Production management and operations management: key differences, tips, and solutions
Team Katana
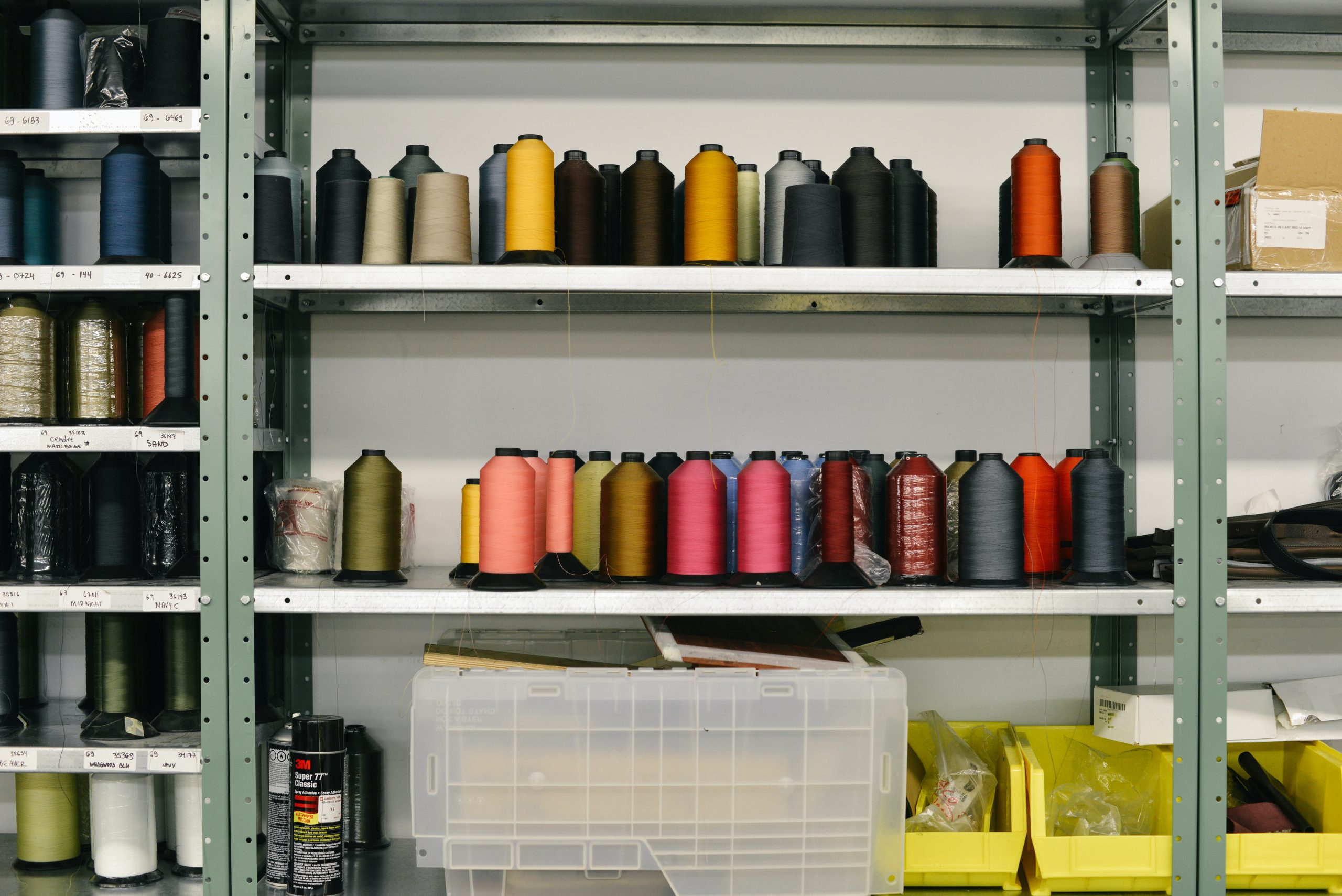
Perfecting your production management is essential for a successful manufacturing business.
Essentially, you can define your production management definition as an optimization problem. The ultimate objective of production management is to optimize your production line’s efficiency with your current resource capacity — manufacturers need production management.
In this article, we look into production management and operations management, focusing on why they are important, and how you can make them work for your business.
What is production management?
Production management, or operations management, focuses on achieving a smooth production process with efficient planning and control of business operations.
It has the ultimate objective of optimizing your manufacturing efficiency with your current capacity. To achieve this, you need to find the best manufacturing process for your business.
