10 key inventory management terms you should master

Ioana Neamt
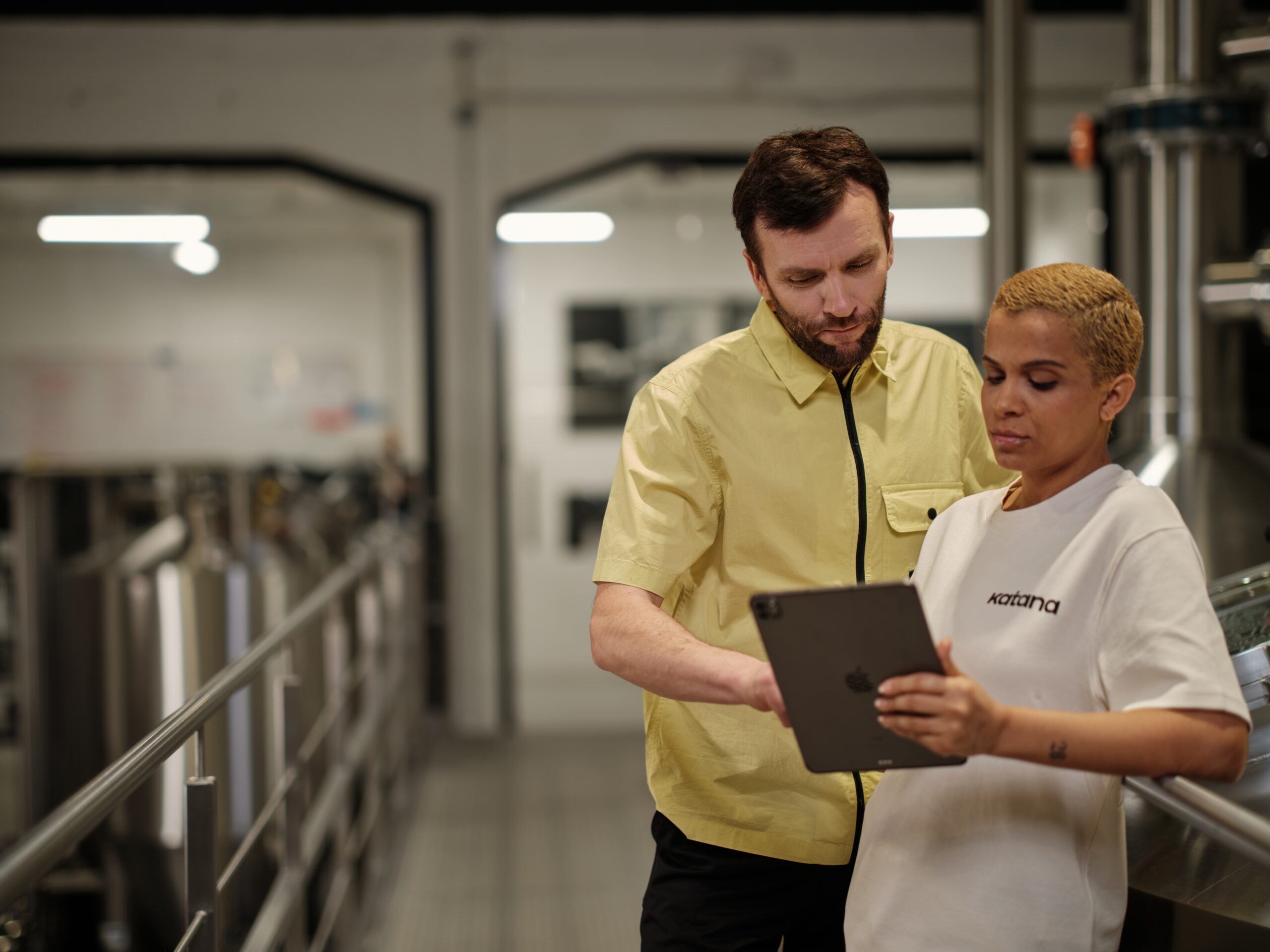
You won’t find any of these terms helpful for Wordle, but you might try using this knowledge to score some points at Scrabble. That is, of course, when you are not busy applying it to unlock the benefits of good inventory management for your business. Understanding the concepts presented below will help you optimize stock levels, reduce costs, prevent stockouts, and improve the overall operational efficiency of your business.
