What is inventory discrepancy, and how to manage it
Understand what can lead to inventory discrepancies and get top tips for improved inventory management and reduced losses.

Ioana Neamt

Finding a mismatch between recorded and physical stock levels is one of the most common challenges faced by businesses. Whether you have too much or too little of something, compared to what you planned for, can result in unhappy customers, operational disruption, and even financial loss.
An inventory discrepancy is a problem. Depending on how large the discrepancy is, the problem can be small or big. But, as with all problems, the first step in dealing with it is to acknowledge it exists. To that end, let’s get into how inventory discrepancies can be created, how to best identify them early, and what steps you can take to prevent them.
What is inventory discrepancy?
A simple way to think of a discrepancy is that it is a mismatch. Specifically, it represents a mismatch between the number of items you have on your books and the actual number of items you have in storage. You might have a shortage (less inventory than you thought you had) or a surplus (more inventory than you expected). Either way, it’s something you have to deal with.
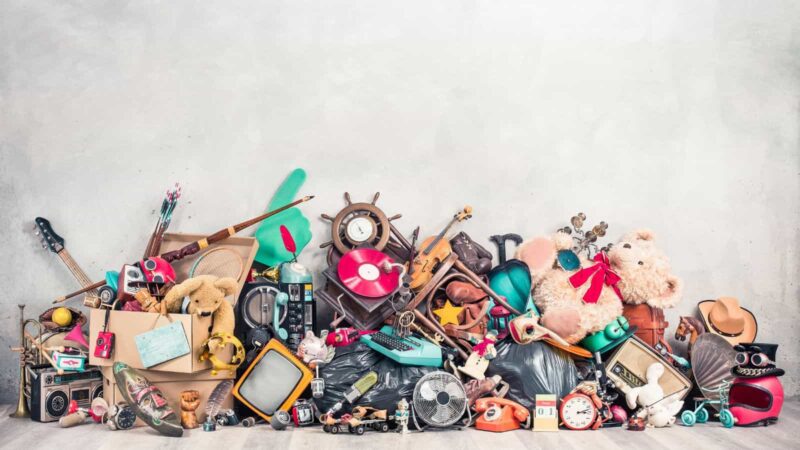
Causes of inventory discrepancies
Inventory discrepancies more often happen due to a combination of factors over time, rather than one event. Understanding possible causes can help you find ways to avoid them. The most common issues leading to inventory mismatches are:
- Human error — Discrepancies can start from someone making a mistake when counting stock or recording the data
- Theft — Shortages can be the consequence of unauthorized removal of items from your inventory
- Damage or spoilage — It can happen that products that are damaged or spoiled are not properly identified as such during a stock count
- Vendor errors — Mistakes can also happen on the supplier end, either in shipping or invoicing, that can lead to discrepancies in your books
- System glitches — You may experience technical issues with inventory management software, that can affect your record-keeping or data entry
- Poor inventory management practices — Having less-than-adequate procedures for receiving, storing, and issuing items can add up to discrepancies in your inventory
- Natural disasters — A one-time event like fires, floods, or earthquakes can cause significant loss of inventory
Accurate inventory levels, every time
Katana’s cloud inventory platform keeps track of all your stock in real time. Streamline your inventory management by eliminating inventory discrepancies with Katana.
6 key strategies to avoid inventory discrepancies
Once you understand where a discrepancy can originate, you can plan to get ahead of it so that you give yourself the best chances of avoiding these situations altogether. Let’s go over some of the key strategies that are recommended for best results.
Cycle counting
Instead of doing a full physical inventory count more often, conduct regular cycle counts of specific items. This method of stocktaking allows you to make more frequent checks and adjustments and can help you identify discrepancies very early on.
Implement an inventory management system
A good inventory management software can track inventory in real time, automate many tasks, reduce the risk of human error in data entry and updating, help you maintain a high level of accuracy, and even identify potential discrepancies through analytical features. Barcode and radio frequency identification (RFID) compatibility is a big plus in saving you time while ensuring accuracy.
Employee training
Make sure that all your employees are properly trained on all inventory procedures, including receiving, storing, and issuing items. It is also important that you prepare clear instructions that remain easily available for follow-up at all times, so your employee training is effective in minimizing errors and inconsistencies.
Regularly review and adjust processes
Regularly assess the effectiveness of your inventory management practices and make any adjustments that are needed. This can mean making changes to storage locations, receiving procedures, warehouse layout, or even the frequency of cycle counts.
Use stock tracking technology
Employing barcode scanning or RFID technology to track items makes a big difference in terms of accuracy and efficiency. It cuts down on data entry time while maintaining high fidelity of data and contributes greatly to real-time visibility into your inventory.
Vendor verification
