Manufacturing throughput time: Fast-forwarding production
Throughput time breaks down manufacturing processes into bitesize chunks. Make sense of it and produce faster without compromising the quality of your product.
Team Katana
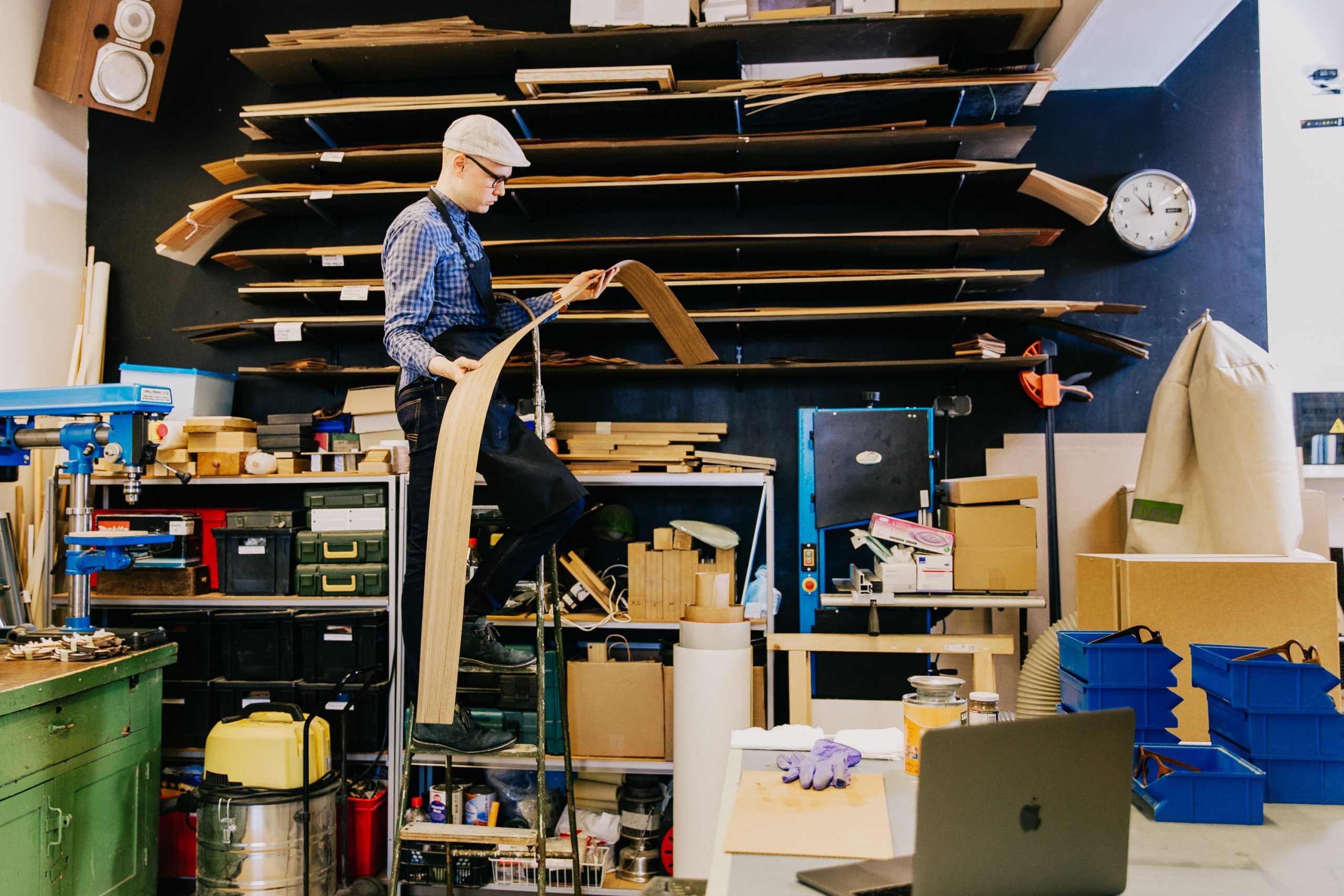
Makers like the team at “Framed” know how important it is to keep track of their manufacturing processes from all angles. There’s plenty of ways to do so – throughput time is one of the tried and tested.