Repetitive manufacturing
This is a 24/7 production/assembly line, made possible with the use of manufacturing process automation such as conveyor belts and robotics.
Discrete manufacturing
This too relies on production lines. But the products that are produced by the manufacturer are varied, which requires the line to be set-up, and changed, depending on the products in production.
Job shop manufacturing
The humble manufacturer’s choice of manufacturing process management, which utilizes workshops and separate production areas to allow for bespoke products.
Batch manufacturing
Batch manufacturing allows manufacturers to make products in the necessary number of batches needed to satisfy customer demand.
Continuous manufacturing
Another manufacturing process that runs 24/7, although this process deals with raw materials such as gasses, liquids, powders, or slurries, including areas like mining, where the products can be more granule.
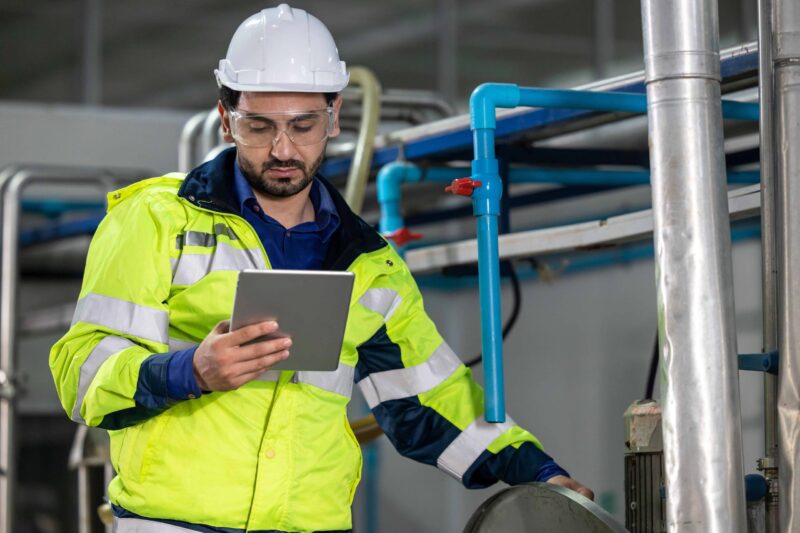
The functions of production management systems
Process operations are defined as a process of production management that includes any of the above workflows. Let’s look at the functions of production management in more detail.
Production control service
This is where you’ll monitor production to make sure everyone executes the correct plans in the manufacturing process. The purpose is to react quickly if things deviate from the plan and make sure everything runs smoothly.
Scheduling
This one is a critical function in any business. Production scheduling is when you plan when production will start and finish during a project run.
Cost and quality control
The aim of this is to produce the highest quality product at the lowest possible cost, not just by saving money for your business, but by offering your customers a fairer price, too. To maintain consistent quality, be sure to follow your production quality control checklist.
Maintenance of machines
Finally, you’ll want to make sure all your tools and machinery are spic-and-span to avoid them underperforming or breaking down and stopping production completely.
PRO TIP: Production management is going to be the most important aspect for manufacturers when looking to get more control over their business. But, with so many tasks and responsibilities, it can quickly become overwhelming. That’s why it’s essential to find production management software that can help you automate these tasks.
Implementing production management
When trying to achieve production and operations management, you’ll need to make decisions at three different stages:
1. Production planning
Essentially this will be your master production schedule. As the manager, you’ll need to decide where, when, and how production will start.
2. Production control service
This is where you’ll focus on quality, costs, and shop floor control.
3. Improving operations and productions management
The final stage of production management and operations is the development of more efficient methods of manufacturing the firm’s goods and services.
That’s a breakdown of what is production management and its definition, so let’s now move on to its counterpart, operations management.
What is operations management?
Operations management is pretty similar to production management. It is the day-to-day running of the business, ensuring operations and production are carried out efficiently and smoothly. This also includes handling administrative, factory-level, and service management.
The focus point of your operations management is the customer. If the customer is satisfied, then you’re heading in the right direction. However, how you handle your resources is also the function of operations management, since you want to be improving customer satisfaction with the least amount of wastage with the maximum utilization of resources. But what are the functions of operations management?
Strategy
From raw inventory management to routing manufacturing, under operations management, you’ll need to develop plans and tactics that will help you achieve lean inventory and a smooth production flow to get a competitive edge over your competitors.
