Wrapping your head around manufacturing cycle time
Manufacturing cycle time looks into the period from converting materials into a finished product, including the production process, travel, quality inspections, and waiting time. Using this article, you can learn about it and how to implement a manufacturing cycle time process.
Team Katana
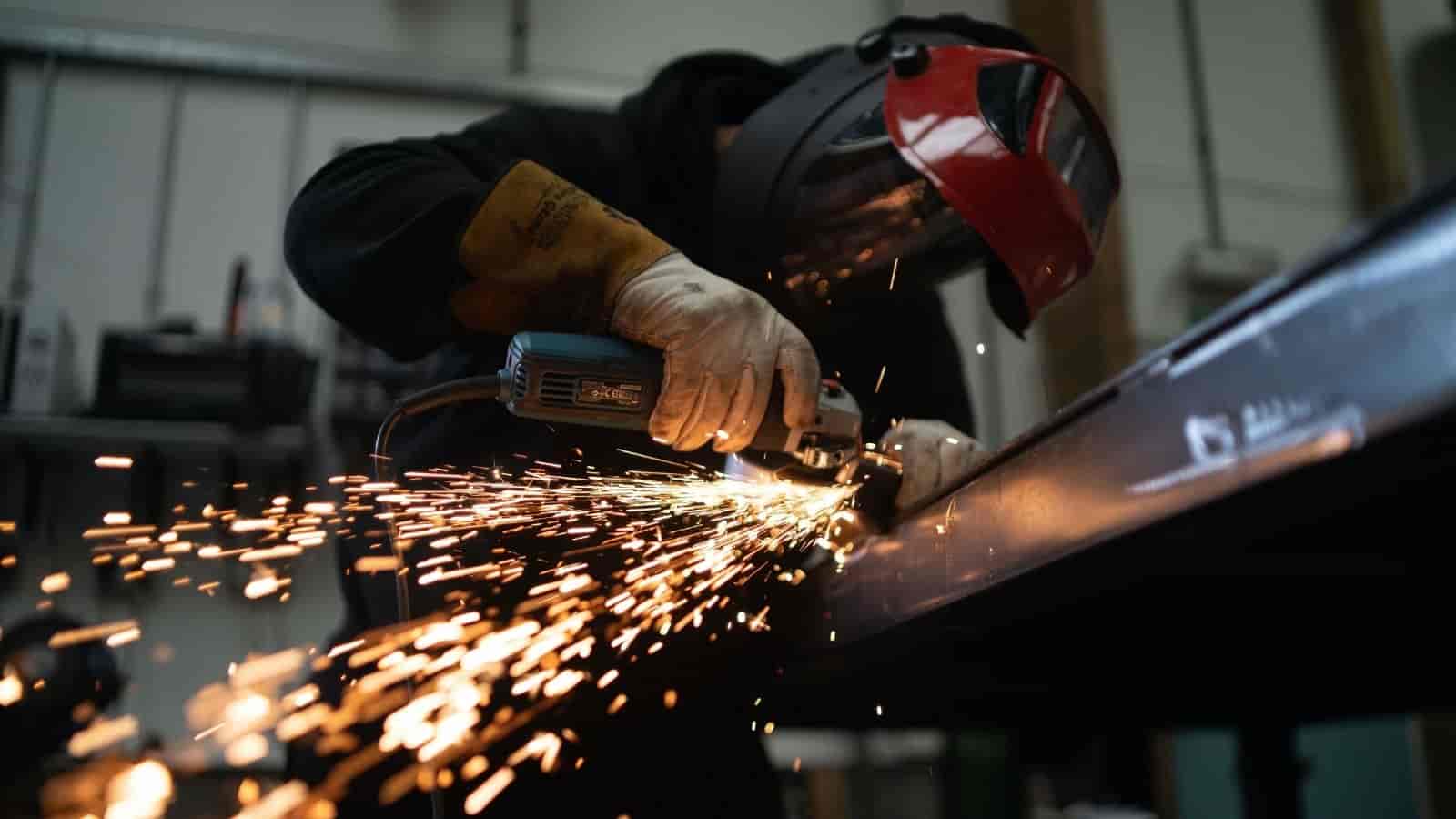
A successful product manufacturing operation is only possible for manufacturers with accurate cycle times.
