Everything you need to know about cross-docking
Cross-docking involves the direct transfer of products from inbound to outbound transportation, bypassing traditional warehousing.

Ioana Neamt
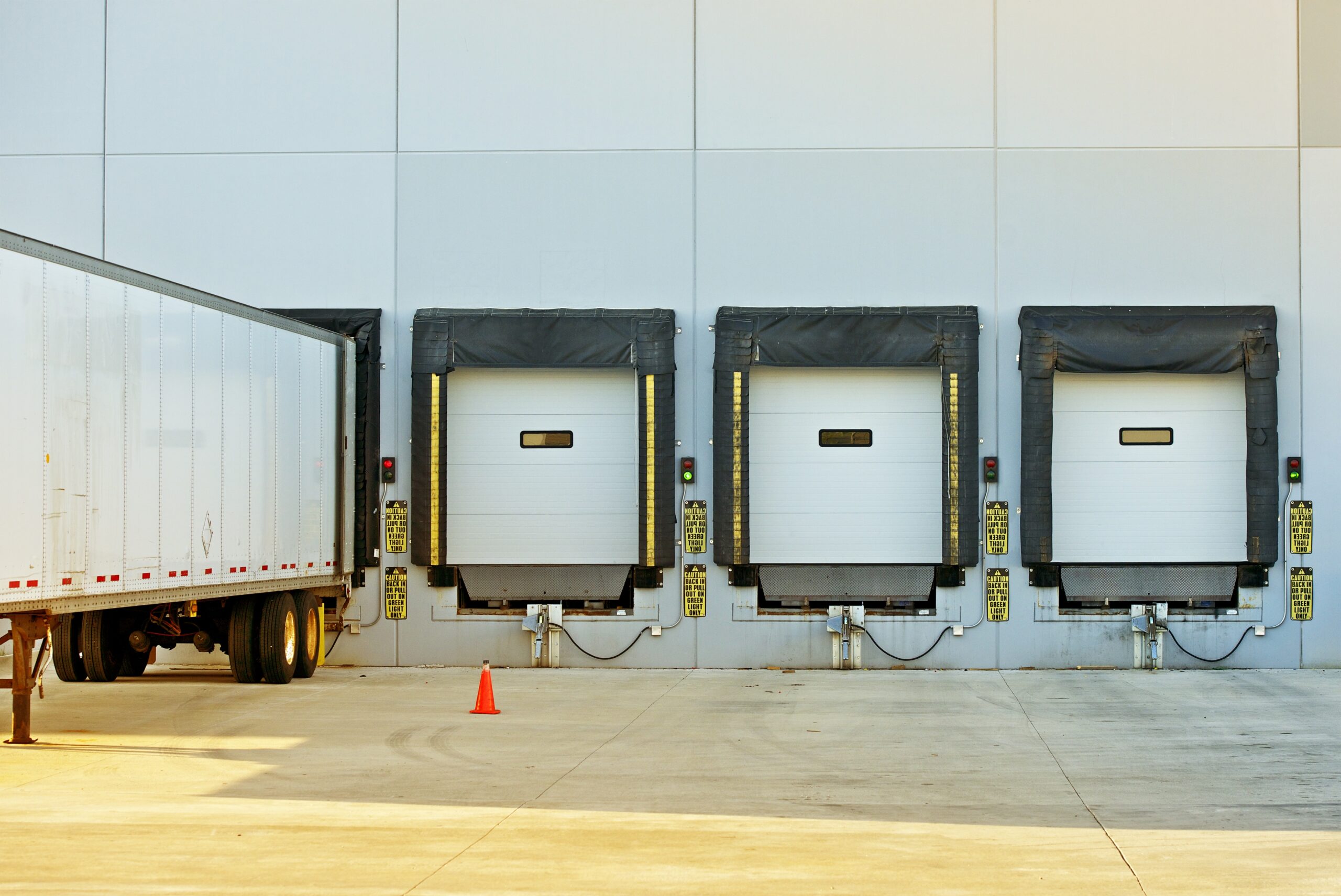
In the fast-moving world of supply chain management, efficiency and speed are paramount. One method that has gained significant traction for its ability to streamline operations is cross-docking. In this article, we’ll explore the essentials of cross-docking, detailing its benefits, challenges, and strategies for effective implementation. Let’s dive right in, shall we?
What is cross-docking, exactly?
At its core, cross-docking is a logistics strategy meant to expedite the distribution process. It involves the direct transfer of products from inbound to outbound transportation, bypassing traditional warehousing. Products are received at a docking terminal, quickly inspected and sorted, and then immediately loaded onto outbound vehicles for delivery. This method drastically reduces or even fully eliminates storage time, which benefits both businesses and customers, in a win-win situation.
