Manufacturing lead time: what it is and how to reduce it
Lead time is the time taken from scheduling to delivering a product. Reducing lead time is vital for your business efficiency. Find out how to reduce lead time.
Team Katana
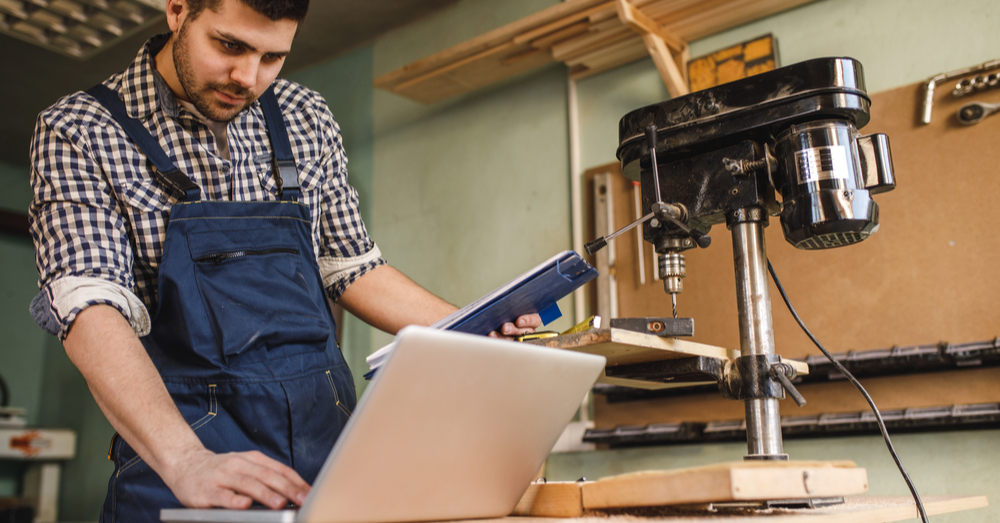
You find something you really like the look of, and you place an order.
Then you wait, and wait, and wait…
No one likes to wait for something they really want. Even on a small scale, if you queue for 20 minutes for a cappuccino and then wait another 10 minutes for it to get to you, it’s not going to feel worth it by the time you finally get it.
In this article, we’re going to look into manufacturing lead time, how you can reduce your lead times, and the tools needed to implement changes to production and scheduling efficiently.
Take the shortcut to lower lead times by implementing production scheduling software.
Request a demo to see how it works.
What is lead time?
Lead time is a metric that looks at the time taken from scheduling production to completing production for a product.
In other words, the lead time is the period when a manufacturing order comes in until the time it’s completed.
For example, let’s imagine you make wooden model bicycles and the process of building them takes place in three steps:
- You make the wheel
- You make the frame
- You put them together
Each of these steps of course has its own processing time, but what about that time in between?
Even if you’re managing to do all these processes at once, there is still time taken to transfer the items and this is all taken into account for manufacturing lead time.
In fact, this metric goes one further too. Because it also considers any time spent making purchases and waiting for materials.
So, before we delve further into lead times, let’s quickly explore another term people often confuse lead time with – cycle time.
Lead time vs cycle time
These are terms that can have varying definitions. But, when looking at lead time vs cycle time, then it primarily comes down to when the clock starts ticking.
- Lead Time starts from when the order comes in
- Cycle Time starts from the moment actual work starts.
So essentially, your cycle time also referred to as the order fulfillment cycle, doesn’t consider the purchasing process.
Although there is value to that metric as well, the focus should always be on manufacturing lead time.
At the end of the day, this is what the customer perceives. They feel the whole wait, it doesn’t matter to them why they’re waiting.
They don’t care how efficient your process is. They just want their delivery to be fast, so they can stick their magnificent model bicycle on the mantelpiece for the whole world to witness.