1. Inventory
This term primarily represents the totality of goods or materials that your business holds for future sale or use. It can also refer to the detailed record of the totality of these goods and materials. Overall, it is generally broken down into four main categories:
- Raw materials, which incorporate components that can be used to create products that you then sell
- Work-in-process inventory (WIP) refers to items that are in the process of becoming finished products
- Finished goods, which refers to inventory consisting of products that are completed and ready to be sold
- MRO inventory, which stands for maintenance, repair, and operations supplies that are needed to keep your production going
2. Stock keeping unit (SKU)
A stock keeping unit is a unique identifier that is assigned to each item in your inventory. This is done to help you accurately track and manage the levels of all types of inventory in your care. It includes several details about the product, such as its size, color, material, and packaging. SKUs are essential to accurately accounting for your stock and to help you streamline all your inventory management processes.
As your business grows, an SKU generator will be one of the handiest tools at your disposal to help you keep your inventory well-organized. You’ll find it is most useful in tracking items across everything from lists to invoices, throughout all steps of the manufacturing process, and in purchase orders.
Easily track and assign SKUs with Katana cloud inventory software. Contact us for a demo to find out more.
Want to effortlessly generate SKUs?
Generate unique stock keeping units and assign them to all your product variants with this free SKU generator template.
3. Inventory turnover
Inventory turnover refers to a way of measuring how efficiently your business manages inventory. It is a calculation of the number of times that inventory is sold and replaced within a specific period of time (usually a year). If your inventory turnover is high, that is a sign of very efficient inventory management. On the other hand, a low turnover is seen to suggest that your business might be facing challenges like overstocking or slow sales.
Once you get a good understanding of it, your inventory turnover calculation should tell you things like whether you are holding too much inventory at one time, if you have enough sales, if your costs are too high, or if you’ve done a good job of keeping up with customer orders.
4. Lead time
Lead time refers to the duration between when an order for a product is initiated and when it is received. This includes the time that is required for the production, transportation, and delivery of the product.
It is very important to consider lead times when managing your inventory, as they can make a notable difference in successfully preventing stockouts and optimizing inventory levels. Ultimately, whether it is the manufacturing lead time or the delivery lead time, your aim should be to reduce them as much as you can, without sacrificing your standard of quality.
5. Reorder point
The reorder point marks the level of inventory at which a new order needs to be placed to avoid stockout. When you calculate a reorder point, you need to take into account factors such as lead time, daily demand, and safety stock. Accurate reorder point calculation is especially important for maintaining optimal inventory levels and preventing any disruptions in the supply chain, such as breakdowns or bottlenecks.
A reorder point is necessary to alert you not only when the right time is to order more materials from your suppliers but can also be set to alert you about the right time to make more sub-assemblies and products.
6. Stockout
We have already used it a few times in this article, so it’s about time to define it. A stockout means running out of a product for which you have unfulfilled orders. This is, of course, undesirable for all parties involved.
If you cannot fulfill the order to a customer in the usual, advertised, or expected time, they might change their mind and back out of the purchase. In addition to potentially lost sales, stockouts can lead to a level of customer dissatisfaction that can damage your company’s reputation. Needless to say, your inventory management strategy should aim to keep this situation from occurring, as much as possible.
