What is material management?
Learn all there is to know about material management and how it differs from operations or production management.

Ioana Neamt
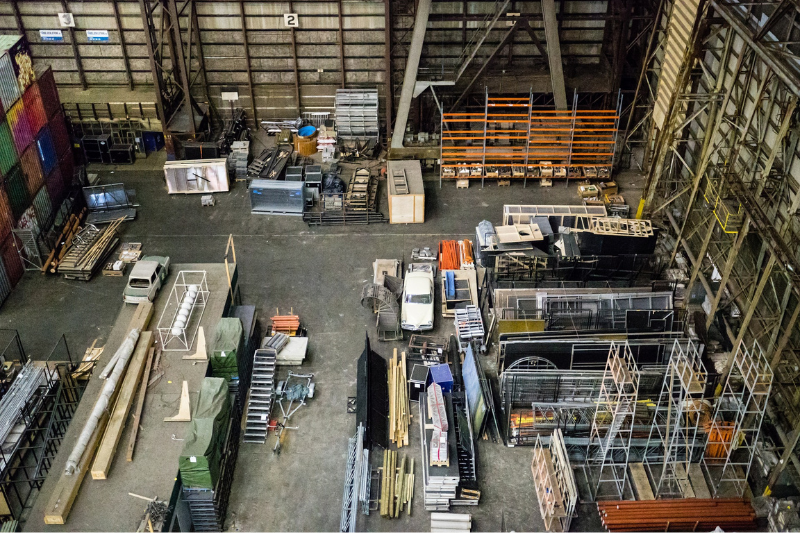
We’ve already tackled the subjects of production management, as well as operations management, so now it’s time to also take a look at material management, and what it’s all about.
Think of it as the third piece of the puzzle we’re trying to put together here for you, to give you a better picture of how these processes intertwine and how they keep your operations moving forward.
What is material management?
Material management in manufacturing refers to the planning, organizing, and control of the flow of materials and inventory throughout the production process. It encompasses a wide range of activities aimed at ensuring that the right materials are available at the right time, in the right quantity, and at the right cost.
Below are some of the key components of material management for the manufacturing industry.
- Procurement — Sourcing and purchasing raw materials and components needed for production
- Inventory management — Monitoring and controlling stock levels to minimize costs while ensuring that materials are available when needed
- Inventory storage — Managing the storage of materials to optimize space and maintain material quality
- Transportation — Coordinating the movement of materials between suppliers, storage locations, and production areas
- Production planning — Aligning material availability with production schedules to meet demand
- Quality control — Ensuring that materials meet required specifications and standards before they enter the production process
- Supplier management — Building and maintaining relationships with suppliers to ensure reliable delivery and quality of materials
What’s the difference between production management and material management?
Without even going into details, you can sense the answer to this question here. Production management, as the name suggests, focuses on the entire production process, while material management focuses on the materials and resources needed within that production process. Basically, there’s no production and no final product without the required materials.
- Production management focuses on the overall manufacturing process, including planning, scheduling, and controlling production activities to maximize efficiency, minimize costs, and ensure product quality. It encompasses aspects like workflow management, capacity planning, and quality control.
- Material management deals specifically with the procurement, handling, storage, and distribution of materials used in production. Its primary goal is to ensure that the right materials are available at the right time and at the right price, thus supporting the production process.
While both functions are interconnected, production management is broader in scope, while material management is a critical subset focused on materials.
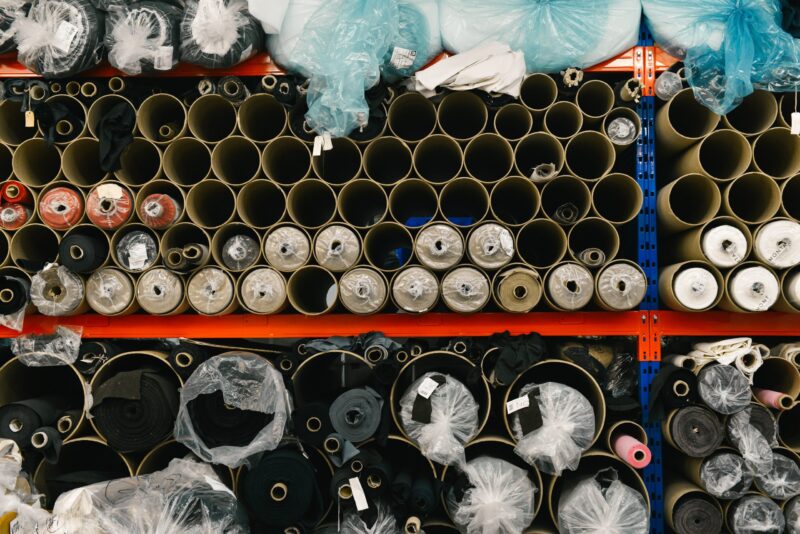
The different types of material management
While it might seem like a small piece of the production management puzzle, material management is a critical component of the supply chain. By failing to provide the necessary materials needed for the smooth flow of operations, the entire system can come to a halt, causing unwanted delays in your production process and leading to dissatisfied customers. Let’s take a look at the types of material management you should focus on, depending on the specific needs of your business.