“Time is of the essence”.
Or in other words, the faster things get done, the more time we have to spend on what we want.
And in most cases in life, that means finding out which areas you’re a little bit slow on so that you can give them a little push.
Manufacturing is no different.
We all know that making your own products is a time-consuming affair.
That’s why tracking how long it takes for each of your productions to be completed is a great way to improve your efficiency and order fulfillment cycle time.
There’s a metric in the maker’s world that can help here:
Throughput time
Throughput time is the amount of time it takes for you to get a product made, from the moment you start making it, to the moment it lands back in your inventory ready to get shipped out.
Here’s a quick calculation for a manufacturer who produces 100 items across 8 hours:
100 / 8 = 12.5
So, if you increase production to produce 20 more items, your throughput rate will be 15, a 20% increase in item output.
This calculation is essential for getting more control over your production and increasing your ROI.
Every business is going to be working on a different scale but getting to know this number intimately is a great way of plotting how you’re doing in your day-to-day operations.
Because once you have a rundown of where you’re moving like snail-like, you can start to channel your inner cheetah and speed up the workshop.
Set targets and aim high.
But before you do, let’s get to know a bit more about how this magic metric works…
Get started with the real-time master planner. Make accurate manufacturing and purchasing decisions with live data to ensure optimal inventory levels at all times. Request a demo today and take your business to the next level.
What is throughput time?
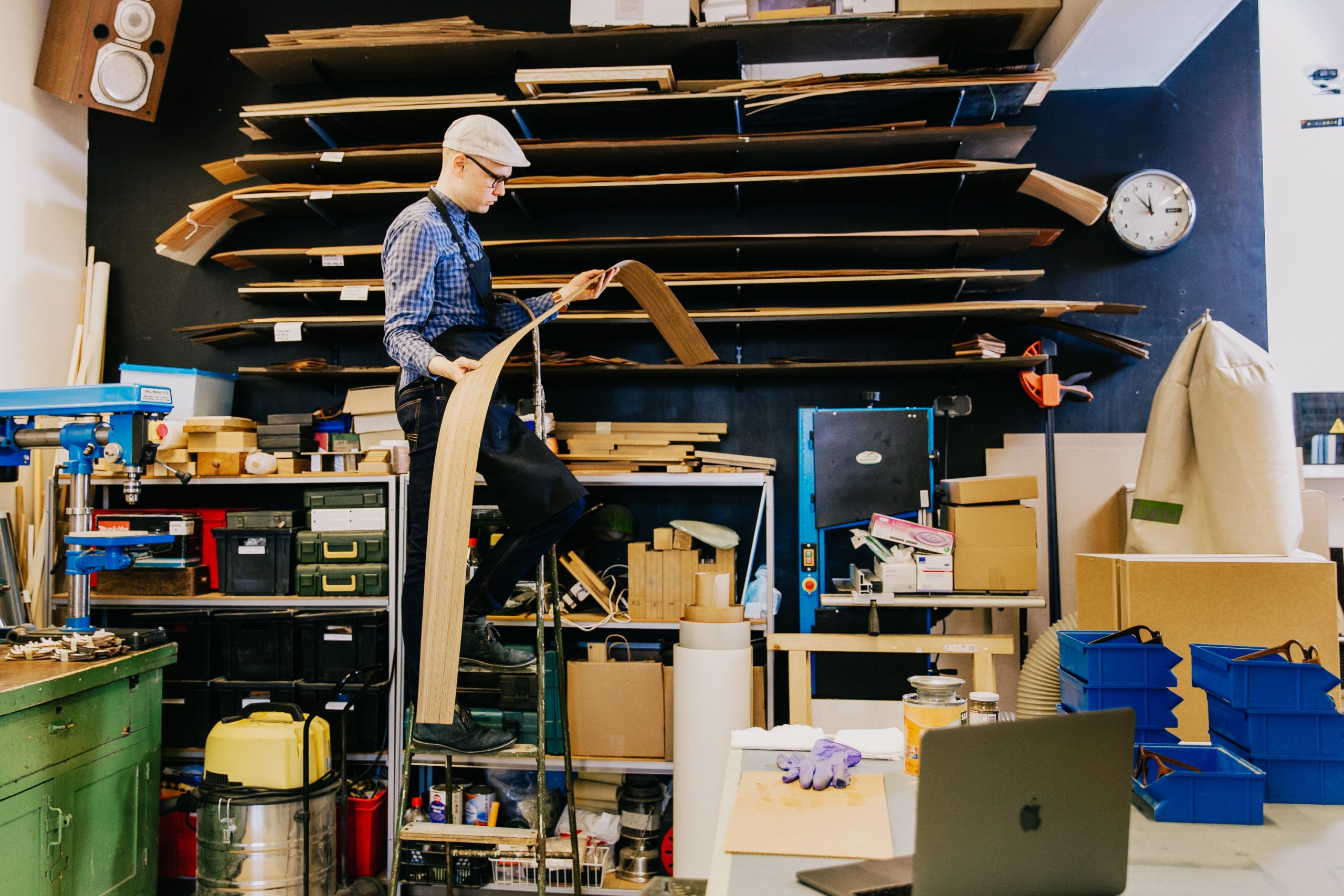
Throughput is the rate at which an item takes from manufacturing order coming in, to the completion of production.
For example, if we were a candle maker, we could look at one of our products manufacturing processes and calculate that we make 3 candles an hour.
But if you inverse that to find out how long it takes for just one candle then you get throughput time.
So here it would be:
60 mins / 3 candles = 20 mins per candle
Throughput definition is basically the amount of time it takes for one unit of a product to be made, from the start to the finish of manufacturing.
Cycle time vs throughput time
Before landing here you might have heard the terms cycle time and throughput time used interchangeably.
So, what is the difference between throughput time and cycle time?
Well here’s a surprise for you — they are the same thing!