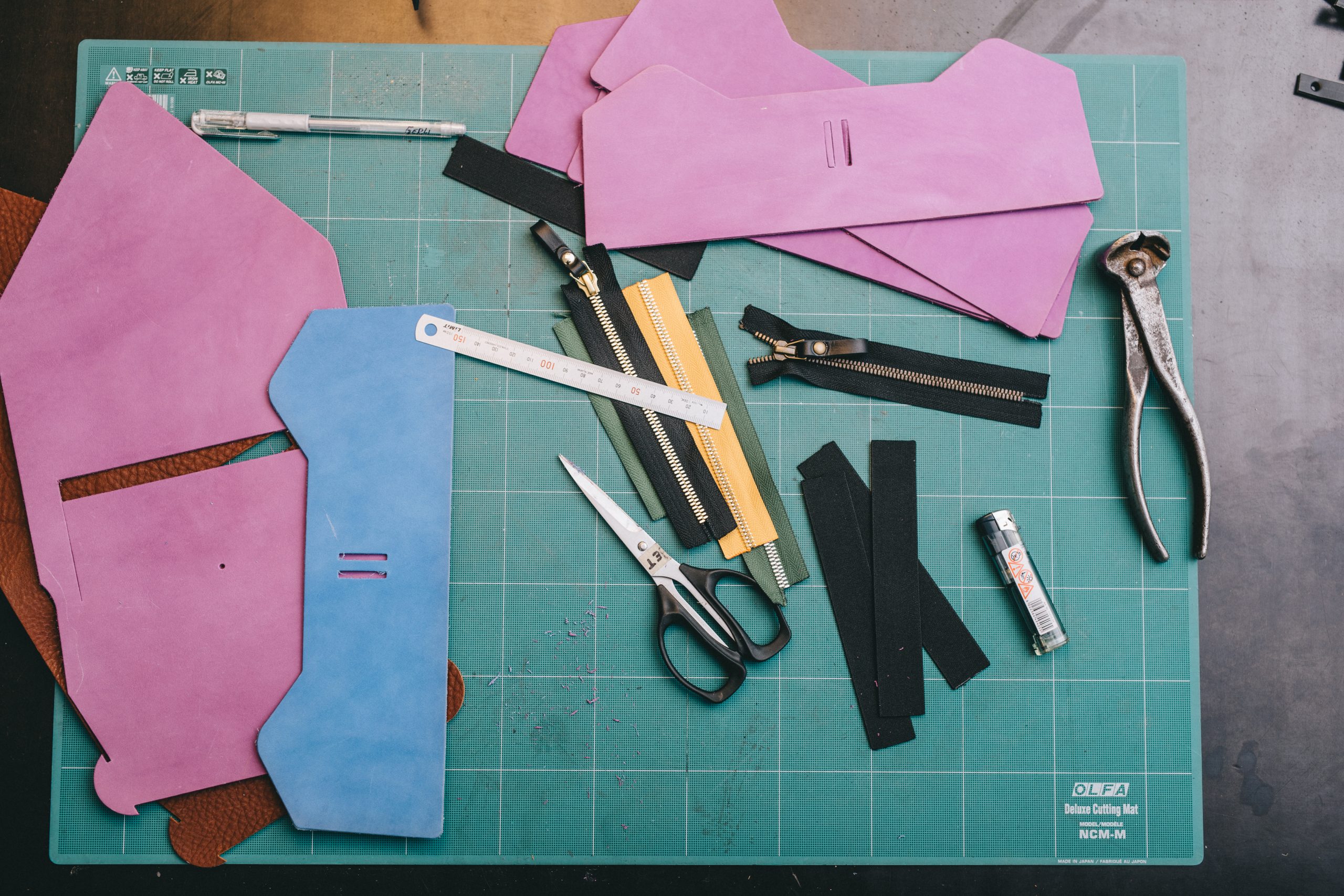
How to calculate manufacturing lead time
It could be hours, days, or even weeks. It all depends on your own processes.
