BOM cost analysis: How to calculate BOM effectively
Smooth manufacturing processes and quality products rely on effective BOM cost analysis. Here’s a deep dive on how to calculate BOMs properly.

Ioana Neamt
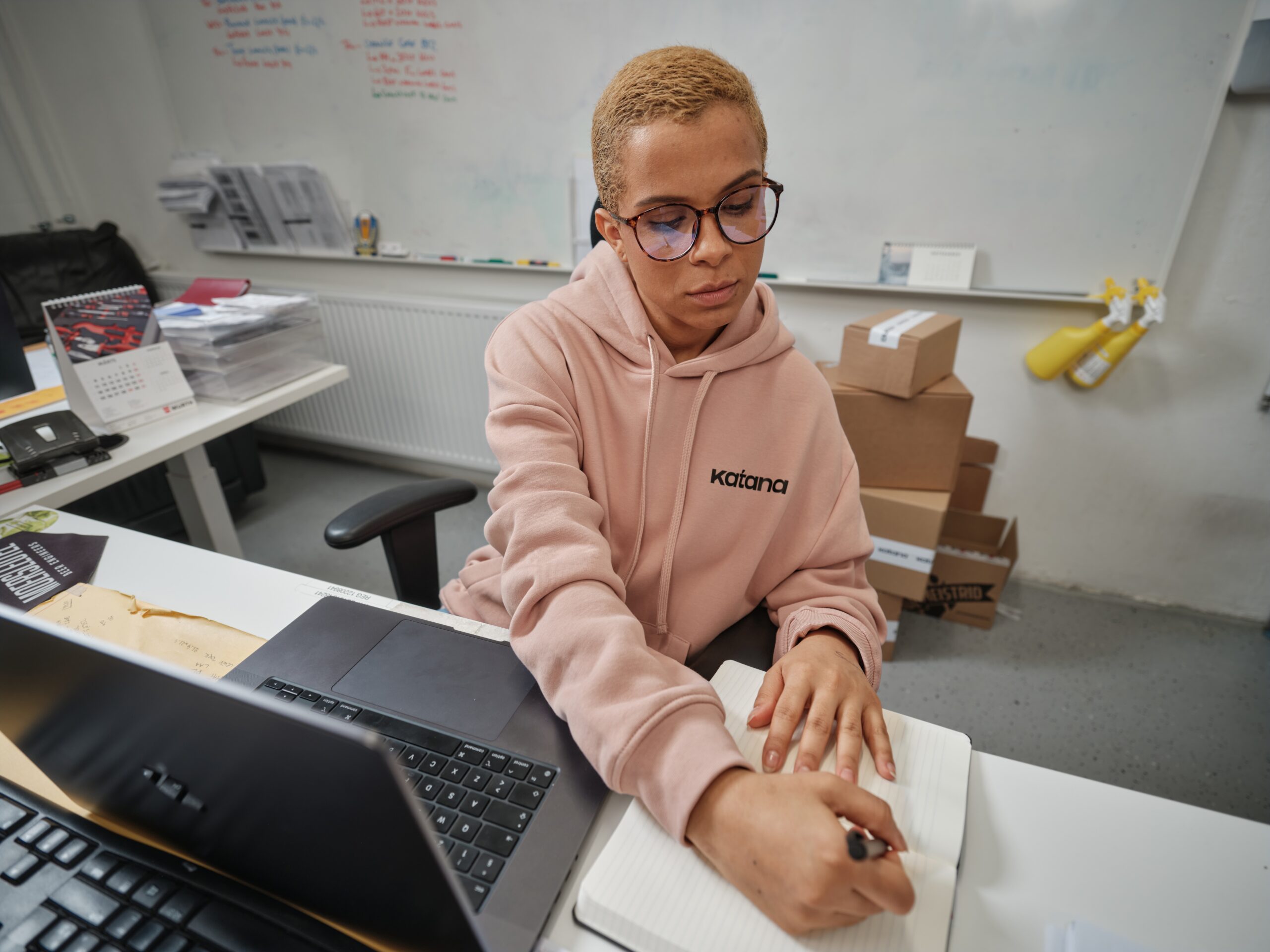
They always say, “Rome wasn’t built in a day.” Want to know the reason why? It’s because Romulus and Remus didn’t argue. Instead, they locked themselves away and figured out how to properly calculate their bill of materials (BOM) to build a branch of Starbucks near the Colosseum.
Friends, Romans, and Countrymen — order a Grande Latte with optional biscotti and settle down. We’ll explain how to figure out a BOM cost analysis and why it’s a non-negotiable stage in the manufacturing process.