Product design
Here is where you should investigate if your product caters to the needs of the customers and follows the market trend. Yes, your product may have survived the prototype stage, but people’s needs and wants change, and you need to be ready to adapt your product to those shifts in manufacturing trends and predictions.
Forecasting
Demand planning will allow you to understand how your product is performing in the marketplace, and decide on how to proceed, be that increasing, decreasing, or even stopping production on a product.
And that’s the ins and outs of operations management. As you can probably see, the difference between production management and operations management isn’t much. Regardless of if you struggle to set them apart or call it something else, here’s why it’s important to have your operations and production management down to a tee.
Want to see Katana in action?
Book a demo to get all your questions answered regarding Katana’s features, integrations, pricing, and more.
What’s the difference between production and operations management?
Production and operations management is an all-encompassing term that covers managing the manufacturing of your products and those finished goods and services.
You might be furrowing an eyebrow, “Aren’t those two technically different areas?” Traditionally speaking, a manufacturer would make its products and dispatch them to a third party, and that would be the end of it. But, as more businesses take more control over their company and brand, they’ve started to introduce services such as customization into their production.
And as we control more aspects of our business, we need to also balance production and operations management.
As manufacturers have drifted toward a direct-to-consumer brand, and even retailers now manufacture their own branded products, the line between production management and operations, products and services, has become increasingly blurred. Are you still confused? Production and operations management are very similar, but the main difference between the two is:
Production management — Monitoring and managing the manufacturing of products.
Operations management — The services which are on offer to the customer and the work that needs to be done to finish the production.
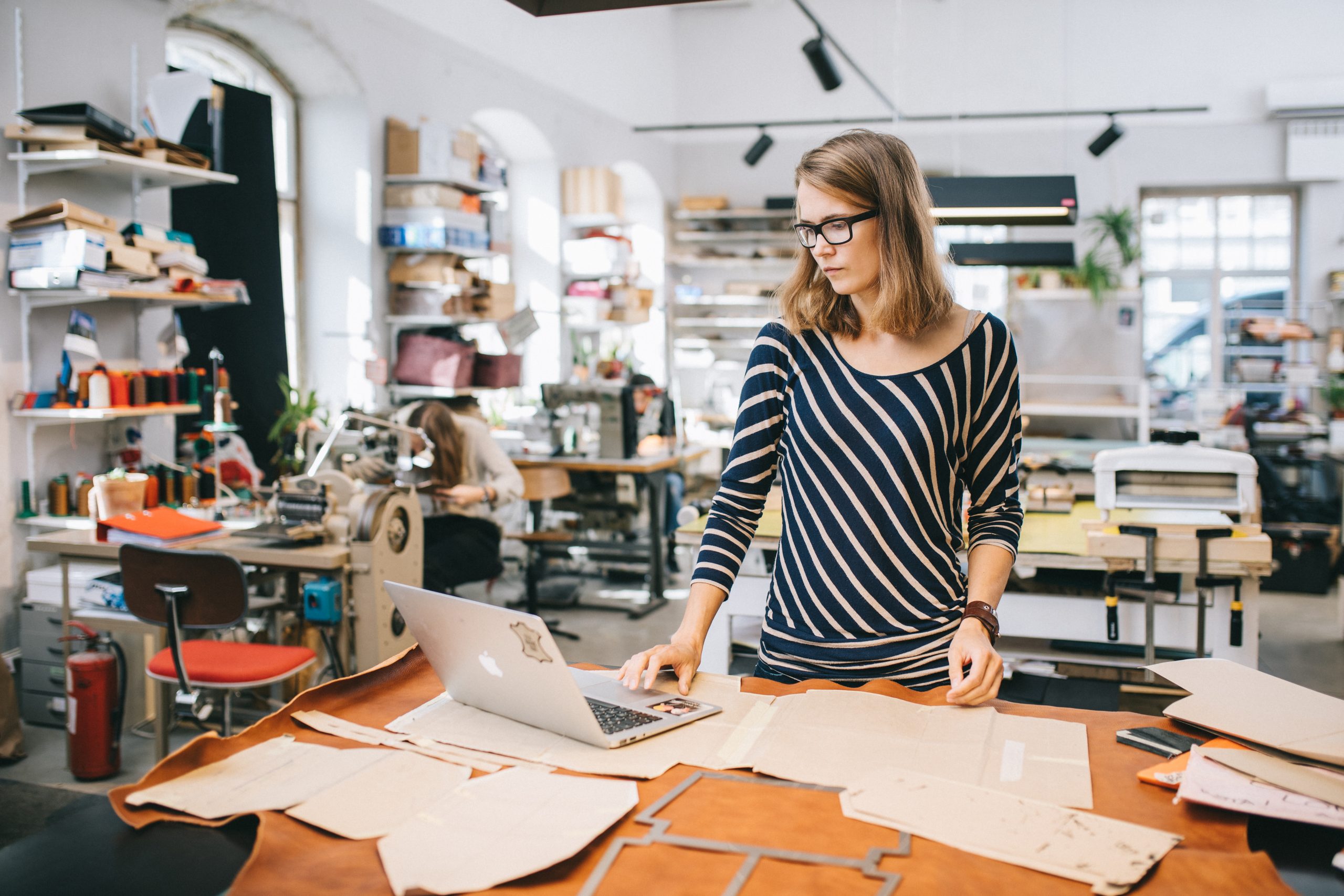
Why is production and operations management important?