- Inventory management — Involves overseeing a company’s stock of raw materials, semi-finished goods, and finished products. This includes identifying optimal inventory levels, determining reorder points, and ensuring proper storage. The goal is to balance the costs of holding excess inventory with the risks of stockouts.
- Warehouse management — Focuses on the storage, handling, and movement of goods within a warehouse, through activities such as receiving, storing, and shipping materials while managing inventory levels and their locations. The primary objective is to maximize space utilization and minimize storage and handling costs.
- Purchasing management — Entails sourcing raw materials, supplies, and services needed for production, which includes selecting suppliers, negotiating prices, preparing purchase orders, and managing supplier relationships. Its primary goal is to obtain high-quality materials at competitive prices while ensuring timely delivery.
- Transportation management — Focuses on the movement of materials between locations, keeping tabs on tasks such as selecting carriers, negotiating freight rates, preparing shipping documents, and managing delivery schedules. Its primary goal is to ensure timely delivery of materials while minimizing transportation costs.
- Material requirements planning (MRP) — A system designed for inventory management that helps plan production schedules and manage material procurement. It takes into account lead times, production durations, and current inventory levels to ensure that the right materials are available in the correct quantities at the appropriate times for production.
What are the key objectives of material management?
The key objectives of material management are as follows:
- Right materials — Ensuring the right materials with the right specifications required for the job are available
- Right time — Ensuring these materials are available at the right time, as needed, thus avoiding overstocking or stockouts
- Right amount — Ensuring the materials are available in the required amount for successful production
- Right prices — Ensuring the materials are purchased at the right price, by negotiating with suppliers and implementing cost-effective measures such as reducing lead times and waste reduction
- Right sources — Ensuring the materials come from reputable, reliable sources, by establishing long-term relationships with suppliers
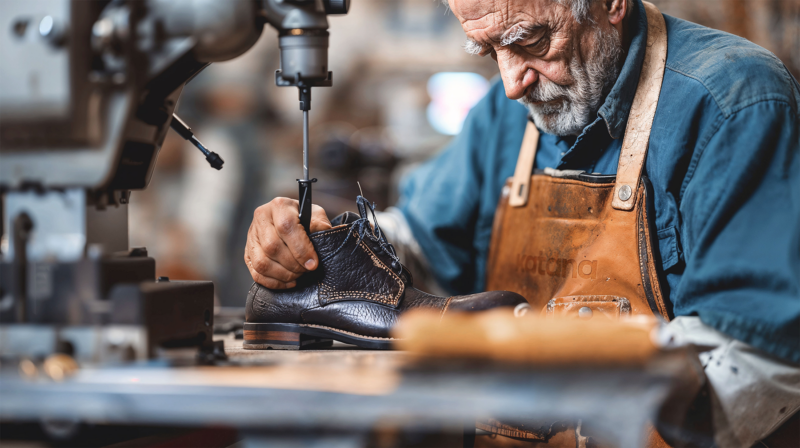
What’s the role of a materials manager?
You can take a wild guess at what the job of a materials manager implies, by looking at the list of objectives above. A material manager handles the procurement, storage, and delivery of the materials required for the production process, ensuring that everything goes smoothly from start to finish. Below are some of the tasks that are part of a materials manager’s day-to-day life.
- Facility management
- Sourcing and purchasing materials
- Inventory management
- Receiving and inspection
- Operations management
- Demand and risk management
- Cost management
- Production planning
We now know what production and material management involve, and the benefits of practicing them. However, it’s a lot of hard work, and perfecting your manufacturing operations can be argued as an impossible dream. That’s why it’s fundamental to find a tool that can help you get your production management under control.
Automate your production and material management with Katana
Although it is possible to do your production management in a cumbersome spreadsheet, it’s not ideal since there’s so much you need to do, and you can’t afford to spend any time stuck doing mundane administrative tasks.
This is where automation comes into play. Katana’s cloud inventory platform is built for manufacturers looking to get more control over their production management and operations. Katana helps manufacturers by giving them the power of automation by:
- Scheduling production and calculating deadlines
- Planning and purchasing materials
- Tracking finished goods and raw materials in real time and allocating them to sale orders and manufacturing orders
- Calculating manufacturing costs
Katana’s intuitive and elegant platform allows manufacturers to see a breakdown of production status.
Once you’ve logged into Katana, the Make screen is where you’ll find the key elements that will help you with production management and give you an overview of your scheduled production, including the:
- Order number
- Customer name
- Quantity
- Production time
- Production deadline
- Material stock level status
- Production status using our red, amber, green (RAG) system
- Improved floor-level management
At the Make screen, under the Tasks, you can see in more detail your floor-level progress, with a list of your workstations or team members and the jobs they’re working on, the operation being performed, and the status of that job.
Request a demo today and see for yourself how Katana can optimize your production and material management.
And until next time, happy manufacturing.

Ioana Neamt
Table of contents
Get inventory trends, news, and tips every month
Get visibility over your sales and stock
Wave goodbye to uncertainty with Katana Cloud Inventory — AI-powered for total inventory control