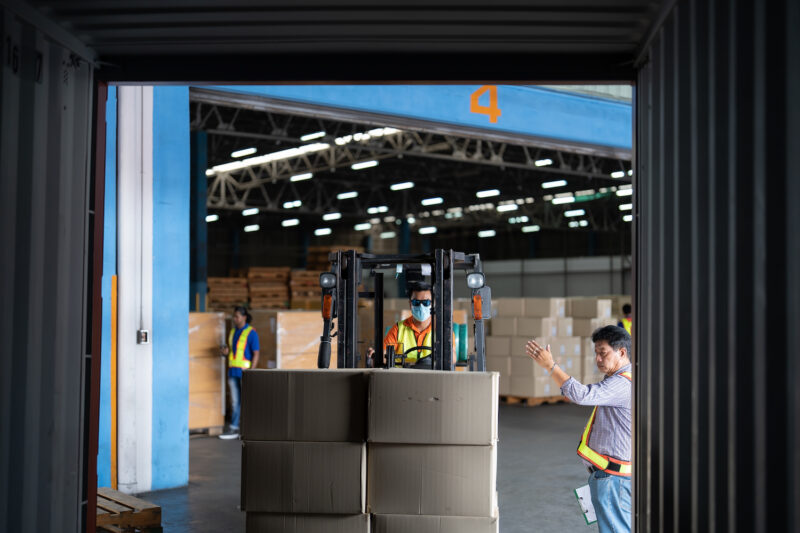
How does cross-docking work?
The cross-docking process begins once goods are received at a terminal or docking facility. Upon arrival, these goods are swiftly unloaded and subjected to a quality inspection to ensure they meet the required standards, and right after that, they are sorted according to their final destinations (don’t tell us you didn’t immediately think of that log truck in Final Destination 2).
Finally, the sorted goods are loaded onto outbound transportation vehicles — trucks, railcars, or other means — for immediate delivery to customers or retail locations. This seamless transition from inbound to outbound logistics minimizes handling and storage time, enhancing overall supply chain efficiency.
Types of cross-docking
Cross-docking is not a one-size-fits-all solution, unfortunately, but it can be adapted to fulfill different operational needs.
- Manufacturing cross-docking, for instance, combines various products required for the production process, delivering them just in time to the manufacturing site.
- Distributor cross-docking, on the other hand, involves consolidating products from multiple suppliers to be distributed to various customers or retail locations.
- Transportation cross-docking consolidates shipments from different suppliers intended for the same destination, optimizing the transportation process.
- Lastly, retail cross-docking involves sorting products according to customer demand and delivering them directly to retail stores, ensuring the timely availability of goods.

What are the key benefits of cross-docking?
One of the most compelling benefits of cross-docking lies in the reduction in inventory costs. By minimizing the need for warehousing, businesses can substantially cut down on storage expenses. This efficiency extends to the overall supply chain, speeding up the movement of goods and reducing delivery times. What’s more, business owners get to reduce warehouse management costs, as there’s no need to store, sort, or keep track of products while they’re in storage in real time.
Another clear advantage of cross-docking is faster shipping. Because goods move quickly from one vehicle to the other, the time it takes for them to reach their final destination is significantly shortened, resulting in satisfied customers.
Add to that the benefit of lowering shipping costs, since one truckload can transport multiple shipments at once, reducing the need for more vehicles required for distribution.
Last but not least, there is a reduced risk of products becoming damaged, spoiled, or obsolete as they sit around in a warehouse or storage facility. The more that a product is moved around, handled, and transported, the more chance of it becoming damaged in some way. There’s also a lowered risk of a product becoming spoiled, sitting in less-than-ideal conditions, or reaching its expiration date in storage.
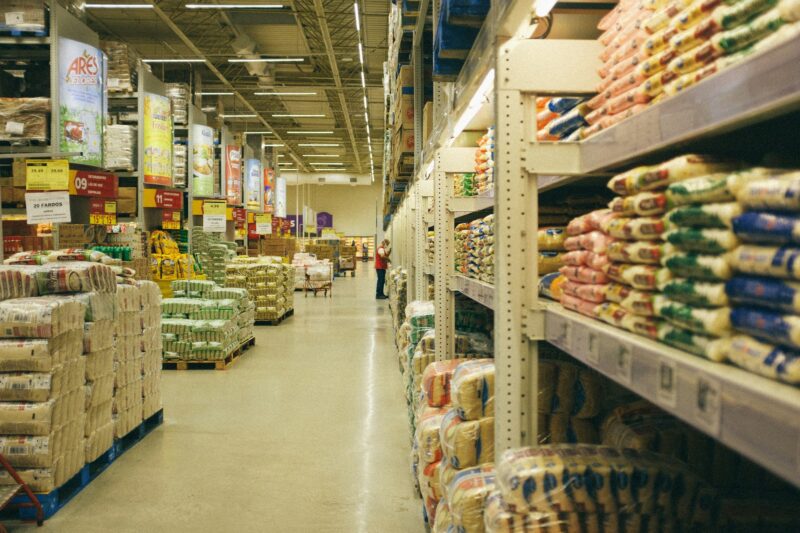
The challenges of cross-docking
Despite its many benefits, cross-docking is not without challenges.
