Part tracking software to take care of all your inventory needs
Implement Katana’s part tracking software into your manufacturing business to gain real-time visibility of every stock item and simplify your entire inventory management.
Full overview of your entire inventory
Not being able to deliver products to your customers in a timely fashion can quickly damage your reputation and hurt your bottom line. You need a live view of your inventory to avoid stock-outs and ensure every client gets the item they ordered. Katana updates your stock levels in real time, so you always know exactly what you have in stock and what’s running low.
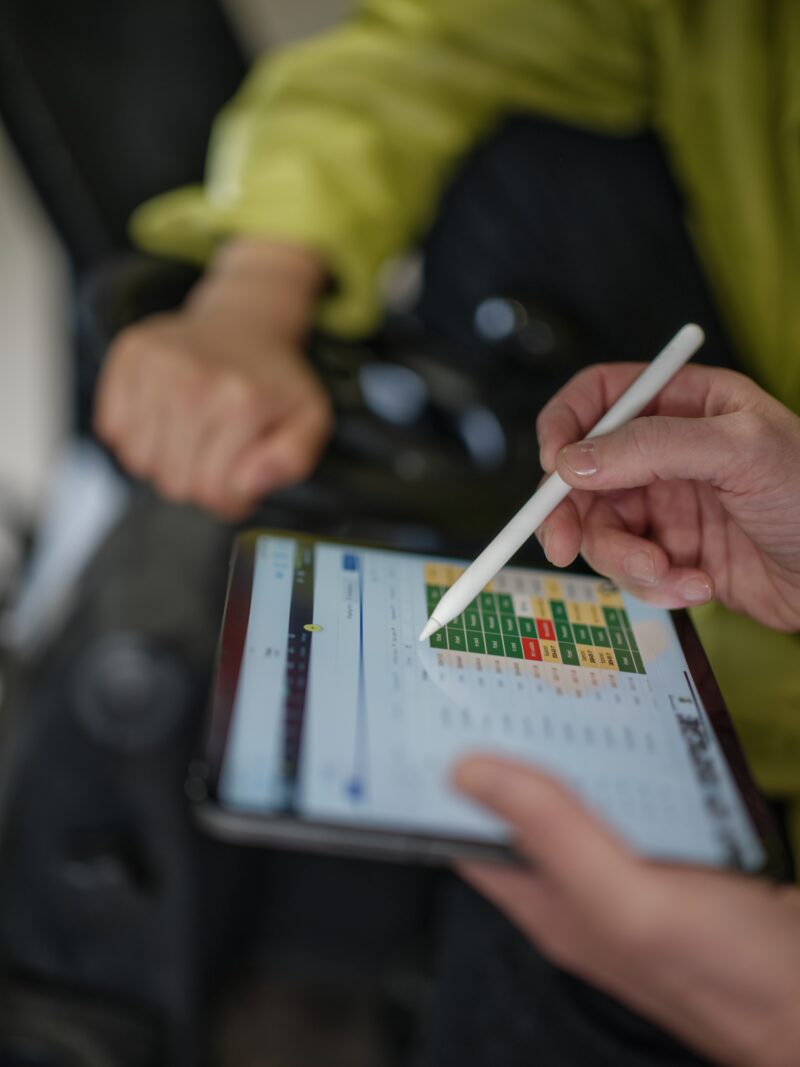
Streamline your inventory tracking with barcodes, QR codes, and RFIDs
Stocktakes are time-consuming but a crucial part of keeping your inventory levels accurate. To ensure your stock levels are correct, you need to count each item in your warehouse every now and again. This will help you avoid stock-outs and ensures you have the required items to fulfill orders.
With Katana’s part tracking software for manufacturing, you can benefit from perpetual inventory and reduce the frequency when manual stocktakes are needed. Katana allows you to automate your inventory counts with barcode, QR, and RFID scanning, making stocktaking a breeze.

Improve your inventory management with SKUs
Keeping track of every part you have in stock is essential, so you can make sure your inventory levels are optimal and your products are moving nicely. However, the more items you have, the more convoluted it becomes to track everything accurately.
That’s where stock-keeping units (SKUs) come in. Using SKUs allows you to collect invaluable data about your product movements. You can use this data for SKU rationalization, developing better marketing strategies, predicting seasonal demands, and more.