The importance of BOM cost analysis
Manufacturing businesses must find innovative ways of optimizing production processes and reducing costs. All this has got to be done without any loss of quality. One of the key ways of achieving this is by looking at the bill of materials and analyzing its costs.
Wait. Before you dust off your abacus in a panic — it isn’t simply a case of looking at the figures. It’s also about examining the key insights that help drive manufacturing success. Later on, we’ll examine these. First, we’ll take a look at some of the challenges BOM management creates.
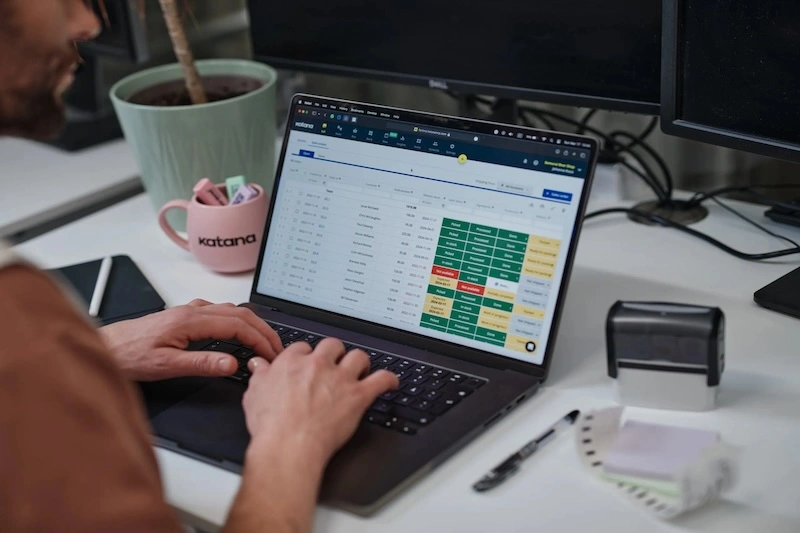
Challenges of traditional (manual) BOM management
When we consider the challenges of managing BOMs — especially in their traditional form, it raises a few issues.
The first is that it can be a time-consuming process. Manually entering and checking data can take up valuable manhours that are better used elsewhere.
Secondly, a result of spending so much time on traditional BOM management is that the analysis can be error-prone.
Finally, the configurable BOM can sometimes lack real-time insight. This means it can be difficult to assess what is working and what isn’t. It then makes it tricky to instigate effective changes to manufacturing processes.
The upshot of all this is that companies end up with:
- Inaccurate cost calculations
- Badly managed supply chains
- Lack of proper inventory management
- Delays in delivering the finished product
Not to be the bringer of even more bad tidings — please don’t spill your latte — but manual BOM management systems will struggle to keep up with certain industries. Especially those that move at a pace. Think about the IT industry, for instance, because pricing for components and the technologies themselves change so quickly.
This leads to a lack of agility, which ends up costing more money and causing production delays. A knock-on effect is that communications with suppliers, buyers, and other business stakeholders are affected, and information sharing slows down. This creates frustration for everyone.
OK, we’re done with the bad news now. Let’s look at ways to turn a situation like this around with consistent, effective BOM cost analysis strategies.
Free bill of materials template
Want to get started with your bill of materials calculations? Download this free template to get yourself on the right track.
How to calculate BOMs effectively
There are some great tips and techniques to calculate the cost of BOMs effectively, and we’ll look at some of the main methods now. Several factors come into play here:
- Complexity of product design — How difficult or complex is the product being manufactured? This will have a direct impact on how to calculate BOM. Manufacturing products with complicated designs, or that require complex parts need to be considered. They’ll often require more raw construction materials or hard-to-obtain components. This will require more labor.
- Selection of materials — The more specialized materials are needed, the higher the cost. In turn, this increases the price of the finished product. Companies, therefore, have got to be savvy when it comes to finding the right balance of materials, and how much they pay for them.
- Workforce efficiency — The productiveness of the workforce matters. Analyzing the skills they have, and how quickly they work will have an impact on how a BOM is calculated. The more efficient the labor, the quicker the product will reach the point of sale.
- How suppliers are chosen — Working with reliable suppliers who are cost-effective and know the product inside out is also a key factor when it comes to BOM costs. Finding suppliers who offer all the above and more will have a big impact on reducing overall costs.
- Financial factors — The cost of materials and production is affected by the overall economy and how markets are performing within the industry. Companies really need to get to grips with all the varying trends and fluctuations to get the perfect calculation for their BOM.