But, what happens when you can’t measure or track how long it will take to produce and package deliverables, so they are ready for shipping to the consumer?
Manufacturing processes are never straightforward. Slow turnarounds may occur and severely impact your bottom line. The only way to prevent slow production and turnaround time is to understand how your manufacturing processes and cycle work.
In this guide, we explain everything you need to know about the production process by answering two essential questions:
- What is known as manufacturing cycle time?
- How do you calculate manufacturing cycle time?
Automate your manufacturing cycle time tracking
Katana gives you all the tools for managing your entire manufacturing business, from receiving supplies to manufacturing and shipping.
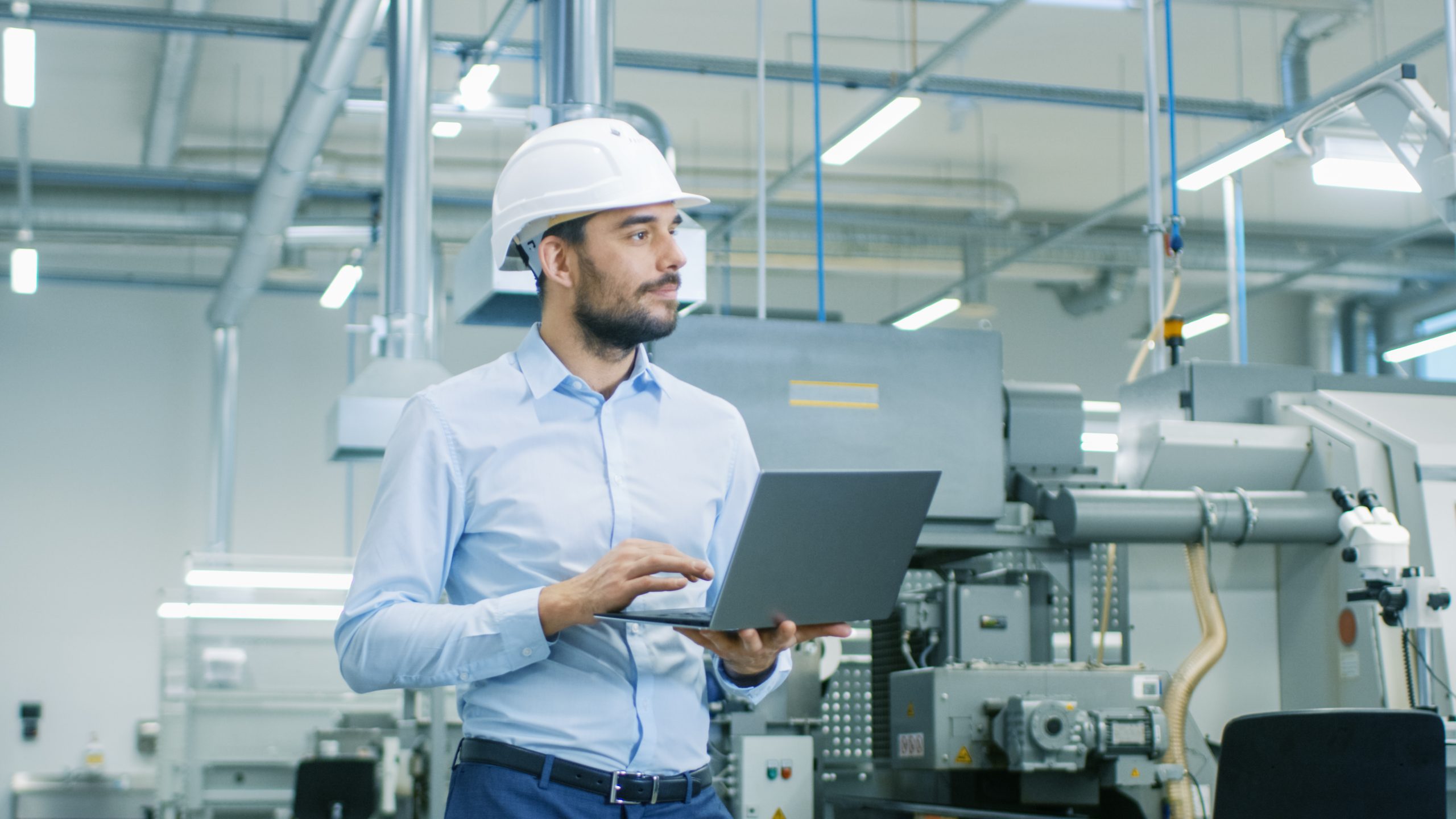
What is the manufacturing cycle time?