It’s mainly a matter of preference which you decide to use, depending on the context it can be useful to use both.
The key point to remember is that this is the amount of time it takes for each of your products to be made from start to finish.
From the moment the manufacturing order comes in, to the moment the finished product is in your stock room ready for shipping.
This is why it works whether your products are make-to-order or make-to-stock.
Lead time vs throughput time
There’s another important metric known as manufacturing lead time which you can use to improve efficiency in the workshop.
It actually uses throughput time (or cycle time if you prefer) in its formula, so you can have two metrics for the price of one!
Lead time starts when the orders come in from the customer and end with the product on their doorstep, unlike throughput time which is only concerned with the process itself.
That means looking into the wait times before manufacturing and after it too, which are also important, though slightly broader in scope.
But of course, we’re getting a bit ahead of ourselves here.
So, let’s jump into the deep end and see how we can work throughput time out properly.
Throughput time formula

The basic formula for throughput time is:
Throughput time = Time taken to complete manufacturing / Unit of product
Which could be as simple as “72 minutes per pencil case”.
The time period that you choose depends on the product you are making. You want to settle on a unit that makes sense for you.
You could make “72 minutes per pencil case” into “4320 seconds per pencil case” but that wouldn’t be too easy on the eyes would it?
But to go further than this we need to determine what actually goes into throughput time. Because we’re not dealing with just a flick of the wand here.
The time taken to complete manufacturing can be broken down.
Throughput time consists of:
Processing – Time is taken for the actual processes of manufacturing, for example melting the wax for candles;
Inspection – Time spent for quality control and making sure that materials are in the right place;
Moving – Materials often have to move between workstations and stockrooms, so this is for those periods of time; and
Queuing – You’re going to have to wait for each of the above to get started, so here we calculate that extra downtime.
As you can see, there are some precise methods to getting this formula right, if you spend the time acquiring the data for all the above.
And even if you decide not to go ahead and use this metric in the long term, it’s always good to have an idea of where your manufacturing time is being spent most regardless.