Katana’s part tracking software can then keep you updated about changes in inventory levels and highlight items that need to be replenished if these have reached your predetermined reorder points. This way you can ensure you always have the necessary parts to fulfill your customers’ orders.
Live view of your entire stock no matter where it’s stored
To remain competitive, businesses constantly need to find new ways to grow while also reducing costs. One way of achieving this is by expanding to new regions. Setting up manufacturing plants and warehouses in new regions can have many benefits, including:
- Reducing delivery times
- Reducing costs
- Managing risks
Katana lets you track your inventory across multiple warehouses making it easier to diversify your customer base by meeting demand globally. Katana keeps track of every item and updates your inventory in real time across all locations. Adopting Katana gives you back the reins over your inventory and ensures that you always know what you have in stock, no matter where it’s stored.
Want to see Katana in action?
Book a demo to get all your questions answered regarding Katana’s features, integrations, pricing, and more.
Part tracking software that integrates with your favorite tools for a smooth workflow
Native integrations, codeless templates, and fully customizable API integrations
Katana gives users access to the API, allowing you to create custom workflows and connect your business apps to manage your sales, manufacturing, and accounting on one platform. Automate data transfers between the services you use to level up efficiency. Take a look at Katana’s API documentation to learn more.
Katana provides us with all the features for manufacturing order management and can track inventory usage and incorporate our sales order tracking into Katana.”
Mikhail Moore
Chief Executive Office (CEO) at Vitacore Industries
Katana accurately keeps stock of assemblies and ingredients so that I can plan production and get instant feedback on whether we have enough resources in stock.”
Kelly Costello
Chief Executive Officer (CEO) at Puppy Cake
Having a system track inventory and what stage it is in has been incredibly helpful. It also has helped our team have a more clear delineation of the order of operations for each product in our catalog.”
Sarah Zinger
Director of Production Logistics at System76
We struggled to know which items are in stock so that we could build a batch and therefore often found extra components lying around […] Katana, we can now know what we have in store and where to look for it.”
Danielle Louw
Production Manager at CT LAB
Part tracking software FAQs
One common method to track inventory is to use a spreadsheet application like Microsoft Excel to maintain a running tally of how many units of each part are on hand. This can be done manually or automated using barcode scanners and other devices.
Another option is to use dedicated part tracking software for complete inventory control. This software can greatly improve your inventory accuracy, simplify data collection, and save time and money.
Katana’s parts inventory tracking software offers businesses all the necessary features for complete inventory control. Katana gives you a real-time view of your inventory counts for quick and easy warehouse management via web application. Katana comes with handy features like:
- Barcode scanning
- Intuitive bill of materials
- Batch tracking
- Tracking of an expiration date
- Support for multiple currencies
Periodic inventory is a method of keeping track of inventory levels where physical counts are only conducted on a periodic basis, such as once per month. This can make it more difficult to track real-time changes in inventory levels but can be less labor-intensive than perpetual inventory methods.
On the other hand, perpetual inventory is a method of keeping track of inventory levels where physical counts are conducted regularly, such as every time a part is used or removed from stock. This provides more accurate information about current inventory levels but can be more labor-intensive than periodic methods.
There’s also cycle count, which is a hybrid of the two methods. Cycle counting involves physical inventory counts being conducted on a regular basis but not for every single item in stock. This allows for more frequent inventory checks without the same level of commitment as perpetual inventory methods.
If your business has more than a handful of orders per day, using an ERP system is the best option for asset tracking. This type of inventory system can help you track real-time changes in inventory levels, reduce inventory costs, see when materials are running low, and generate reports on inventory usage.
An on-premise ERP is installed and operated from a company’s own servers and computers. A cloud-based ERP is hosted by the software vendor and accessed by navigating to the provider’s website. You can then view and manage everything via web application.
On-premise ERP systems can be more expensive to set up and maintain than cloud-based ERPs, but they offer more control over data security and privacy. With an on-premise system, you would need an in-house maintenance team to keep your systems running.
Cloud-based systems are typically more scalable and easier to set up and use and have more flexible pricing plans than on-premise ERPs. Also, the amount of time needed to set everything up and get familiar with the software is a lot less compared to on-premise systems. What’s more, with a cloud-based system, all the batches and updates are taken care of by the service provider, which can help to reduce downtime.
Get visibility over your sales and stock
Wave goodbye to uncertainty with Katana Cloud Inventory — AI-powered for total inventory control