Your inventory audit quick guide
This quick guide explores best practices, procedures, and benefits of inventory audits, empowering you to reduce errors and maximize profits.

Ioana Neamt

Depending on how nerdy you are when it comes to technology, but also business in general, learning new things about various technical terminologies can sometimes be quite daunting. That’s why today we’ll try our best to explain the inventory audit with an analogy — running a restaurant.
What is an inventory audit?
An inventory audit consists of a physical count of the goods in your warehouse and/or in transit, cross-checked against financial records. This is to eliminate discrepancies between your actual inventory and records.
Imagine your business is a restaurant. Your inventory makes up the ingredients in your kitchen. An inventory audit is like a chef taking stock of the pantry before a big rush. It ensures you have the right amount of everything — enough flour for bread, enough cheese for pizza, and enough vegetables for salads — to fulfill orders or, in this case, serve hungry customers smoothly.
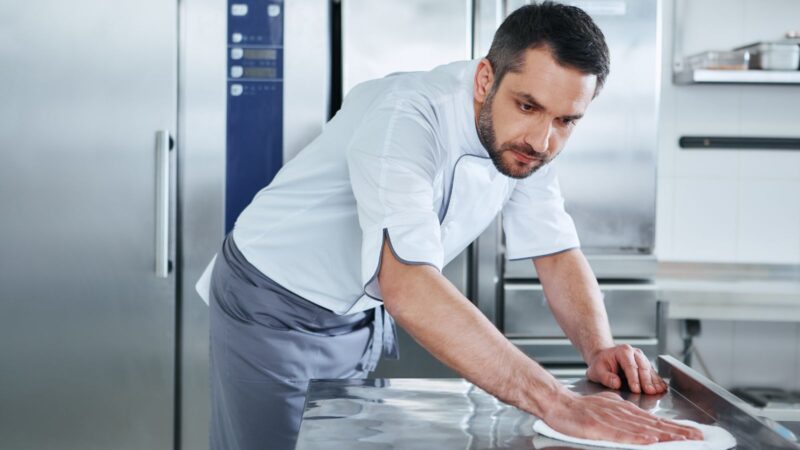
Why is inventory auditing important?
There’s not only one reason why inventory auditing is crucial when running a business. There are several points you should focus on here:
- Improved accuracy — Having accurate inventory records is essential for not only calculating profits and budgeting effectively, but also making informed purchasing decisions.
- Reduced shrinkage — Imagine going through the loss of inventory due to theft, damage, or administrative errors. Regular audits help identify shrinkage and implement measures to prevent it.
- Enhanced planning — Every entrepreneur has to be aware of and understand their inventory levels alongside sales trends. By doing so, they’ll be able to forecast future demand and make informed decisions about purchasing and production. This helps avoid stockouts and reduces the risk of having excess inventory that ties up capital.
- Fraud detection — Constant audits can uncover instances of inventory fraud, such as employee theft or manipulation of records.
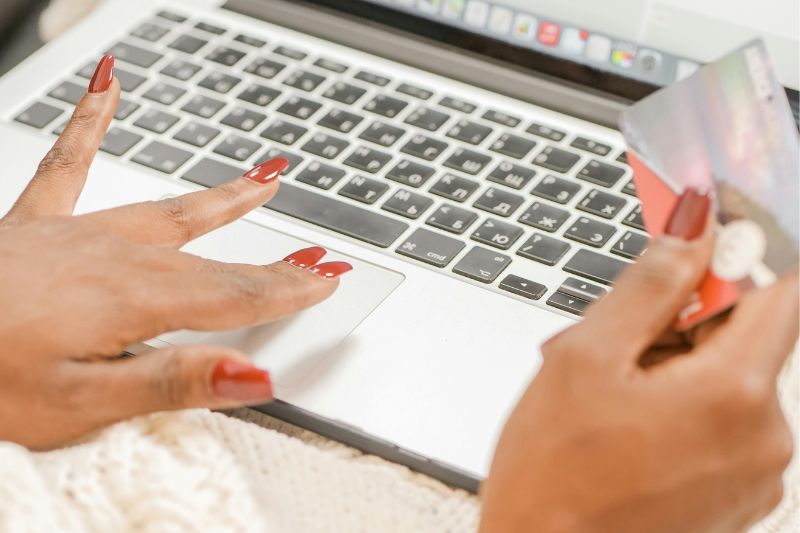
Inventory audit benefits
By now, you probably have an idea of what an inventory audit is and why it is important. While understanding the importance of it might seem like a good enough benefit, there are still some aspects of inventory auditing that we’d like to point out.