Advanced throughput time calculation
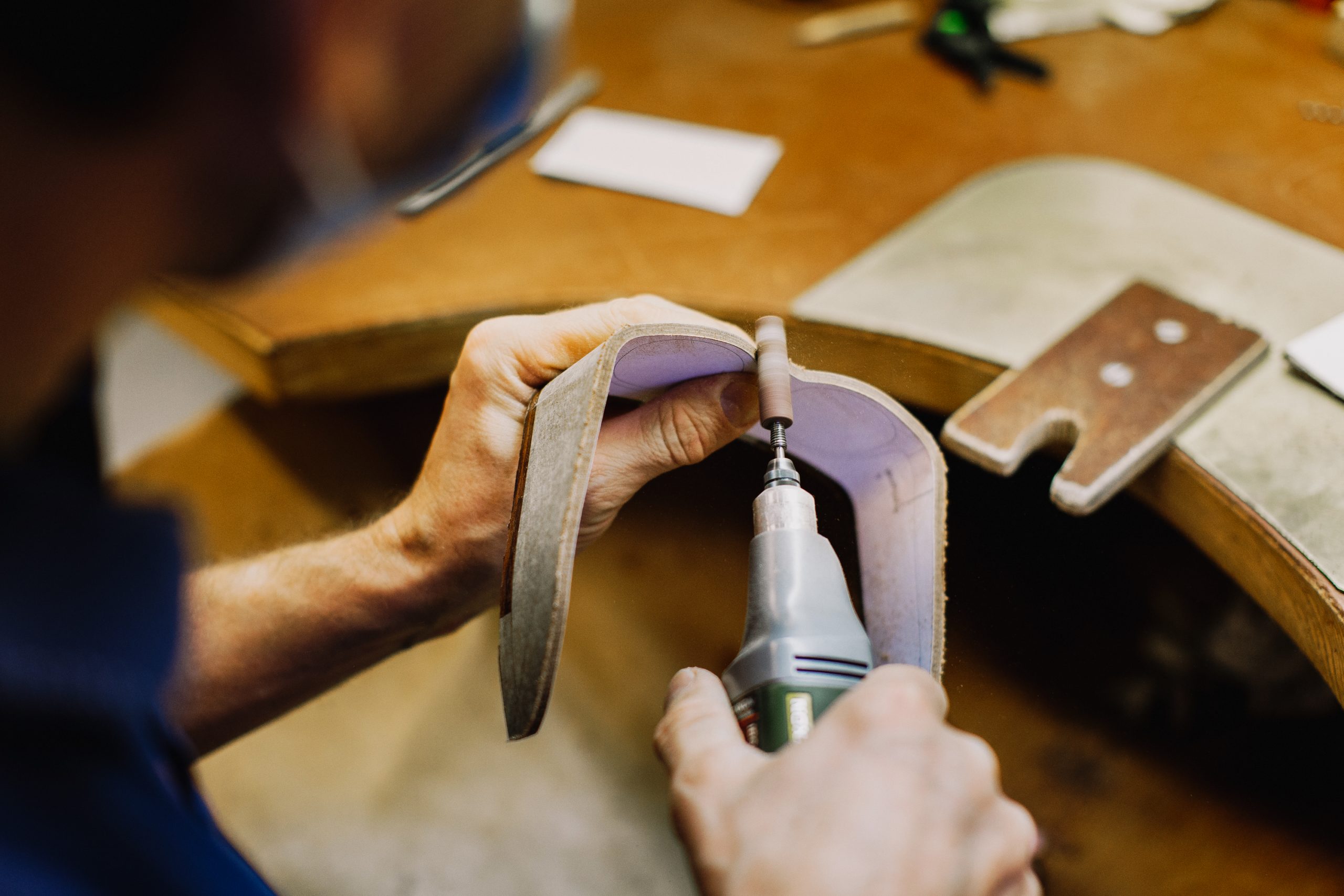
Okay, we know the basic formula, and we know what goes into it.
That might be enough for some, but for others, a more detailed breakdown can be more useful.
So, let’s put all the information together into a more digestible and precise formula.
Here’s how to calculate throughput time in detail:
Throughput time = (Processing + Inspection + Move + Queue) / Unit of product
Let’s take an example and break it down so that you can see how it works for yourself.
Imagine you are a brilliantly successful scented candle maker.
You got one candle out there that flies off the shelves.