But, essentially when figuring out how to calculate your manufacturing lead time (MLT), this is the formula you’ll be using:
MLT = Planning and Purchase Orders Made + Wait/dely times + Materials received + Operations + Manufacturing completion
This lays the foundation you need to start increasing your efficiency and begin to reduce that lead time.
But really understanding the concept is key to taking advantage of it.
There are two steps to consider:
- Preprocessing Lead Time; and
- Processing Lead Time.
Preprocessing is the planning stage. This is when your purchase orders go out and no work has been done yet.
Processing lead time, often referred to as throughput time, is the heavy-duty stuff. It’s the time required to manufacture or get hold of a required item. So, it’s the average amount of time for:
- Materials to come in;
- Processes to get done; and
- The waiting times in between.
Let’s get back to those exciting wooden model bicycles.
The preprocessing stage is spent on determining what materials are required, sending out the purchase orders, scheduling the tasks, and any other processes that need planning.
The processing then goes into the actual making of the bike.
Using the above formula, you can investigate these processes, determine how long it takes for each step to finish, and calculate your manufacturing lead time from there.
PRO TIP: “Someone’s sitting in the shade today because someone planted a tree a long time ago.” Warren Buffett.
Be a step ahead of your competitors. Plant the seed of knowledge and understand what is manufacturing. Learning now means you can reap the benefits later.
Reducing manufacturing lead times is vital for your business
Lead times are probably the biggest contributing factor that influences the performance of your supply chain.
Understanding lead time is important for every type of business.
An example of what happens if you don’t understand lead time
Let’s say you’re a retailer who orders a product that has a lead time of one month.
Two weeks after placing the order, your research shows that interest in the product has vanished.
Now when that product finally arrives in two weeks, it runs the risk of becoming dead stock.
And that’s just a simple process of ordering something, for manufacturers they have to consider:
- Material lead time;
- Production lead times; and
- Cumulative lead times.
If there’s one hiccup with any of these lead times, your overall manufacturing lead time is affected, which means customers’ orders will be delayed causing them to become unhappy and drive away sales.