- Profit calculation — Accurate inventory records directly affect your bottom line. Inventory audits help identify discrepancies and ensure your cost of goods sold (COGS) is calculated correctly, leading to a more accurate reflection of your profits.
- Accurate budgeting — When you don’t have accurate inventory data, budgeting becomes a guessing game. Luckily, audits provide a clear picture of your inventory levels, allowing you to allocate resources more effectively when planning for future purchases, like the sauce, flour, cheese, oregano, or mushrooms, to name a few ingredients.
- Identifying inefficiencies — Inventory audits can reveal inefficiencies in your inventory management system, such as slow-moving products, inaccurate storage methods, or overstocking — and sometimes even employee errors.
- Optimizing inventory levels — Holding too much inventory can tie up capital and incur storage costs — and no one likes to see good ingredients go to waste. Also, insufficient inventory can lead to stockouts and lost sales. Inventory audits help you achieve a balance by being able to identify the optimal inventory levels for each product.
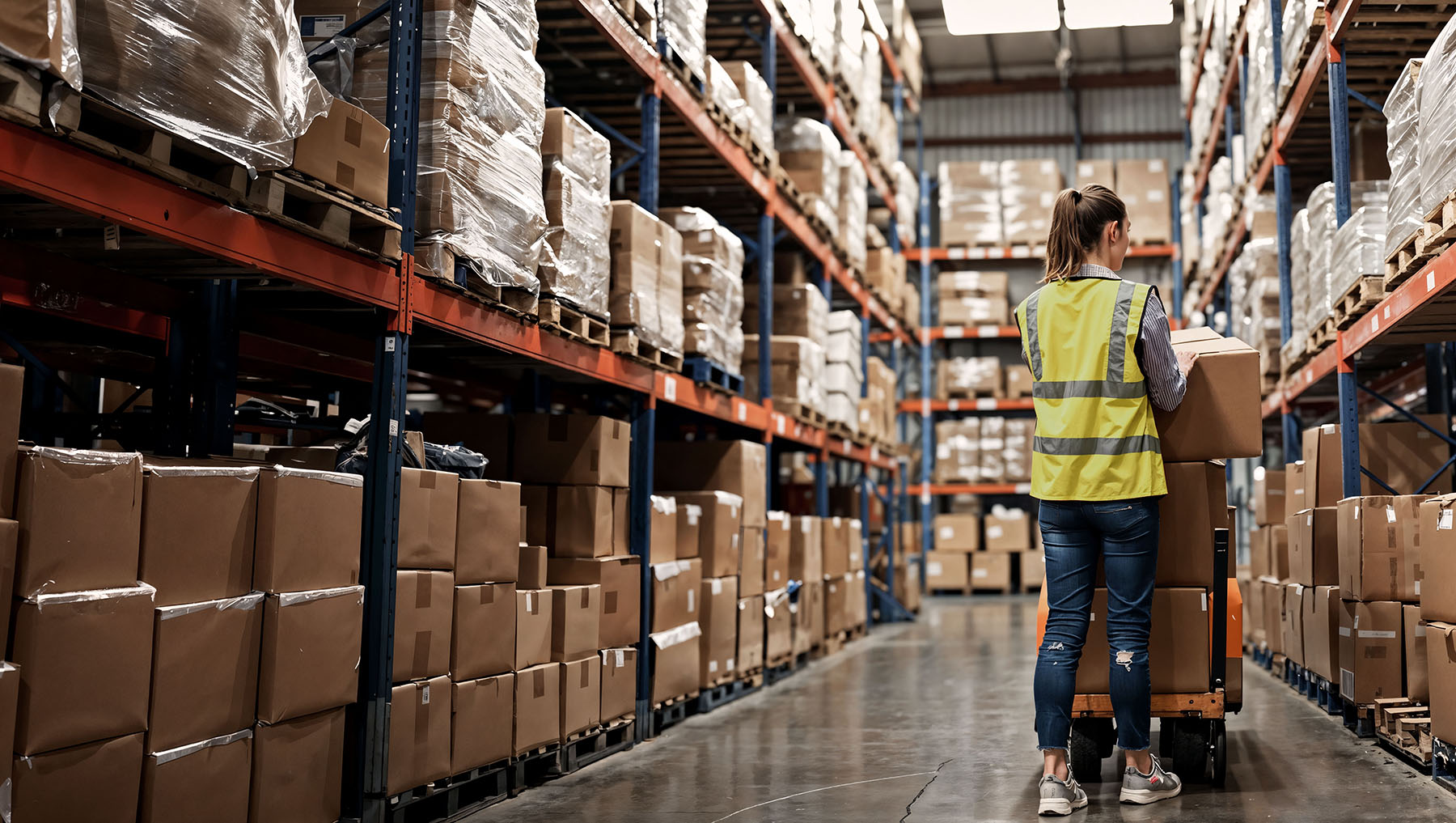
Inventory audit procedures
Now that you’re a bit more familiar with inventory auditing, let’s explore the different procedures involved here.
