Capacity utilization and how to calculate it
Optimal capacity utilization is the sweet spot between too much and too little production. Learn more about capacity utilization and how to calculate it as a manufacturer to maximize efficiency and reduce costs.
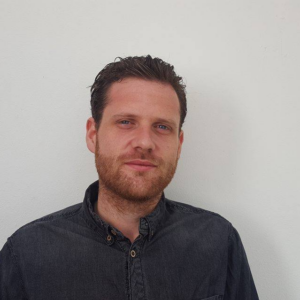
James Humphreys
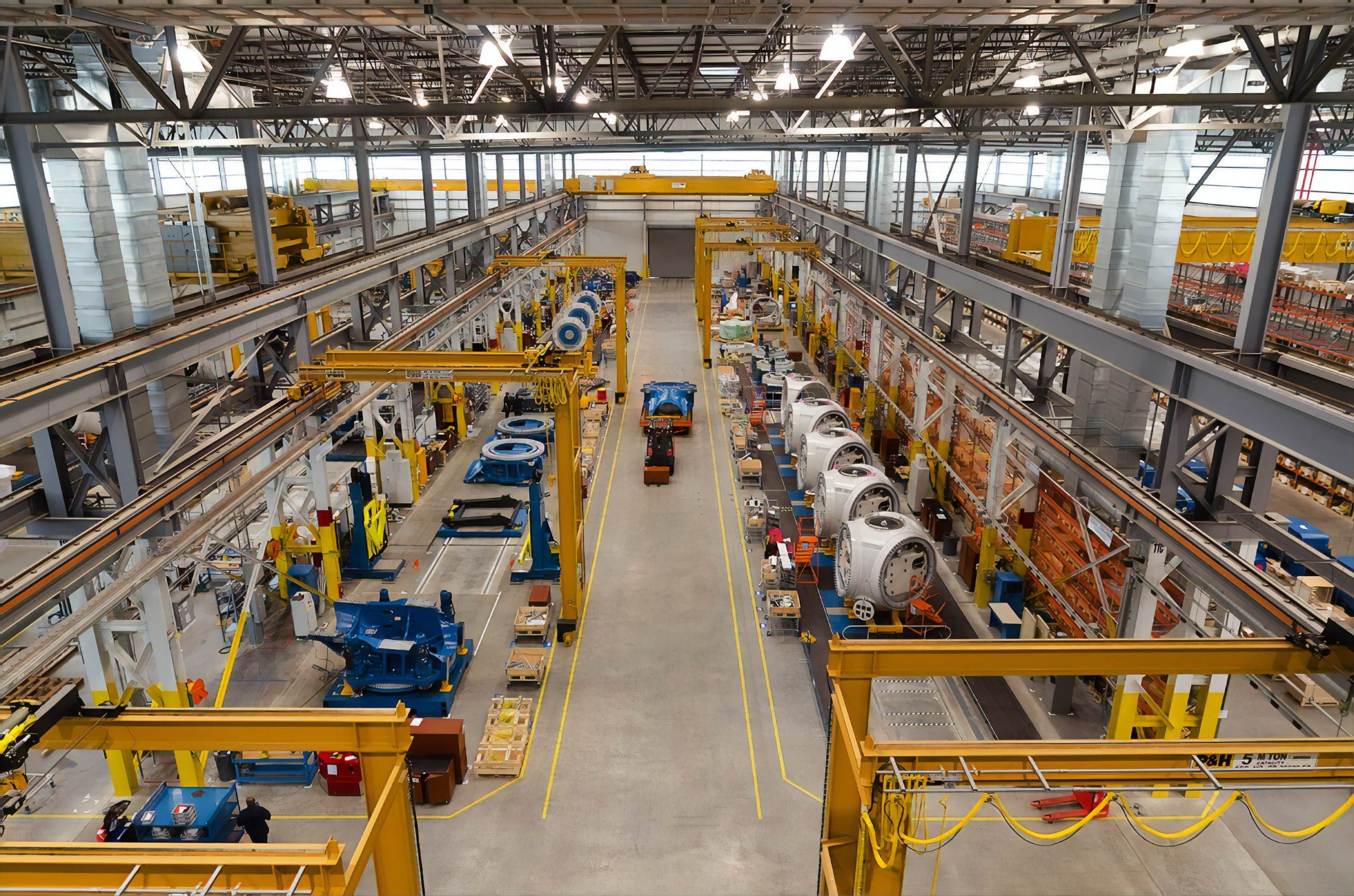
If you were to ask the layman about what percentage they believe a manufacturing plant should produce relative to its maximum, they might say 100%.
This would be incorrect.
Optimal capacity utilization is the sweet spot between too much and too little production. If a factory produces 100% of its maximum output, it is likely to experience bottlenecks, waste, and inefficiency.
On the other hand, if a factory only operates at 50% of its maximum output, it is wasting money on underused resources. The goal for any business should be to find that happy medium between over and under-utilization of capacity.
In this article, we will examine:
- What is capacity utilization in manufacturing?
- How do you calculate capacity utilization?
- What is a good manufacturing capacity utilization?
- A capacity utilization example
Ready? Crank up that conveyor belt and let’s get started!
What is capacity utilization (in manufacturing)?
Capacity utilization is a metric that measures the amount of output produced by a manufacturing plant relative to its maximum potential output. It is typically expressed as a percentage.
This important key performance indicator (KPI) helps businesses to track efficiency and optimize production while making sure they have room for sudden increased market demand if necessary. It can be used for individual factories, assembly lines, or even specific pieces of machinery.
One of the hardest things to understand for many businesses is when to slow down. If a company can produce more, it may be tempted to do so to meet customer demand and increase profits.