Manufacturing cycle time, or throughput time, is typically a KPI used in measuring the total time taken to transform raw materials into finished goods.
However, many people often misinterpret these metrics with some of its closest formulas like takt time and lead time. Cycle time, lead time, and takt time are all key metrics in lean manufacturing — a process that helps business owners minimize waste and maximize productivity during the manufacturing process. However, they differ significantly in their formula and what they measure.
Takt time measures the pace or speed at which the manufacturing process is completed to satisfy customer demand.
On the other hand, lead time measures the total amount of time from order placement to payment and delivery stage.
Although these two concepts are like cycle time, they differ in that takt time emphasizes production speed and turnaround time. While manufacturing lead time focuses on the customer perspective of time spent from when they make an order to when you deliver. So, what is cycle time in manufacturing?
Cycle time helps business owners, manufacturers, and product managers analyze and track product duration from start to finish.
For example, if you bake bread for sale, the throughput time tells you how long it will take to make just one bread from obtaining the raw materials to the end of production, where the raw materials for the bread are pieced together and packaged.
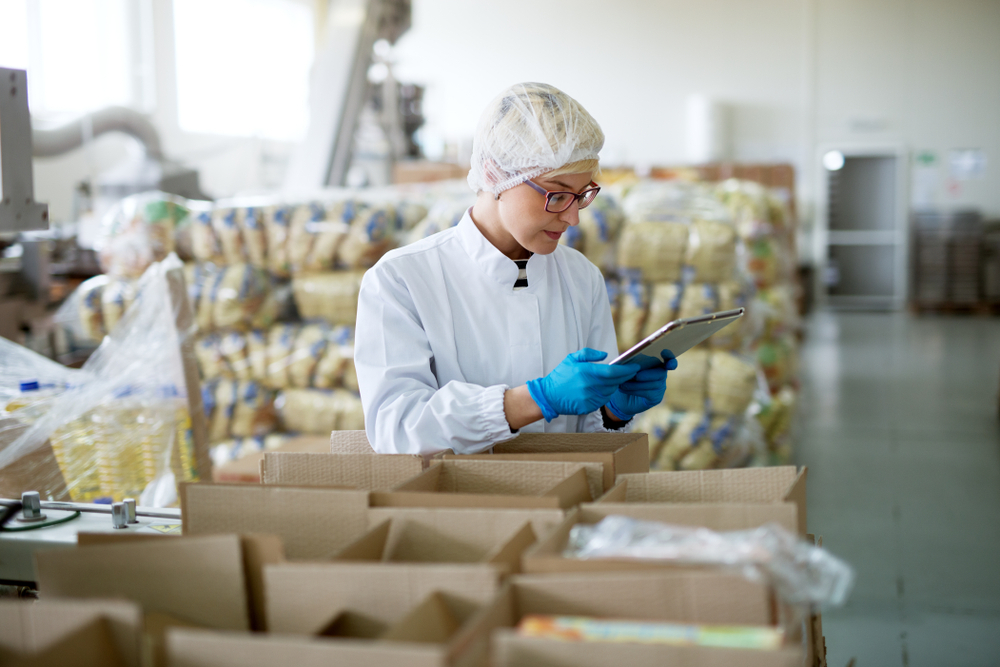
Why track the manufacturing cycle?
Efficiency and productivity are the key goals of using cycle time KPI in businesses.