ABC analysis
ABC analysis categorizes inventory items based on their value and volume.
- High-value (A) items receive the most attention during the audit
- Items marked as (B) are somewhere in between, as they’re usually not that important
- Low-value (C) items may not be in focus right away
Let’s see it in a concrete example:
High-value items here would be key ingredients, like premium cuts of meat and fresh vegetables for signature dishes. These items require a more meticulous counting process.
The secondary ingredients, marked with B, are the supporting ingredients, or moderate-value items that deserve attention.
C items are pantry staples, or to be more exact, low-value items that can be counted less frequently.
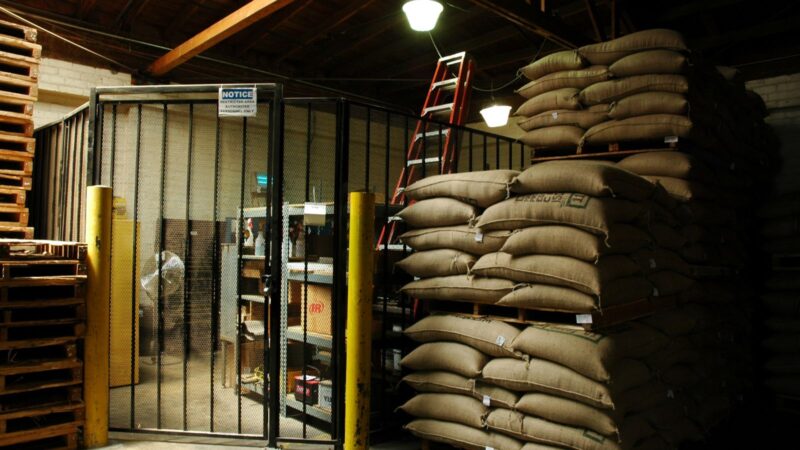
Cut-off analysis
To ensure the headcount is accurate, your kitchen needs a designated time to pause all incoming and outgoing deliveries, or in this case, ingredients.
This cut-off period helps prevent discrepancies caused by last-minute orders. This also applies to deliveries that might not be included in the inventory records at the time of the count. Imagine it as the chef pausing all new orders before taking stock of what’s already in the pantry.
Finished goods cost analysis
When a product is being made and is officially certified as finished, that’s where the cost analysis comes into play. This type of analysis is crucial for manufacturers. It helps determine the value of finished products for accounting purposes — and nobody wants to have problematic books.
Freight cost analysis
Freight cost analysis revolves around including transportation costs associated with getting inventory to different locations in your overall inventory valuation. Renting two vans on a weekly basis just to transport a couple of cases of tomatoes would be a bit excessive.
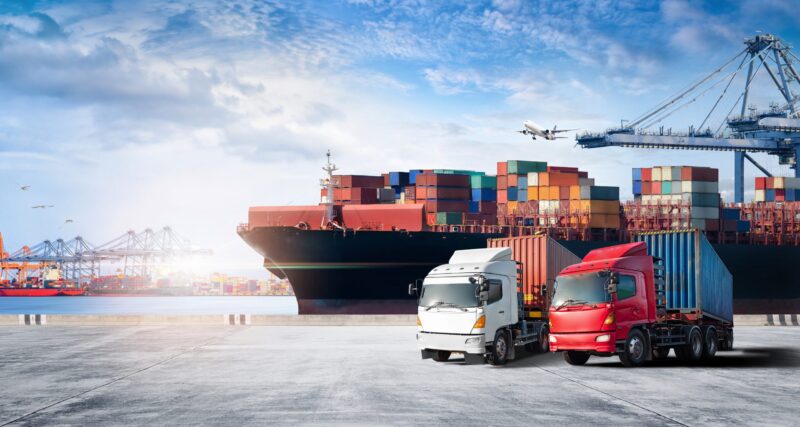
Overhead analysis
Overhead costs should not be overlooked when doing audits or cost reviews. You need to factor in non-direct expenses that occur during production to optimize your spending and make sure you’re allocating the right resources.
