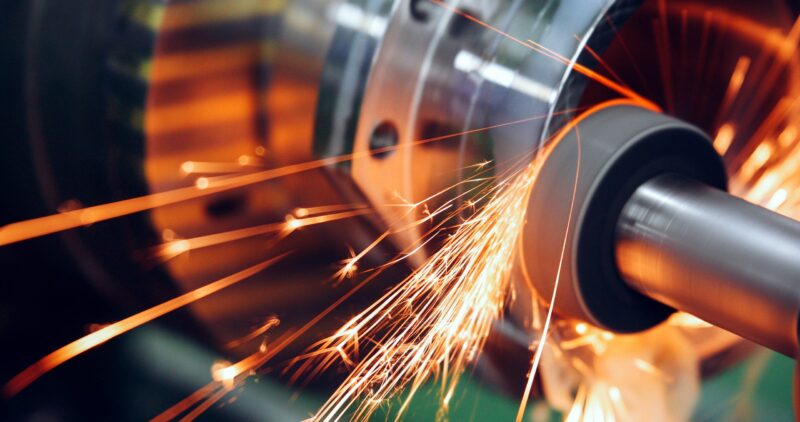
The electrical discharge machining process, explained
Now it’s time to go into a bit more detail about how electrical discharge machining actually works. But don’t worry, it’s not (quite) as complicated as it seems.
EDM is also known as spark machining, spark eroding, die sinking, wire burning, or wire erosion — and all these terms give you an idea of what the process of EDM might entail. The key components that are part of the EDM process include, but are not limited to, the following:
- Power supply
- Dielectric liquid
- Control unit
- Work tank
- Electrodes
- Flushing system
- Filtration and cooling systems
How EDM works, in a nutshell, is this — the process allows us to shape or cut a hard material by using precise and controlled electrical charges, or sparks. By applying rapid and recurrent sparks between two electrodes (the tool electrode and the workpiece electrode), we can remove material from the workpiece in a controlled fashion.
To eliminate erosion caused by the electrical discharge, the two electrodes are separated by dielectric liquid, which provides insulation and cooling. After each application or discharge, the existing liquid is flushed, along with the excess material that was removed. New dielectric fluid is conveyed into the work tank, and the cycle is repeated as many times as necessary. The EDM process is particularly useful in treating extremely hard materials like titanium alloys, carbides, or ceramics, which are resistant to conventional manufacturing machining methods.
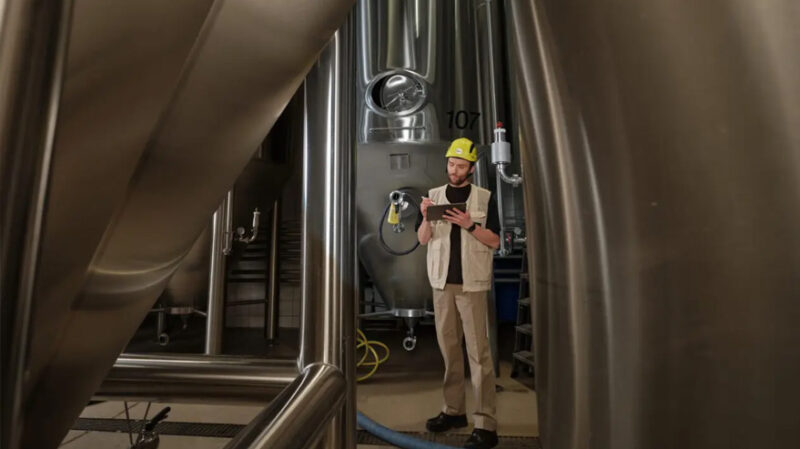
EDM methods and techniques
Now that we’ve got the basics of how electrical discharge machining works (hopefully), it’s time to learn about the most common methods and techniques used for this process. Depending on the type of material you’re working with, and the precision required, you might need a different EDM machine to get the job done.