It’s called the Scorpio candle because it’s shaped like a scorpion and has been known to smell especially good to those born under the Scorpio sign.
Sadly though, it often comes up short in stock because it takes so long to produce.
Seems like a good place to test out throughput time:
1. Let’s starts with seeing how long the processing takes.
In this world – wax melting, candle forming, and wicking are the main processes.
And the total time taken for the production processes is 360 minutes.
2. Next is inspection.
Thankfully, that is rather simple. Just got to check if the candles are all the right shape and packed correctly – that takes 5 minutes a candle.
3. Moving the candles around when they are raw materials is a little bit complex though.
They get done in batches but are being carried one by one, so the time taken here adds up to 60 mins a candle.
4. As for queueing, there is a fair amount of time taken for the wax to melt and wait for the staff to come back from lunch break. So, we got around 120 mins there on average.
Putting it all together this is what we get:
Throughput time = (360 + 5 + 60 + 120) / Candle or 545 minutes per Candle
Now that might seem like a lot of time, but you have to remember that you are going to be making more than one candle at a time.
This metric gives you an idea of how you could reduce the time taken for manufacturing on a micro-scale and see in detail where the improvements can be made.
That’s how you can begin to reduce throughput time and make your calculations count in the workshop.
Katana production scheduling software
Managing your inventory, production, and sales shouldn’t require an endless folder of spreadsheets or dozens of software solutions. Katana makes production scheduling efficient, accurate, and hassle-free by unifying all your manufacturing tools in one view.
How can I reduce my throughput time?
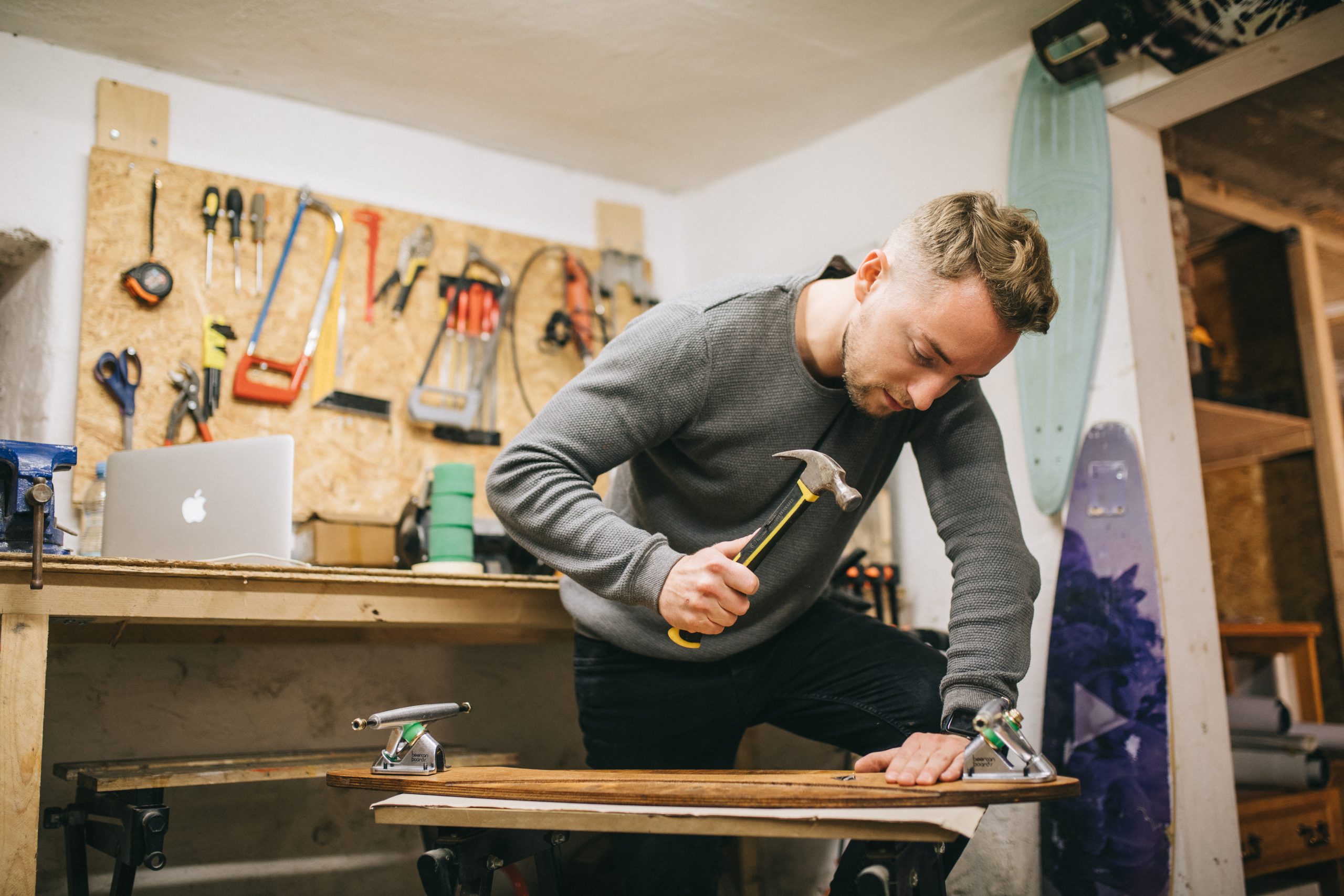
So, that’s a question, how do we actually reduce this magic number?
Well, the great thing is that if you’ve already done the breakdown, then you’ve done half the work.
Because you now have the four segments upon which you can start to analyze your manufacturing workflow.
