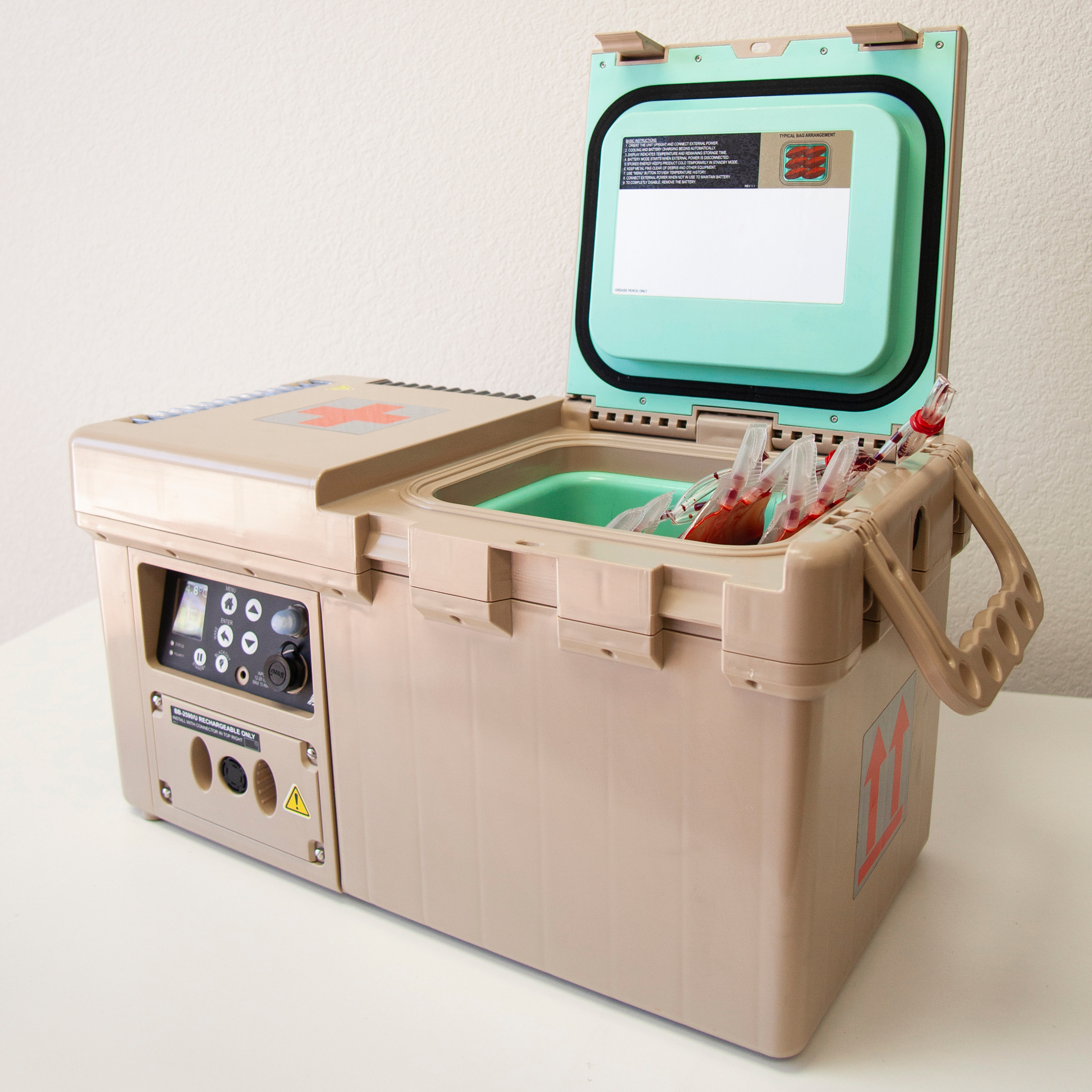
How Delta Development Team stays in stock with Katana
Delta Development Team Inc. manufactures portable refrigerators for the transportation of blood. They switched from using only QuickBooks Desktop to a setup of Katana integrated with QuickBooks Online, giving them live inventory tracking and planning and a structured and unbroken manufacturing process.
Shop Floor App
For optimizing operations
Multilocation
For strict quality control
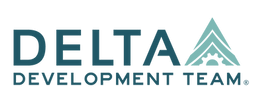
About Delta Development Team
Based in Tucson, Arizona, Delta Development Team is an American company that produces medical refrigeration units for the portable transportation of blood.
Chatting with Alexander Blanchard, the Operations Coordinator at Delta Development Team, we learned that the company started out by making large refrigerators called Tricons, which are large shipping units used by the military. They then went on to develop the APRU (Autonomous Portable Refrigeration Unit), the world’s most portable, FDA-listed blood and vaccine refrigerator. The APRU has since become their main product.