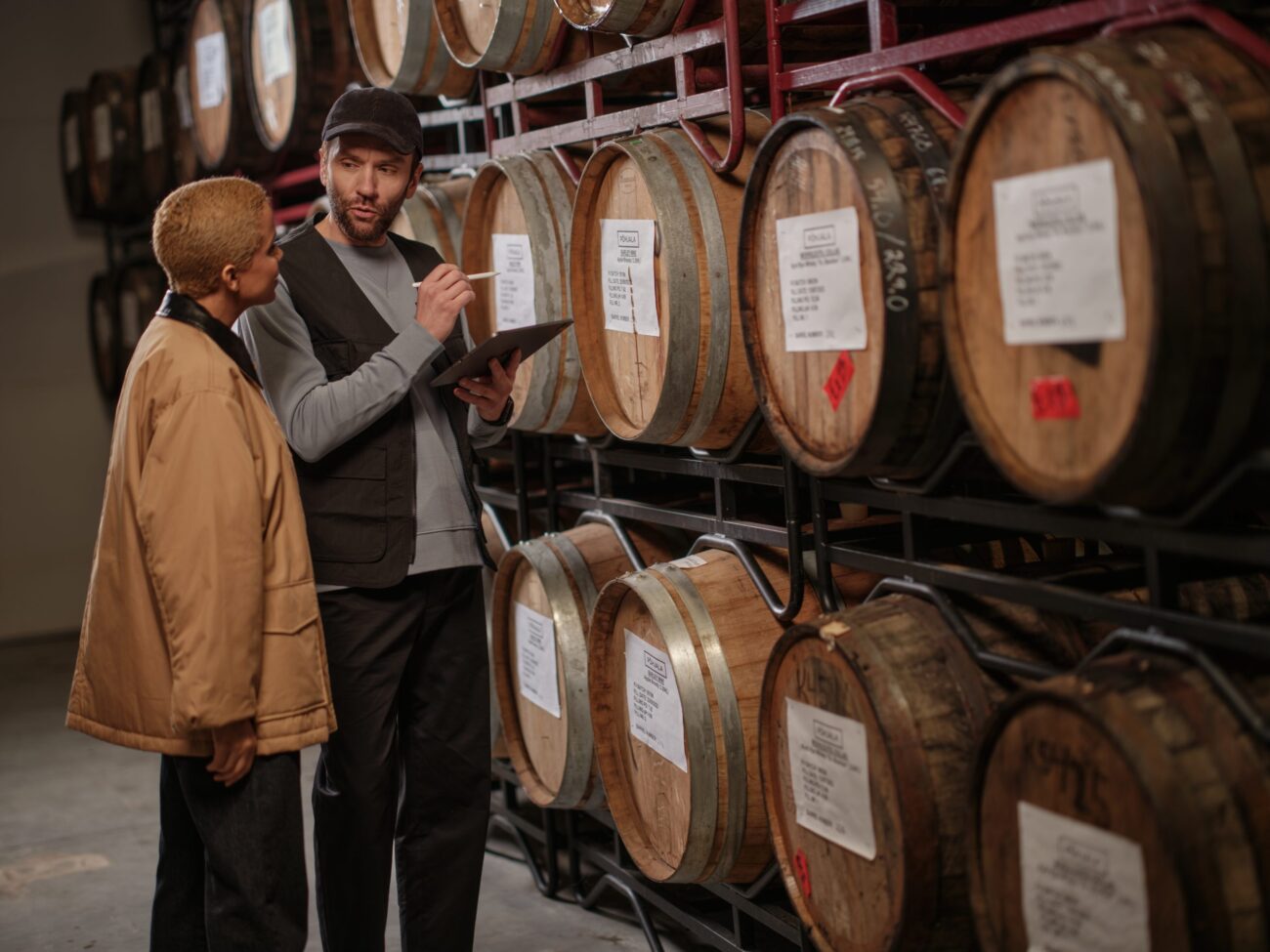
7. Safety stock
You can probably tell by now that the fear of running out of any inventory that is in demand is all too real. Safety stock represents a key hedge against finding yourself in that situation. This term refers to extra inventory that is held in reserve in case of unexpected fluctuations in demand (a sudden surge of interest compared to your usual sales trends) or any supply chain disruptions that might cause delays in your usual replenishment of certain inventory.
It is worth noting that, although it helps prevent the occasional stockout, it does incur an increase in carrying costs. The tricky part is determining the appropriate amount of safety stock that won’t hurt your budget more than it helps your sales.