Die-sink EDM
Die-sinking, otherwise known as cavity-type EDM or volume EDM, is a type of electrical discharge machining that involves submerging or ‘sinking’ the electrode and workpiece in an insulating liquid (usually hydrocarbon oil). In sinker EDM, the workpiece is usually made of graphite, tungsten, or copper, which are hard to shape or manipulate through conventional machining methods.
To create a specific shape from the material in sinker EDM, the tool used must be a positive copy of the cavity you want to create, to ‘fill in’ the hole you’re about to cut. For example, if you’re looking to create a square-shaped cavity in a workpiece, you’ll have to use a square-shaped tool to get the job done. In conventional machining methods, a precise cutting tool is used to cut the desired shape into the workpiece, moving side to side and back and forth. In sinker EDM, the tool has the same shape as the cavity we’re trying to achieve.
Wire EDM
Have you ever seen someone cut a big wheel of cheese using a wire? Well, that’s similar to how the wire EDM process goes, so you already get the picture. Unlike die-sink EDM, wire-cut EDM uses a very thin strand of wire to ‘cut’ the workpiece into a desired shape. We say ‘cut’ because in electrical discharge machining, there is no physical contact between the tool and the workpiece, regardless of the type of tool used.
Wire EDM can cut through incredibly hard materials, just like die-sink EDM. However, in wire-cut EDM, the wire can cut all the way through the piece, separating it completely, while in sinker EDM, a cavity is created within the workpiece. Just like cutting cute shapes into dough before baking, if you will. The wire in wire-cut EDM is usually made of brass, and the tool and workpiece are submerged in deionized water, another dielectric liquid.
Manage all your manufacturing processes in one place
Whether your manufacturing processes consist of electrical discharge machining or just old-school saw cutting, Katana lets you manage them all.
Multi-axis EDM
Multi-axis EDM takes electrical discharge machining to the next level. It’s mainly used to create intricate 3D shapes into hard materials, by incorporating additional axes of movement. This way, it manages to add more ‘creativity’ than the basic back-and-forth, side-to-side motions of die-sink EDM. This increasingly popular EDM model opens new doors when it comes to manufacturing and design using resistant materials, because it allows you to create incredibly complex shapes and angles that are impossible to create using conventional machining methods.
Fast hole drilling EDM
Fast hole drilling EDM does what the name says — it creates small and accurate holes, quickly. It differs from other EDM processes, in that it uses a rotating cube containing a pressurized jet of dielectric fluid to make deep, small holes in the workpiece. It’s incredibly fast and accurate, able to produce inch-deep holes in hard materials in less than a minute. Fast hole drilling EDM is very popular in the aerospace industry, as it’s commonly used to drill cooling holes into different aerodynamic components.
Electrical discharge machining use cases
EDM, while an unconventional machining method, is incredibly popular in certain industries that work with hard materials like aluminum, brass, copper, gold, silver, tungsten carbide, titanium, or steel. Some examples include:
- The aerospace industry — Machining turbine blades, engine parts, and other aero components
- The automotive industry — Working with molds and dies for car parts
- The healthcare industry — Creating intricate and details surgical tools, implants, and medical instruments
- The defense industry — Producing parts for military equipment, vehicles, or weapons
- The electronics industry — Handling and producing connectors and semiconductor parts
- The energy sector — Machining parts for wind, energy, or even nuclear energy systems
- The manufacturing industry — Creating complex machinery parts
- The research and development sector — Creating prototypes and experimental/test parts
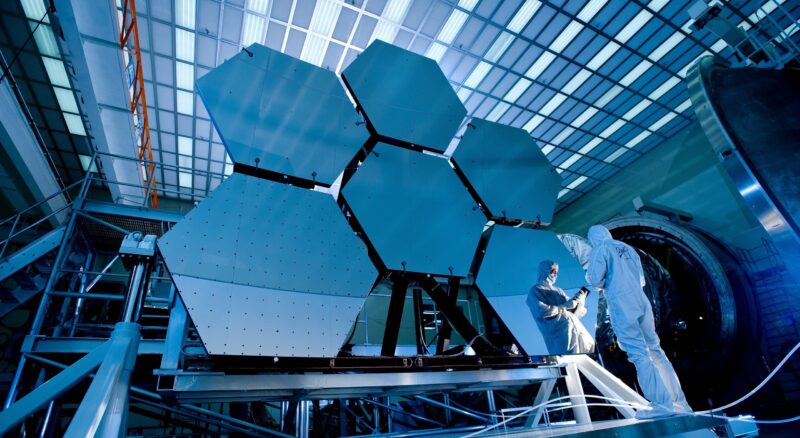
EDM pros and cons
With any complex and innovative manufacturing process, there are both advantages and disadvantages to consider, and EDM is no exception. While it’s an incredibly useful way of machining even the hardest-to-crack materials, it’s definitely not perfect, and it might not work for every scenario. Let’s check out some of the most common benefits and challenges related to EDM.