Reconciling items
After making sure that the whole inventory is in order, there’s still the need to compare it with the existing recipe book, which, in this case, is an analogy for inventory records.
If some discrepancies are found between the physical count and financial records, then there’s a need for a procedure to identify and resolve the issue. For example, investigating why some ingredients are missing due to spoilage or simply being misplaced, or even correcting errors in recording ingredient quantities.
Matching items
The final procedure in an inventory audit would be to match the items. This involves comparing physical inventory counts with both purchase orders and shipping logs. That way, the person running a business manages to ensure an accurate recording of received and shipped items.
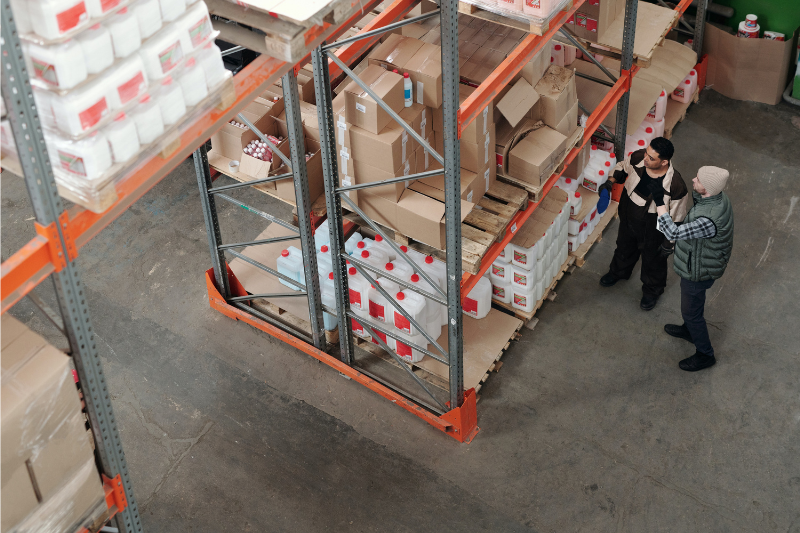
Best practices for an inventory audit
It’s time to focus on the practical aspect of inventory auditing. Here’s how it all works in practice.
As we briefly mentioned above, there’s a strategy for prioritizing your inventory. By conducting regular audits and focusing on high-value items during audits, there’s no reason why your business shouldn’t be successful.
Try to stay organized as much as possible. That way, regular audits shouldn’t be that big of a deal — if anything, it’s similar to keeping your house clean. Just make sure to tidy it up completely at least once a month and you’re good to go. Of course, some people do it more often, and some people do not, but as a business runner, make sure you’re more punctual than an average person.
Keep track of and gather all documentation, as it’s really important to have all the necessary documents on hand whenever you need them. Documents like inventory records, invoices, and shipping logs should be readily available for the auditors.
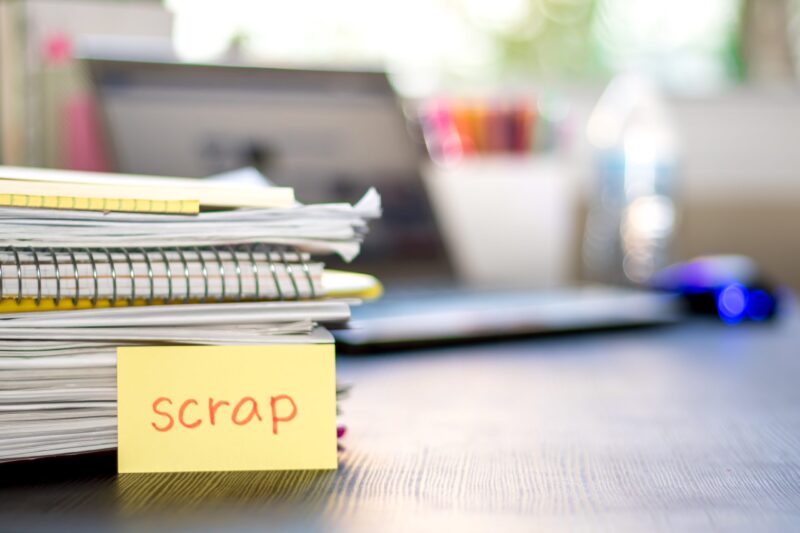
It’s also worth mentioning that scheduling regular audits is quite important. Being able to conduct regular audits, whether that be on a quarterly or biannual basis, helps minor discrepancies. They sometimes tend to snowball into major problems, like not cleaning the kitchen for a whole month. That could lead to not only potential time-related issues, but also problems with a sanitary inspection.