Reducing your manufacturing lead times by as much as you possibly can will help you avoid creating bottlenecks as you wait for deliveries or resolve customer wait times as quick as possible.
But, how exactly do you go about reducing your manufacturing lead time?
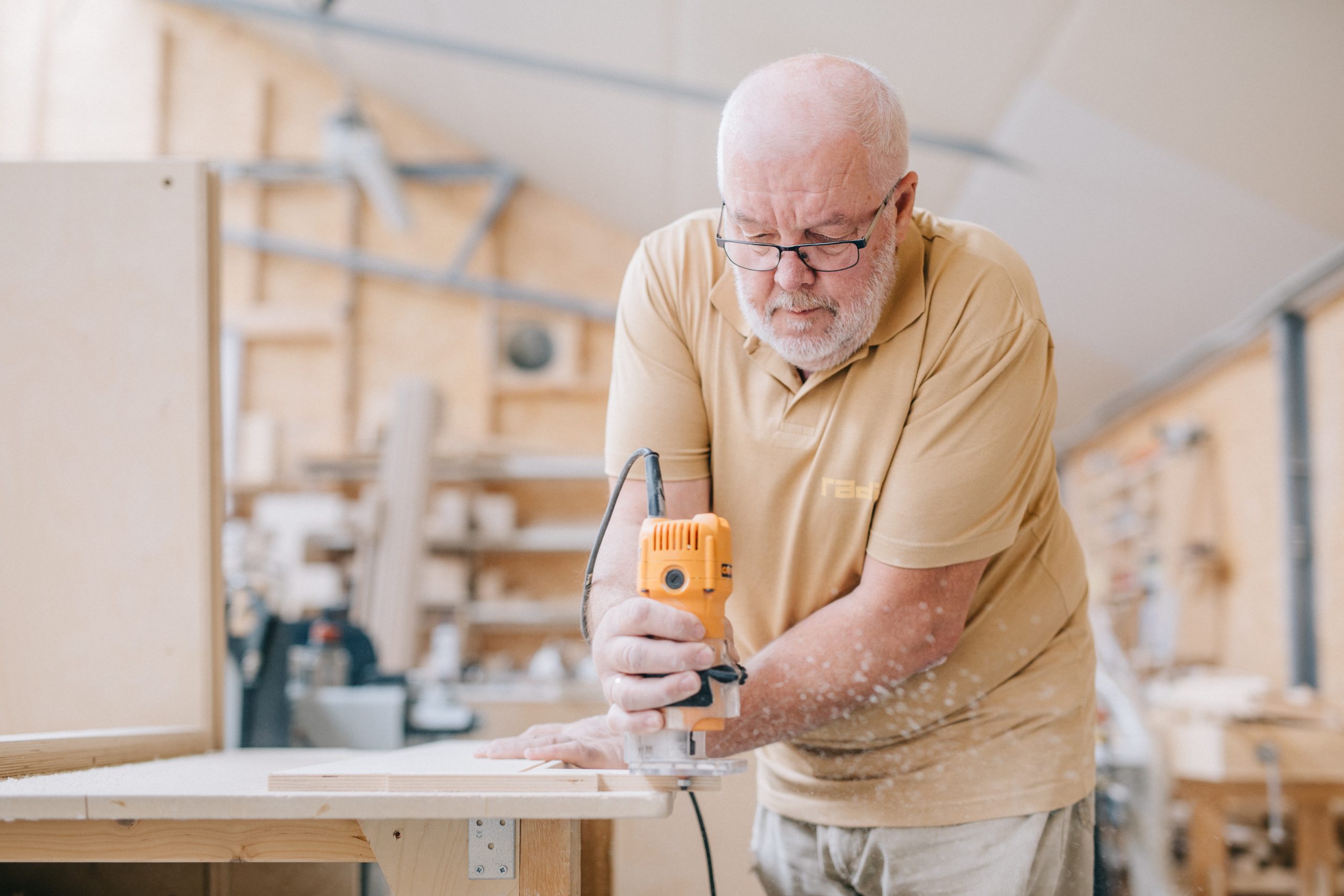
How to reduce manufacturing lead time
So, you now know how to calculate your lead time, but now comes the hard part, implement processes to reduce your lead time.
Well, this is where you can begin to dissect things and work out how to reduce lead time in your master production schedule because remember, the lower your manufacturing lead time, the less your customers have to wait for their orders.
The first is to make sure you are taking your inventory management seriously enough. But how does this help?
For one, it decreases your preprocessing time by making your purchasing a more efficient process. You don’t have to spend as much time planning your purchases because you already know if anything is missing.
The other effect it has is to make sure that you always have the right set of materials in stock. This means no waiting around with your hands in pockets for a delivery of raw materials before anything gets done.
Here are three quick tips that can get you started on the journey of reducing manufacturing lead time.
Shorten lead time and optimize inventory management
Set reorder points and safety stock
Getting into the habit of setting reorder points and keeping safety stock is going to be a lifesaver later down the line and help you implement lean inventory. A reorder point is a technique of identifying what is the optimal level of inventory to keep stocked until you order or manufacture more items.
Safety stock, on the other hand, is usually associated with make to stock businesses, but it doesn’t hurt to practice this, even if you use just-in-time inventory. Your safety stock is a buffer, so you can still fulfill orders while waiting on deliveries or production to finish.
Complete tasks in parallel
It’s easy to become laser-focused on a product’s workflow.
From point A, it moves to point B, point C, and so on. But it might be that one of the stages of production can be started and finished in tandem with other processes?
By figuring out what tasks can be completed at the same time you’ll be saving 100’s of hours in the long run.
Automate inventory management
Tracking supplier lead times and your own manufacturing lead times manually is an inevitable disaster waiting to happen.