However, this can often lead to over-utilization of resources, which can then cause bottlenecks, waste, and inefficiency. The goal is to find that happy medium between too much and too little production.
How to calculate capacity utilization
The capacity utilization formula is relatively simple:
Capacity Utilization = (Actual Output / Maximum Potential Output) x 100
For example, if a factory has the potential to produce 10 widgets per hour but is only producing 8 widgets per hour, its capacity utilization would be:
(8/10) x 100 = 80%
When calculating capacity vs utilization, you need two pieces of information:
- The maximum potential output of the manufacturing plant
- The actual output of the manufacturing plant
The first piece of information is usually easy to find. Most businesses have a good understanding of their production capabilities.
The second piece of information can be more difficult to track down. You will need data on the number of products or services produced by your manufacturing plant over a specific period.
This can be done by tracking output at the individual machine level, or by tracking overall production for the plant.
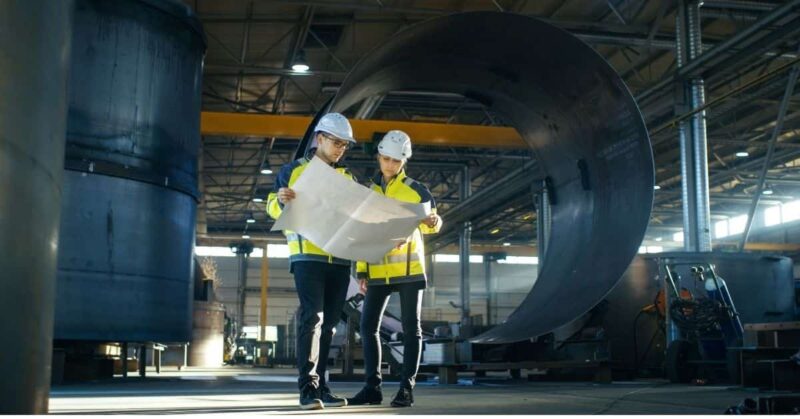
What is a good manufacturing capacity utilization?
While basic intuition may suggest that this number should be as high as possible, it isn’t the case. For most manufacturing plants, anything above 85% capacity utilization begins to cause problems such as:
- Excess inventory: If a factory is running at or near full capacity, it will likely build up excess inventory. This can be costly, as it ties up money in products that may not sell for some time and can cause an increase in external debt.
- Decreased flexibility: If a company is already operating at full capacity, it will have difficulty responding to an uptick in demand. This could lead to lost sales and decreased customer satisfaction.
- Inefficient use of resources: Running at full capacity rates can also lead to inefficiencies, as bottlenecks and other resource management issues arise. This can lead to increased costs and decreased quality control.
- Shipping delays: If a company is unable to keep up with demand, it may experience shipping delays. This could lead to unhappy customers and lost sales.
- Wasted materials: If a manufacturing plant is producing more than what is needed, it may end up wasting materials. This not only increases costs but also hurts the environment.
- Machine breakdowns: When machines are running at or near full capacity, they are more likely to break down. This can lead to production delays and increased maintenance costs.
For these reasons, most businesses aim for a capacity utilization rate between 80 and 85%. This leaves some room for error while still maintaining a high level of efficiency.
It is important to keep in mind that capacity utilization is not a static number. It will fluctuate over time as demand for your products or services changes. As such, it is important to track capacity utilization over time, ideally with the help of production management software, so that you can identify trends and make adjustments to your production as necessary.
Capacity utilization example
Introducing FakeMFG, our example manufacturing company that we can use to illustrate capacity utilization. They have opened a facility to produce chairs, their flagship product. The factory has the potential to produce 90 chairs per day.
- On Monday, FakeMFG produced 78 chairs
- On Tuesday, they produced 68 chairs
- On Wednesday, they produced 73 chairs
- On Thursday, they produced 64 chairs
- And on Friday, they produced 77 chairs
To calculate capacity utilization for the week, we simply take the average of the daily production numbers:
(70 + 68 + 73 + 64 + 77) / 5 = 70.4
We then plug this number into the capacity utilization formula:
(70.4/90) x 100 = 78.2%
This means that, on average, FakeMFG was operating at 78.2% of its maximum potential output level for the week. Since this is lower than our target of 80 to 85%, the hypothetical manager has a problem on her hands. There are a few ways she could increase her capacity utilization by a few percentage points:
- Examine the days with a lower output to discover why production was down
- Make changes to the factory floor to increase efficiency
- Run the factory for longer hours or reassess the production schedule
- Hire more workers
All of these options come with their own set of pros and cons, so the manager will have to weigh her options and decide which is best for the company. No matter what decision she makes, it will not be done in a vacuum.
Constant monitoring will be necessary to make sure that capacity utilization remains at an optimal level, and does not increase to the point of risking the operation.
Final thoughts
Capacity utilization is the measure of how much output a manufacturing plant is producing compared to its maximum potential output. It is typically expressed as a percentage and serves as an important KPI for businesses to track efficiency and optimize production.
The optimal capacity utilization rate will vary from business to business but generally falls between 80 and 85%, leaving room for increased demand and unexpected production hiccups.
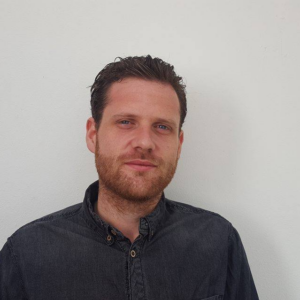
James Humphreys
Table of contents
Get inventory trends, news, and tips every month
Get visibility over your sales and stock
Wave goodbye to uncertainty with Katana Cloud Inventory — AI-powered for total inventory control