Every business works on a different scale. Using these key metrics to track time spent in the manufacturing operation will provide access to data collection that describes value added in day-to-day operations. Yet, it doesn’t end there.
When business owners use this time formula, it exposes inefficiencies within production operations to facilitate improvement. So, once you have an idea of the throughput time and find certain loopholes causing a slow turnaround, you start to channel them for better productivity.
Other benefits of calculating cycle time include:
1. Increased profitability
Calculating cycle time helps you understand where time is mostly spent in production, so you know where to cut back on time and increase profit.
2. Consistent production rates
Cycle time helps organizations understand their production flow to eliminate excess waste and increase productivity.
3. Customer satisfaction
Customers need realistic product development timelines to stay loyal to your business. Tracking cycle time helps determine the exact delivery timeframe customers can trust.
4. Gain a competitive advantage
Cycle time helps businesses stay ahead of the competition by offering real-time data on a delivery time range. This way, if business owners operate snail-like production, they can hasten their production time and gain a competitive advantage.
5. Clear insights on business spending
Paid individual processes must add value to your production process, but some don’t. Business owners, manufacturers, and product managers can understand expense management to optimize productivity by tracking cycle time. In short, cycle time allows you to get better insights into your business processes.
How do you calculate manufacturing cycle time?
To calculate the cycle time, you need to consider both the time required to complete manufacturing which is the productive and non-productive hours.
The productive hours comprise two key elapsed times, the processing and inspection stage:
- Process time — it is the time spent on the actual manufacturing process. For example, if you own a bakery, a good example of process time is when you mix the dough
- Inspection time — this is the time spent on ensuring little to no defects in the product. It is a quality control measure that should be included in your production quality control checklist
On the other hand, the non-productive hours comprise the move and queue time or idle time:
- Move time — this is the load and unloading stage when materials and products are transported between the warehouse and workstations
- Queue time — this is the waiting time before any task commences
The cycle time formula
From the explanation of how to calculate cycle time in manufacturing, we can draw our formula as follows:
Cycle time = Net production time (per product)
However, the formula above may seem too complicated to grasp. A straightforward formula to consider is:
Non-productive hours + Productive hours (per product) = Cycle time
or
Process time + Inspection time + Movement time + Queue time (per product) = Cycle time
Take control of your cycle time
Katana cloud manufacturing software helps you get more control over your shopfloor instead of running circles trying to identify issues. Manage your entire manufacturing business from one place.
Using Katana for calculating manufacturing cycle time
Sometimes, no matter how clear your calculation is, the chances are that you may miss essential data causing costly downtime.
The good news is that reducing cycle time losses is possible when using cloud manufacturing software to calculate cycle time.
A good cloud solution to consider is Katana. Katana helps track the necessary data and information related to the manufacturing process to provide valuable real-time insights into the manufacturing cycle time. These reports and analytics identify areas where improvements can be made so that the necessary changes improve the cycle time.
How does Katana track cycle time? Here are some noteworthy easy-to-use features Katana uses for calculating cycle time:
Live inventory management
Katana offers live inventory management. Visual real-time feeds help you keep track of inventories, from raw stocks to finished products. This way, you can measure estimated production time, automate inventory transactions, calculate actual cycle time, and eliminate hitches and inconsistencies in your stock levels.
Use custom workflow via API
Katan’s flow diagram gives you visual data of your work in progress. This feature works well with the live inventory feature, so you view your production process in real-time.
No more going round and round with manufacturing cycle time
Nobody wants to lose loyal customers or risk costly downtime due to overcommitments and production laxity.
Fortunately, understanding your manufacturing processes and cycle time helps prevent these discrepancies while ensuring efficiency and productivity. Whether you are using cycle time for your large or small-scale business, it will not only measure how much you are producing but is an essential metric that improves the way your business runs while driving profitability, quality products, and consumer retention.
Team Katana
Table of contents
Get inventory trends, news, and tips every month
Get visibility over your sales and stock
Wave goodbye to uncertainty with Katana Cloud Inventory — AI-powered for total inventory control