First things first, implementing a cross-docking system requires a significant initial investment in infrastructure and technology. From vehicles to loading docks to specialized staff, there’s a long list of things that need to be set in place to ensure that cross-docking operations run smoothly and no errors emerge.
What’s more, advanced tracking and communication systems are essential to ensure smooth operations, which can be costly to set up. With products moving swiftly from one vehicle to another, there’s an increased risk of human error, product mishandling, or having the wrong products shipped to the wrong place.
Furthermore, the success of cross-docking heavily depends on the reliability of your suppliers, which is often something that’s hard to control. Any delays or inconsistencies in supply can disrupt the entire process and result in dissatisfied customers and disgruntled employees. Coordinating between various stakeholders, including suppliers, logistics providers, and customers, adds yet another layer of complexity.
Strategies for effective cross-docking
Alright, like Elvis used to say, ‘a little less conversation, a little more action, please.’ What does it take to ensure cross-docking operations run smoothly? Implementing cross-docking successfully requires a well-thought-out approach that integrates advanced technology, strategic partnerships, and continuous improvement. Let’s see some of the crucial steps required to make cross-docking a success for your business.
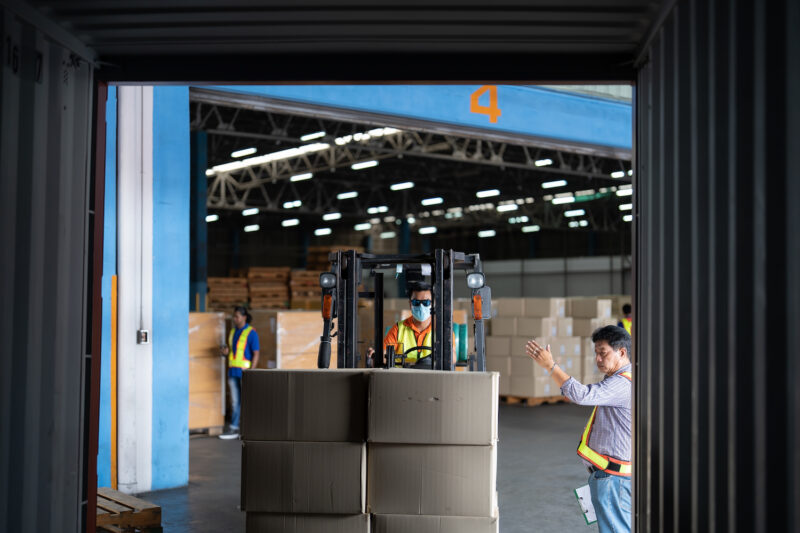
Investing in technology
One of the foundational strategies for successful cross-docking is investing in advanced technology. ERP, WMS, and transportation management systems (TMS) are critical tools that facilitate real-time tracking and efficient operations.
A robust WMS helps in managing inventory, optimizing warehouse layout, and coordinating the flow of goods. It ensures that products are accurately tracked from the moment they enter the docking terminal until they leave for delivery. TMS, on the other hand, optimizes the transportation process, ensuring that the right products are loaded onto the right vehicles and that routes are planned for maximum efficiency. Together, these systems enable seamless coordination and communication across the supply chain. Like yin and yang.
Building strong relationships with reliable partners
The success of cross-docking heavily depends on the reliability of suppliers and logistics providers. That’s why it’s crucial to build strong, collaborative relationships with these partners. Reliable suppliers ensure timely deliveries, which is essential for maintaining the tight schedules that cross-docking requires. Regular communication with suppliers about production schedules, delivery lead times, and potential issues can help in avoiding disruptions.
At the same time, partnering with dependable logistics providers who understand the intricacies of cross-docking can enhance the efficiency of the process. Establishing clear agreements and performance metrics can help in maintaining high standards and ensuring smooth operations.