Alexander implemented Katana in Delta Development Team’s fulfillment process and is in charge of purchasing and inventory management for all of their materials. We spoke with him further about the company’s overall experience with cloud inventory software.
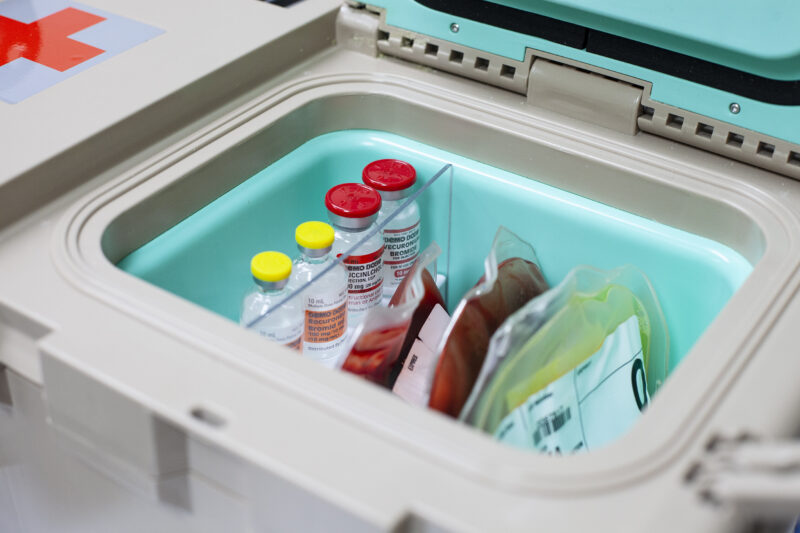
Planning future demand without the right data didn’t work
Originally, inventory tracking was done with pen, paper, and memory. Unfortunately, memory-based tracking lacks precision and can lead to inaccurate inventory levels and estimations of future material needs, leaving room for oversights, stockouts, and inefficiencies in planning and procurement.
Implementing Katana for live inventory tracking and planning addresses this problem by providing a centralized and accurate system to monitor stock levels in real time. Katana’s integration with QuickBooks Online ensures that inventory data is up-to-date and accessible, reducing reliance on manual methods and improving overall inventory management accuracy.
To keep track of materials, our COO had a pen, pencil, and his memory — ‘OK, I’m pretty sure we have all of these, so we’ll need more in a month’ – and that’s simply not a good system.
Alexander Blanchard, Operations Coordinator at Delta Development Team
Using Katana’s manufacturing capabilities, Delta Development Team established structured production workflows and schedules based on real-time inventory data and demand forecasts. This helps optimize production processes, reduce waste, and ensure manufacturing aligns with actual demand and inventory levels.
Finding a suitable solution
By using Katana, Delta Development Team can efficiently monitor inventory levels, receive notifications for reordering materials, and forecast potential shortages. This proactive approach helps in maintaining optimal stock levels and streamlining procurement processes.
Katana facilitates detailed production planning, giving Delta Development Team visibility into the entire production process, enabling them to easily adjust schedules, manage resource allocation, and prioritize tasks based on real-time insights. The ability to adapt to vendor delays or unexpected issues ensures continuity in production without major disruptions.
I love getting a little notification that says these materials are reordered. I can see what material is going to run out in a month.
The multilocation features allow Delta Development Team to efficiently manage inventory across different locations. This is particularly useful for segregating nonconforming materials (NCM) and maintaining quality control. And, with serial number tracking capabilities, they can assign and track serial numbers more flexibly across manufacturing and sales orders. This enhances traceability and facilitates compliance with regulatory requirements.
Optimizing stock levels with the right tech made easy
Katana helped significantly improve inventory management processes, such as anticipating material shortages a month in advance, enhancing proactive decision-making, ensuring optimal stock levels, and minimizing disruptions in production.
The Shop Floor App allows for task assignment and focused workflow management. This feature empowers production operators to focus on specific manufacturing orders or tasks, improving efficiency and reducing errors, resulting in increased productivity and better utilization of resources.
Overall, my experience with Katana has been really, really great. It’s easy to do stock adjustments, stock transfers, and stocktakes. I can easily see all the materials that we’re going to run out of in a month.
By adopting Katana, the Delta Development Team enhanced inventory management efficiency and improved job performance with the ability to perform tasks more easily and anticipate material needs in advance.
More case studies
Get visibility over your sales and stock
Wave goodbye to uncertainty with Katana Cloud Inventory — AI-powered for total inventory control