Phew. So that’s the five factors that can affect BOMs covered. Now, what we need to do is classify the three principles used to cost them:
- Standard costs
- Planned costs
- Fall back principle
Standard costs to calculate BOM
Standard costs are used in a bill of materials to work out the final cost of a manufactured item. The calculation is worked out via a few different sources. They include:
- A costing version, which has all the information about the item, and its indirect calculation formulas.
- Next, there are the cost records. This is when each purchased item has its own cost record — maintained in the costing version. It’ll have an effective date. The BOM calculation date will determine which of the cost records is used.
- Then there’s the cost group. This is assigned to a purchased item, and it assists in segmenting the costs in the final calculated BOM.
- Lastly, there’s the BOM calculation group. This contains the warning conditions that can flag up potential issues with costs that need to be dealt with.
Planned costs for BOM calculations
For planned costs, it’s a good idea to use a BOM calculation group to highlight the source of the cost contribution data for any of the components purchased.
- First things first, look at the cost price model as this highlights the source of the cost contribution data for all the raw materials and components that are bought.
- Secondly, there’s the sales price model. This shows how the data from the item will be used to formulate a suggested sale price.
- Finally, there’s the stop explosion. This indicates that the item that’s been manufactured needs to be treated as a purchased item for cost roll-up purposes.
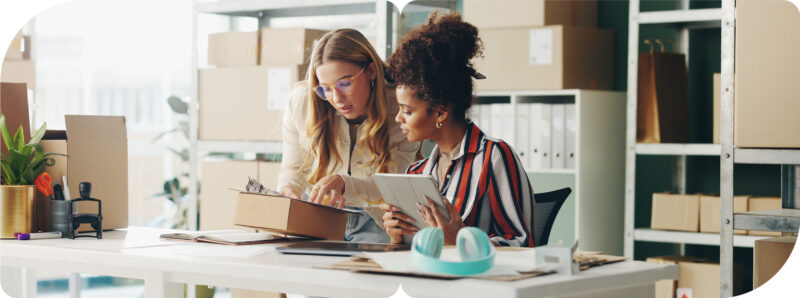
Fallback principles for BOM calculations
How do we incorporate the fallback principle into this? Let’s go.
- Fallback principle for standard costs — For standard costs, a costing version can contain incremental changes. These can be things like pending cost records that highlight new items or cost changes. Here, the fallback principle will identify the use of active standard costs contained in other costing versions.
- Fallback principle for planned costs — In terms of planned costs, they contain incremental changes for simulation purposes. This costing version includes pending cost records that simulate cost changes to items, cost categories, and calculation formulas for their indirect cost. Here, the fallback principle identifies the use of the active standard costs contained in other costing versions.
Calculate your BOMs with Katana
Getting the right manufacturing processes in place is key to a smooth production process.
The team at Katana knows this and we’re on hand to help take you through every stage.
Katana’s BOM software gives your manufacturing model a boost, but over time it can give your business a real market lead. It helps you manage your manufacturing operations, production schedules, and costs, in one intuitive platform.
Katana’s software makes a world of difference to every project you undertake. With real-time production planning and scheduling, busy businesses get the boost they need, so they can spend time on other tasks.
Let Katana take care of all your BOM needs. Contact us for a demo today. Scale up your business with our hassle-free solutions.
How to calculate BOM FAQs
BOMs are calculated by analyzing data from a wide range of sources. They’ll include various factors such as item information, costing formulas, and costing versions. Every BOM cost will be unique. It’ll always depend on the type of product that’s being manufactured and the industry it’s for.
Once a BOM is saved, it’s possible to estimate a final cost. This is done by adding up the total cost of the materials used. However, it can depend on whether or not specific production materials are in stock. If they are, then the cost will be worked out by using the weighted average cost. If any or all of the materials aren’t in stock, a simple estimated cost is used.
Companies need to streamline their processes as much as they can, especially in challenging economic times. Products must still be high quality but costs at a reduced level. A key way of reaching this goal is to put in place proper BOM cost analysis.
There are three main ways to calculate BOMs. These are standard costs, planned costs, and the fallback principle. The latter can be used in conjunction with either standard or planned costs. All of these depend on the type of product being manufactured, the components needed, and the skill level required to complete the work.

Ioana Neamt
Table of contents
bom-template
Get inventory trends, news, and tips every month
Get visibility over your sales and stock
Wave goodbye to uncertainty with Katana Cloud Inventory — AI-powered for total inventory control