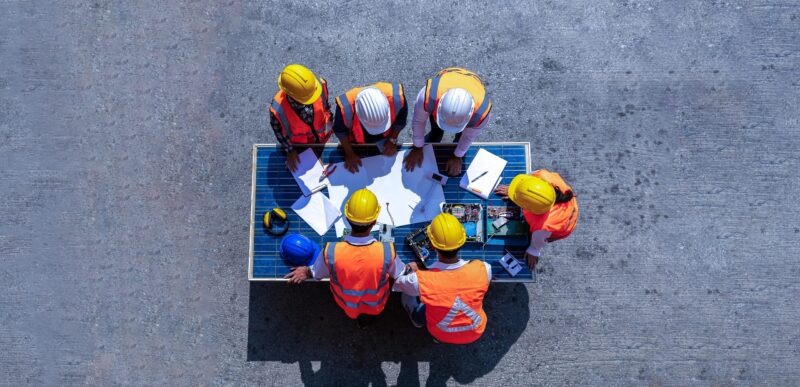
Optimizing dock layout
The physical layout of the docking area plays a significant role in the efficiency of cross-docking operations. An optimized dock layout minimizes handling time and maximizes throughput, which are your main goals. This involves designing the dock area to facilitate easy movement of goods from inbound to outbound areas. Clear signage, designated pathways, and strategically placed loading and unloading zones can reduce congestion and speed up the process. Additionally, using specialized equipment such as conveyor belts, forklifts, and automated guided vehicles (AGVs) can further streamline the movement of goods.
Comprehensive staff training
A well-trained workforce is essential for the smooth execution of cross-docking operations. Employees should be thoroughly trained in cross-docking procedures, including sorting, inspection, and loading techniques, to eliminate the possibility of human error as much as possible. Training should also cover safety protocols to prevent accidents and ensure a safe working environment. Needless to say, regular training sessions and updates on new technologies and procedures can keep the staff proficient, confident, and responsive to the demands of cross-docking.
Implementing pilot programs
Before scaling up to full implementation, it is wise to start with a pilot program, much like startup entrepreneurs launch an MVP, or minimum viable product, before a full product launch. A pilot program allows businesses to test the cross-docking process on a smaller scale, identify potential issues, and make necessary adjustments. This trial phase provides valuable insights into the operational dynamics and highlights areas that need improvement. By addressing these issues early on, businesses can ensure a smoother transition to full-scale cross-docking operations. The pilot program also serves as a training ground for staff, helping them get accustomed to the new processes.
Analyzing customer demand
Understanding and predicting customer demand is crucial for optimizing cross-docking operations. By leveraging data analytics, businesses can gain insights into customer buying patterns, seasonal trends, and product demand cycles. This information helps in aligning the cross-docking process with market demands, ensuring that the right products are available at the right time. Accurate demand forecasting reduces the risk of overstocking or stockouts, thereby enhancing customer satisfaction and reducing waste.
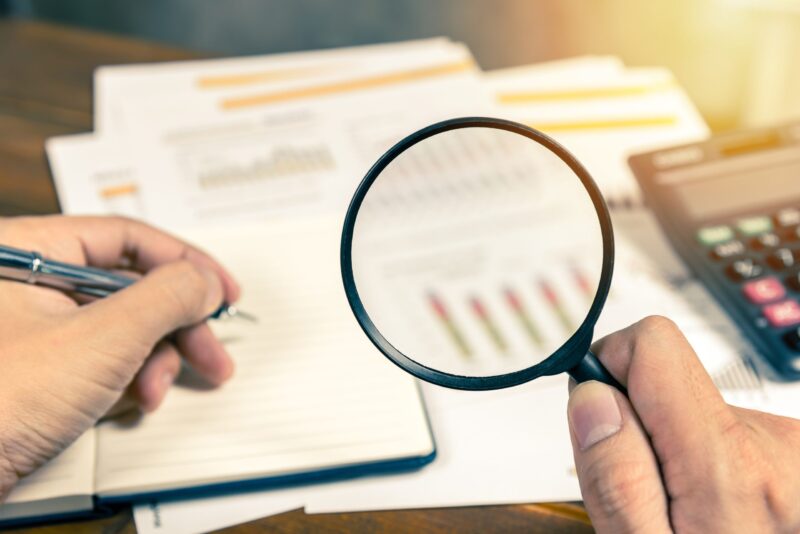
Power up your cross-docking capabilities with Katana
Implementing a top-tier inventory management system like Katana is essential for optimizing your supply chain efficiency. Katana offers real-time inventory tracking, ensuring complete transparency across every facet of your supply chain. This transparency empowers you to make informed decisions, preventing issues such as stockouts, delays, obsolete inventory, and customer dissatisfaction.
Moreover, Katana’s seamless integration with leading ecommerce platforms enables precise inventory tracking, improved order processing and management, and accurate forecasting of inventory demand fluctuations. Additionally, by streamlining your inventory processes, Katana significantly boosts your cross-docking operations, facilitating quicker and more efficient transfers of goods.
Get a demo to see Katana in action and discover more features!

Ioana Neamt
Table of contents
Get inventory trends, news, and tips every month
Get visibility over your sales and stock
Wave goodbye to uncertainty with Katana Cloud Inventory — AI-powered for total inventory control