Production management and operations management is not just recommended to improve some areas of your business, but it is essential. Otherwise, you could find your business struggling to meet orders and lose customers. So, as a manufacturer, by understanding operations management and the importance of production management, you can:
1. Accomplish business objectives
By performing your production and operations analysis, you’ll be able to achieve business objectives by efficiently producing goods and services that meet the needs of the customer. This will increase customer satisfaction, which, in turn, increases your sales and profit.
2. Boost brand image
Important for D2C manufacturers, with production and operations analysis, you’ll be able to raise your reputation as a business that delivers quality products and fair prices.
3. Reduce manufacturing costs
Essentially, the goal of a production management system is to achieve lean manufacturing. By optimizing your manufacturing output, you can expect to lower your manufacturing costs either by not having resources waiting idly by or figuring out the best way to keep inventory, such as using ABC inventory.
Now that we’ve tackled the subjects of production management, as well as operations management, it’s time to also take a look at material management, and what it’s all about. Think of it as the third piece of the puzzle we’re trying to put together here for you, to give you a better picture of how these processes intertwine and how they keep your operations moving forward.
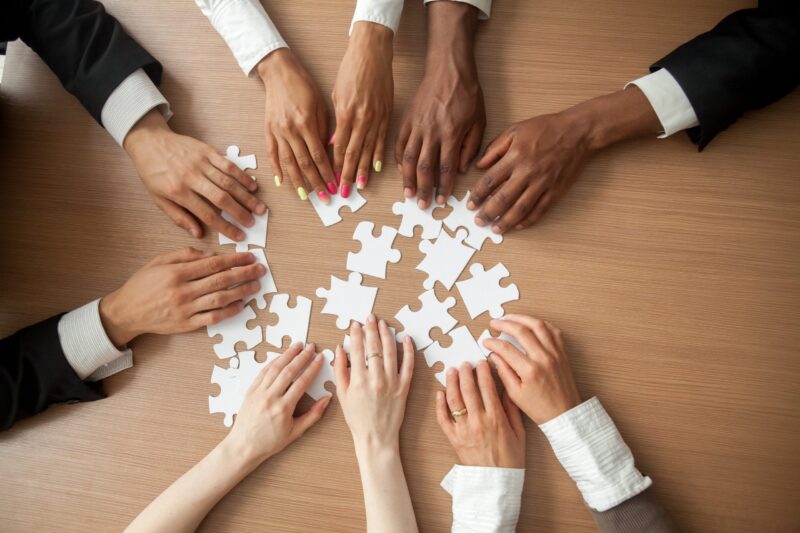
Automate your production management with Katana
Although it is possible to do your production management in a cumbersome spreadsheet, it’s not ideal since there’s so much you need to do, and you can’t afford to spend any time stuck doing mundane administrative tasks.
This is where automation comes into play. Katana’s cloud inventory software is an all-in-one platform that has been built for manufacturers looking to get more control over their production management and operations. Katana helps manufacturers by giving them the power of automation by:
- Scheduling production and calculating deadlines
- Planning and purchasing materials
- Tracking finished goods and raw materials in real-time and allocating them to sale orders and manufacturing orders
- Calculating manufacturing costs
Request a demo today and see for yourself how Katana can optimize your production and material management.
Team Katana
Table of contents
Get inventory trends, news, and tips every month
Get visibility over your sales and stock
Wave goodbye to uncertainty with Katana Cloud Inventory — AI-powered for total inventory control