Remember Processing, Inspection, Moving, and Queueing.
Let’s look at the example before so we can get an idea of where we could improve.
1. Processing
Looking at the first segment of processing is often the most technical.
Your processes are difficult things to change and in the case of candle making the ways to change would be to improve the machinery, the tools, and the skills of your workers.
Do some research into your product and see how competitors are doing it. Maybe there’s a more efficient way.
2. Inspection
It’s too easy to think you can just skimp out on this step.
It’s also too easy for things to go wrong in your manufacturing, and the last thing you want is for customers to get back to you saying your products are faulty or misshapen.
Candles are a fairly easy thing to check. So, time-wise you might think there’s little that can be done.
But you can always try to inspect in bigger batches or make sure that you do the inspections in one place so that there isn’t stock constantly being moved around.
There’s a whole load of inspection equipment out there too, to help you get more accurate in your detective work.
3. Moving
It’s inevitable that materials and products will have to move around.
That doesn’t mean that changes can’t be made.
In our candle example, everything is moved by hand, which of course slows moving down. But what about using trolleys to move the batches?
Certainly, it would be an added expense, but the amount of time saved would quickly make up for it. As long as the resources are there, and you haven’t reached the limits of light speed, the options for reducing moving time are always available too.
4. Queueing
Waiting is one of the most boring and necessary evils of life. There’s a whole play based on that concept called Waiting for Godot if you want to check it out.
But one of the great things about running a manufacturing business is that there’s always something to do. So, reducing queueing can be more about what else you can fit in that time to reduce the overall throughput time.
For example, you could make the candle holders at the same time as the wax is melting.
Half the queueing, half the time.