According to studies, in every 300 characters, there’s at least one mistake. This might seem a non-issue to you, but over time these errors quickly add up and increase your lead times and bleed capital from your business.
Automating your inventory management will allow you to monitor inventory movements in real-time, and identify the inventory turnover ratio of your products.
But, be sure that you’re reducing lead time, and not cutting corners…
There is a difference.
Maintain product quality when eeducing manufacturing lead time
When decreasing lead time these two factors should always be in the balance:
- Product quality
- Customer satisfaction.
You can spend all the time in the world scheduling to absolute perfection and managing your inventory valuation methods. There are always factors that are out of your control because we all know that manufacturing rarely goes exactly to plan.
Margins of error need to be accounted for, and more than that you have to stay in touch with the floor level operations.
Often it occurs that workstations decrease their lead times at the expense of product quality.
It may be that you can have two of your team members working simultaneously on tasks.
But did you consider that beforehand they were using each other’s free hands for quality assurance when working alternately, and now they can’t do that?
There are so many minute details that can be missed when reducing lead times, that often corners can be cut even without any malice intended.
The worst-case scenario here is that there are knock-on effects on your customer’s satisfaction.
It’s important that you make changes gradually to processes so that you can keep track of your product quality and customer satisfaction.
You always need to consider the balance struck between lead times and your final product.
There are dangers to fixating on one angle because you might end up with tunnel vision. And then your hard work sadly just goes to waste.
So, with changes to be made but the steps needing to be incremental, what is the best way of tracking your progress when reducing your manufacturing lead time?
Full visibility and lead time reduction with Katana
Now you might be thinking, well, this sounds like a lot to deal with. Trying to decipher this information from my spreadsheets is going to be hell.
And that’s true, it will be hell, especially in manufacturing where things can go awry at any moment.
Katana can keep track of your manufacturing workflow from top to bottom.
But, how exactly does it achieve this?
Live order management
Katana allows you to monitor, in real-time, your:
- Procurement orders;
- Sales orders; and
- Manufacturing orders.
Total order management from one visual and easy-to-read dashboard that will help you better evaluate your inventory levels and make the best business decision when reducing your lead time.
Katana also comes equipped with a reorder point feature, which will highlight stock that is starting to run low, so you can stay ahead of demand and order or manufacture more items.
Production planning
Using different techniques like forward and backward scheduling along with Katana allows you to determine the length of time it takes to complete tasks and the associated manufacturing costs, and from there, Katana will be able to calculate and estimate a delivery date for you and your customers.
Better still, the production schedule within Katana updates in real-time, so if an order comes in that should take priority, you can simply use our drag and drop feature to rearrange the schedule on the fly, and Katana will redistribute allocated inventory and recalculate production times.
Shop floor app
If you’re manufacturing products at a large scale, you can also take advantage of the shop floor app, which gives your employees the tools to monitor tasks and report on progress, which allows for better coordination between workers doing tasks in parallel to reduce lead time.
Using the Katana dashboard means you can redistribute resources, and operators will be able to see any updates changes to the schedule immediately, giving you the flexibility to quickly adapt your manufacturing processes.
There are many more benefits and features your business can experience by adopting a system like Katana.
But, we’re believers in seeing is believing. Come and see for yourself how Katana is the perfect tool to help you lower your manufacturing lead times.
We’re offering you a free demo, so you can see for yourself the benefits that can be reaped with the built-in tools.
And that’s it! Everything you need to know about manufacturing lead time and the steps you can take to reduce lead time across the board.
We’re sure this article is sure to help you, but if you have any questions about manufacturing lead time or Katana, please feel free to write us an email, and we’ll be more than happy to answer them.
And until next time, happy manufacturing.
Team Katana
Table of contents
Get inventory trends, news, and tips every month
Get visibility over your sales and stock
Wave goodbye to uncertainty with Katana Cloud Inventory — AI-powered for total inventory control