Advantages of EDM
- It can be used on tough materials like hardened steel, titanium alloys, or tungsten carbide
- It can machine complex, intricate shapes, shapes that cannot be achieved using conventional machining methods
- It minimizes mechanical wear since there is never any physical contact between the electrodes and the workpiece
- It is highly precise and accurate, making it ideal for machining small pieces in minute detail
- It achieves excellent surface finish and doesn’t create burrs, thus reducing the need for post-machining treatment processes
- It works with various electrically conductive materials and different types of dielectric liquids
Drawbacks of EDM
- It only works with electrically conductive materials
- It is slower than traditional machining methods, which results in a slower production rate
- It requires a significant financial investment, as the costs for the equipment, electricity consumption, maintenance, and repairs can add up
- It can involve recurrent investments and repairs (for instance, the electrodes in die-sink EDM can wear and tear over time)
- It is a complex machining system that requires specialized staff to install, operate, maintain, and repair it
Take your manufacturing processes to the next level with Katana
Electrical discharge machining is a complex, arduous, incredibly precise manufacturing process that can open new doors for companies in diverse industries, from healthcare, defense, and aerospace to electronics, research and development, automotive, and energy.
When it comes to manufacturing, Katana can be a powerful ally that enables you to make the best out of innovative, non-traditional processes like EDM. Integrating powerful inventory management software like Katana can help you optimize production processes, reduce lead times, and enhance efficiency while staying ahead of the competition through innovative technologies.
With the help of Katana, you can elevate your manufacturing game, streamline operations, oversee the entire production process, avoid errors and failures, and ensure customer satisfaction.
Ready to see Katana in action? Get in touch with us, and let’s see how we can help.
FAQs
Electrical discharge machining is the best way to work with hard materials that are challenging to cut or shape using conventional machining methods. Such materials include:
- Steel
- Aluminum
- Copper
- Brass
- Titanium
- Tungsten Carbide
- Inconel
- Hastelloy
- Graphite
- Silver
- Gold
- Kovar
Electrical discharge machining, or EDM, is different from CNC, which stands for computer numerical control. EDM uses electrical sparks to shape or cut tough materials, while CNC controls machinery used for precise milling, drilling, and cutting, via computer commands. Both methods are used in manufacturing, but their purpose is different.
The main types of EDM are:
- Die-sink EDM, which involves the submersion of an electrode and a workpiece into dielectric liquid
- Wire EDM, which involves cutting a workpiece using a thin brass wire
- Multi-axis EDM, which involves multiple wires or tools that can cut intricate 3D shapes
- And fast hole drilling EDM, which creates deep, small, and accurate holes into a workpiece

Ioana Neamt
Table of contents
Get inventory trends, news, and tips every month
Get visibility over your sales and stock
Wave goodbye to uncertainty with Katana Cloud Inventory — AI-powered for total inventory control