Final thoughts on throughput time
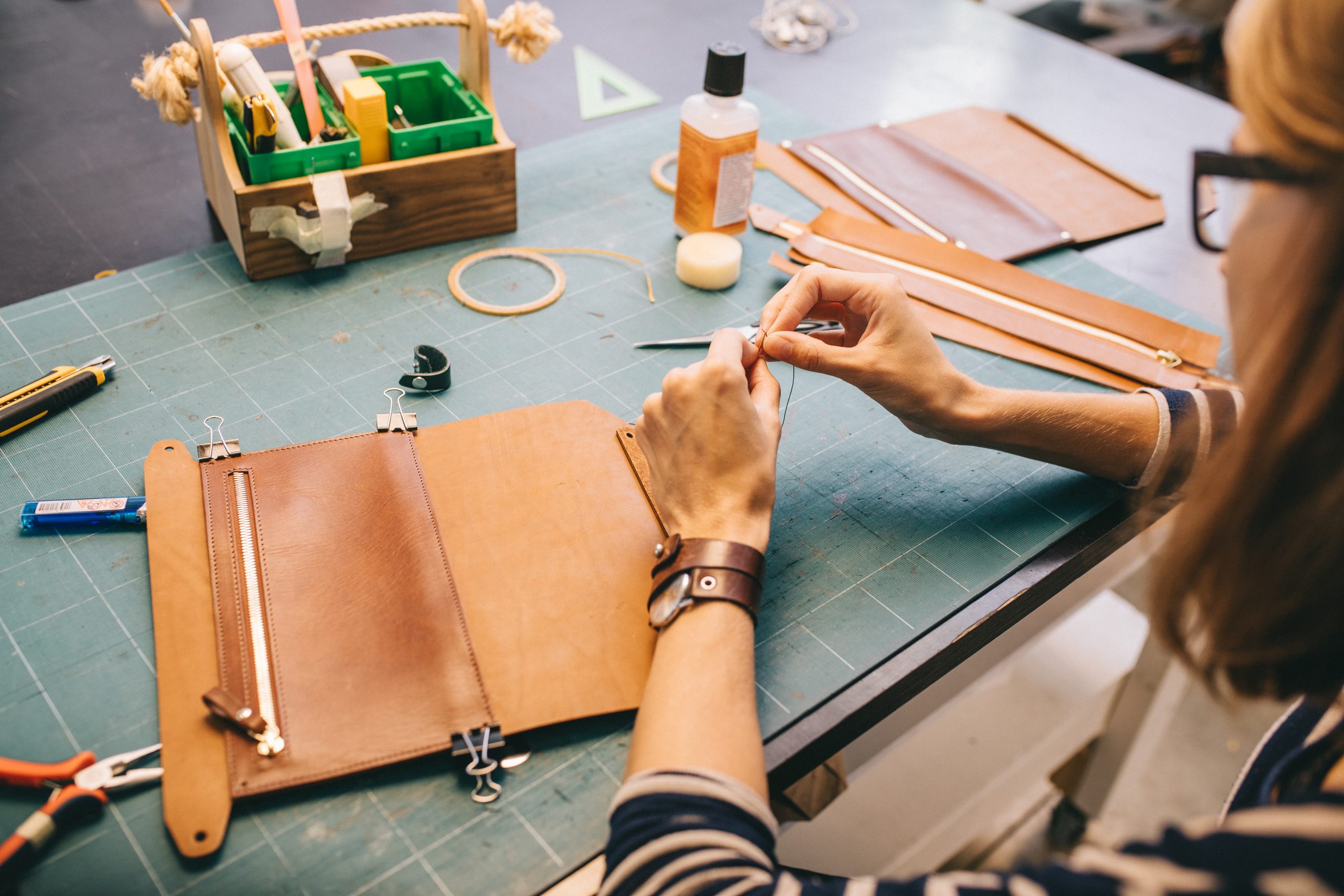
Throughput time is one of those metrics that every maker can make use of.
It doesn’t matter if you produce feather hats, wooden scissors, or even lipstick – all of them will have room for improvement.
The point here is to reduce the horror of your production into bitesize chunks which you can analyze from afar, before getting your hands dirty and making those vital time-sensitive modifications.
Your production planning and scheduling can be on point this way.
It might seem at first that you’re not getting too far. But every second counts here.
If you can reduce your throughput time for a product enough that it gets done in one day rather than two, then your customers can get their delivery faster, too.
Plus, you can start to reduce your carrying costs by being more efficient with your inventory management.
But we know what you might be thinking…this is a lot of information to gather.
And if you’re still working with spreadsheets, then that might be true.
Thankfully, though, Katana’s cloud-based inventory solution keeps your entire production workflow from start to finish.
Every bit of data is neatly arranged and kept up to date by the system in absolute real-time.
Apart from the convenience of having your purchasing, production, and online sales in one place, you can work out your throughput time, in half the time.
That means you can finally channel your inner cheetah and start running your workshop like a well-oiled machine.
Team Katana
Table of contents
Get inventory trends, news, and tips every month
Get visibility over your sales and stock
Wave goodbye to uncertainty with Katana Cloud Inventory — AI-powered for total inventory control