Make a habit of checking the accuracy of vendor invoices and shipping documents, so that you catch any errors as soon as possible and prevent them from affecting your inventory records down the line. Maintain good communication with your supply chain partners, for timely resolution of any issues you identify.
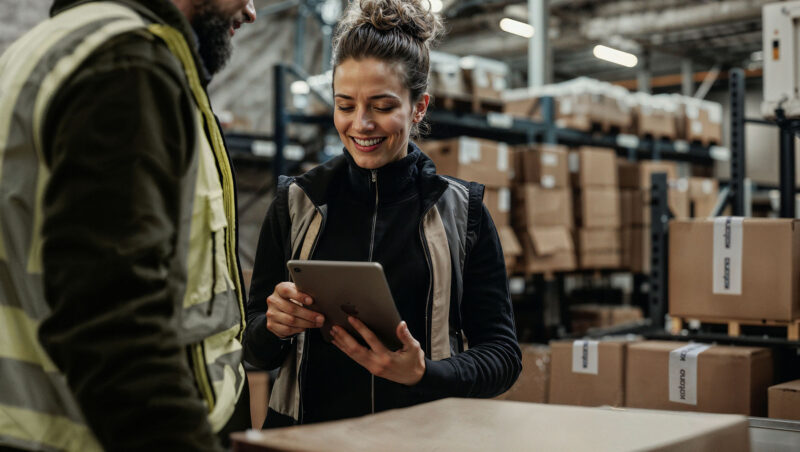
Best practices to mitigate inventory discrepancy
Working to reduce the incidence of inventory discrepancies essentially means you are working to improve the overall efficiency of your inventory management. All systems are connected and lift each other to better quality results when your entire business operates at the standard you establish. And that is, essentially, what best practices are all about. Let’s go over some of the most recommended ways to mitigate inventory discrepancies.
Sustain a culture of quality control and accountability
Best practices include offering proper training to your staff on all internal procedures and then inspiring and empowering them to take ownership of quality standards in everything they do.
The best way to have a clean house is to keep it clean with small, consistent, and frequent actions. Attention to detail during any phase of handling inventory will go a long way to avoiding discrepancies. Any mistakes that do happen are valuable lessons for everyone up and down the chain. Communication and transparency are essential to both identifying and resolving discrepancies as soon as possible.
Identify causes of discrepancies and adapt your process
Mistakes do happen, and the most important thing is to learn from them and take measures to prevent repetition (leave the reps for the gym!). If a mismatch happens because a process was not followed correctly, take the time to enhance the training and development of your staff so that they can do better. If the cause was faulty technology, make sure you are always up-to-date with maintenance and warranties, to ensure you are working with the best quality tools.
Automate inventory tracking
The best way to keep errors at a minimum is to embrace inventory tracking technology. Implement barcode or RFID scanning to ensure that each item and batch in your inventory is well accounted for in real time, at any point of its journey. Invest in inventory management technology that uses this data to keep your stock count up to date through sales, returns, and any other transactions.
Partner with a specialized logistics services provider
While self-warehousing does give you full control over your operations, this means that you and your team are the ones coordinating all movements of your products, from picking and packaging to shipping and everything in between. One popular practice among businesses is to partner with a third-party logistics services provider (3PL), which specializes in inventory handling services and can handle at least some of your inventory moving and storing needs.
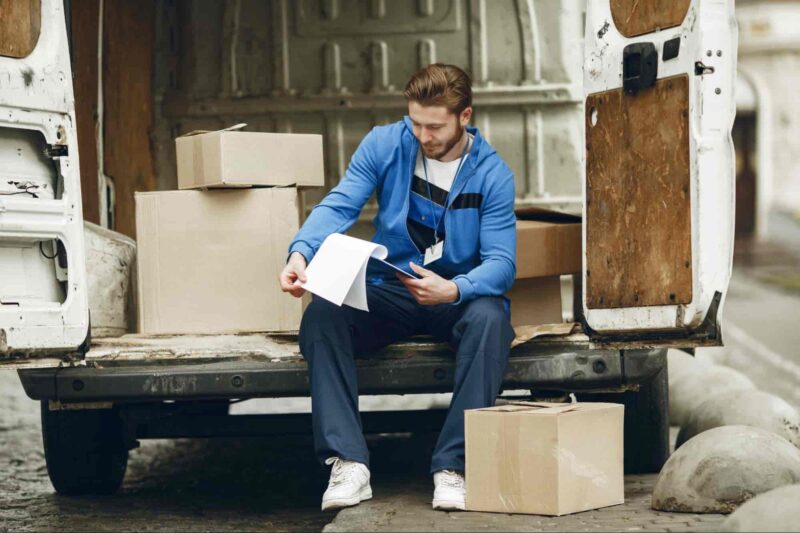
Prevent inventory discrepancies with Katana
The best thing you can do to achieve high-quality inventory data discrepancy management is to work with the inventory management technology that best suits your business. Katana cloud-based management software is widely appreciated by a variety of businesses, both big and small, for its intuitively designed suite of features. With Katana, you have:
- Real-time inventory updates
- Omnichannel inventory management
- End-to-end traceability with lot tracking
- Expiry date tracking for shelf-life management
- Integration with your favorite tools, apps, and platforms for easy data management
- And much more
Reach out for a demo to see Katana in action and how it can improve your inventory management process.
FAQs
Yes! Taking stock of any inconsistencies between your stock and your records is essential, and the best way to go about it is to work with an inventory management system, such as the cloud-based solutions offered by Katana, to help you automate tracking items and updating your database.
Work with a barcode or RFID system to more easily keep track of items, batches, sales, returns, faulty shipments, and everything in between. Automated traceability helps reduce or eliminate human error in inventory counting and recording.
Inventory reconciliation is the process by which you identify any discrepancies in your stock levels. This process compares the physical count of inventory items to the recorded quantity in your records and should be done regularly, to keep discrepancies at a minimum.

Ioana Neamt
Table of contents
Get inventory trends, news, and tips every month
Get visibility over your sales and stock
Wave goodbye to uncertainty with Katana Cloud Inventory — AI-powered for total inventory control