8. Carrying cost
Carrying cost refers to the expenses associated with holding inventory. Such costs include:
- Storage fees (warehouse space and storage rent)
- The work time that was spent handling the inventory
- The cost of transporting it
- Insurance
- Taxes
- Loss by obsolescence or spoilage
- The opportunity cost of capital that is tied up in inventory
In order to maintain profitability where you want it, it is essential to manage your inventory in such a way that you minimize carrying costs. The longer it takes for inventory to sell, the more the carrying cost adds up, which will also be apparent in your lower inventory turnover.
9. Order quantity
Order quantity refers to the number of units ordered from a supplier in a single purchase. This term comes with a little bit of a challenge, as you will need to determine what the optimal order quantity is, in such a way that it balances your ordering costs and your carrying costs.
You’ll generally find it referenced in two ways:
- MOQ is the minimum order quantity, which represents the smallest quantity of product that a supplier is able to produce or is willing to sell.
- EOQ stands for economic order quantity and represents the optimal number of products to minimize ordering and holding costs.
10. Inventory valuation
Inventory valuation refers to the process of assigning a monetary value to inventory, for purposes of accounting and financial reporting. There are different inventory valuation methods that you can employ, and each has an impact on the cost of goods sold and the value of inventory on the balance sheet. An inventory valuation should be done periodically and the method you choose should be reflective of your company’s cost structure.
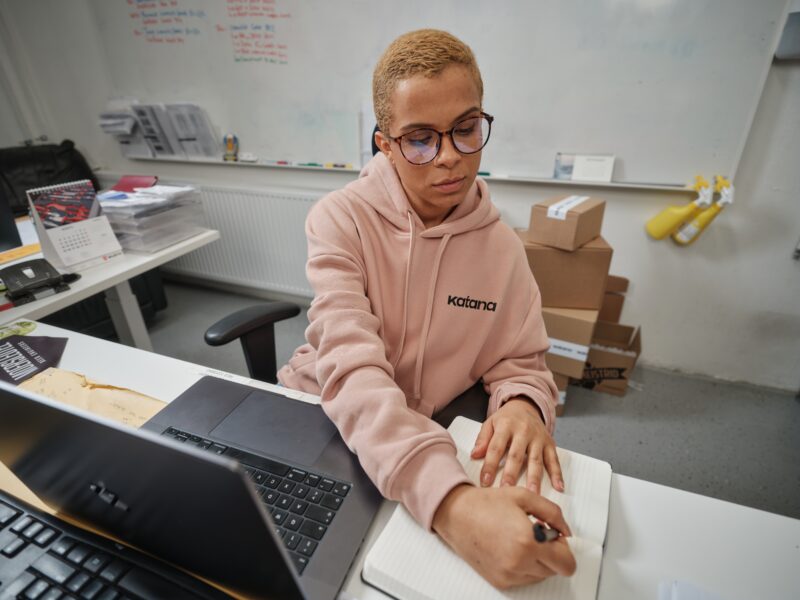
Master inventory management with Katana
Feeling enlightened enough to take a deeper dive? Get the ultimate inventory management guide for an in-depth walk-through of benefits, challenges, and best practices for keeping track of your stock.
Katana inventory management software can help you organize and grow your business effectively:
- Planning and forecasting features that provide data-based insights for your management strategy decisions
- Easily set reorder points for each item in your inventory, so you always know when replenishment is due
- Seamless integration with your business tools puts Katana at the center of your operations, and makes it easy for you to handle your entire flow from purchasing to sales on one platform
- Track stock levels across various locations with multilocation support and across all your sales channels (online and offline) with multichannel inventory visibility
- Make the most of end-to-end traceability for materials and products to identify issues early, avoid holding on to expiring stock, ensure timely maintenance, and more!
If you want to see solutions in action, contact us to get a demo!

Ioana Neamt
Table of contents
SKU
Get inventory trends, news, and tips every month
Get visibility over your sales and stock
Wave goodbye to uncertainty with Katana Cloud Inventory — AI-powered for total inventory control