Getting help from external auditors is a good way of getting an unbiased perspective. That way, an external auditor can identify areas for improvement in your inventory management system.
Communication is key, which means that being able to communicate the audit findings with relevant stakeholders leads to ensuring transparency and implementation of correct actions where necessary.
Are there any challenges to running an inventory audit?
Inventory audits, while essential for keeping your stockroom in check, can sometimes be a real headache.
Physically counting everything, especially for businesses with a ton of items (SKUs), takes a lot of time and manpower. As your business grows and your inventory expands, managing audits becomes even more complex. Keeping track of numerous items, locations, and ever-changing demands can be overwhelming with traditional methods.
On top of that, manual counting is error-prone, leading to discrepancies between your actual stock and what your records say. This can tinker with your financial reports quite a bit and make it hard to make good business decisions.
This is where technology and automation come into play. With a robust and reliable inventory management software like Katana, you can automate your inventory audits and thus avoid human errors and speed up processes significantly.
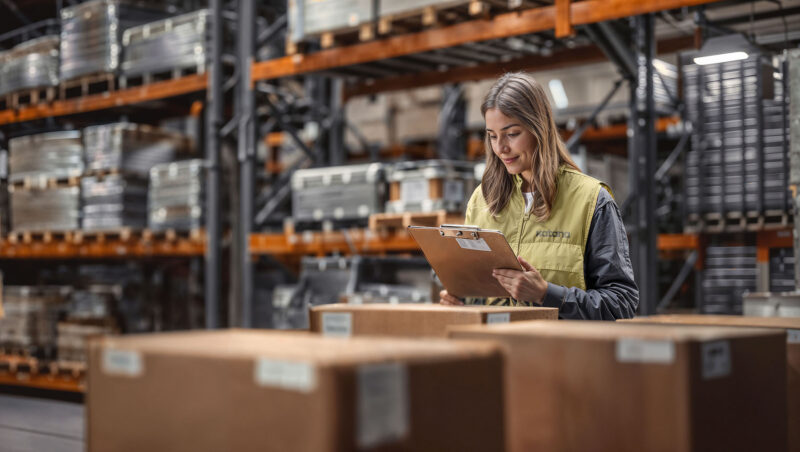
Improve inventory audit efficiency with Katana
Are you struggling with time-consuming inventory audits? No need to worry, as Katana can be of help. Our software automates real-time inventory tracking, eliminating the need for manual counting and saving you a ton of time and manpower.
Katana also grows with your business. It can handle even complex inventory structures, managing numerous items across multiple locations — all with ease. Plus, it integrates well with your existing accounting and sales systems. That way, it creates a central hub for all your inventory data. This allows Katana to analyze data automatically and generate reports.
Real-time insights into your inventory levels also allow you to identify not only areas for improvement, but also optimize stock levels before conducting a full audit, minimizing disruptions even further.
Get on a call with one of our experts to get a demo of our product and get answers to any questions you might have. Katana offers benefits like:
- Being able to easily manage incoming orders from all your sales channels and track products available for sale at the same time
- Manage different aspects of running a company, like production planning and resource allocation — all in real-time
- Issue purchase orders based on precise material requirements and reorder points
FAQs
The frequency of inventory audits depends on industry standards as well as the size and complexity of your business — you might be running a small pizza parlor or a huge restaurant. However, most businesses typically conduct full audits annually or biannually, with more frequent cycle counts for high-value items.
Absolutely — Katana’s many features, like centralized inventory data and real-time insights, can significantly improve your audit preparation.
Yes, we’re happy to say that Katana provides comprehensive implementation and ongoing support to ensure you understand how to audit inventory and get the most out of the software. Our dedicated team can help you not only implement Katana effectively but also leverage its features to make audit processes go as smoothly as possible.

Ioana Neamt
Table of contents
Get inventory trends, news, and tips every month
Get visibility over your sales and stock
Wave goodbye to uncertainty with Katana Cloud Inventory — AI-powered for total inventory control