Beginning inventory: Everything you need to know
Properly calculating the beginning inventory is crucial for accurate inventory management and just as accurate financial reporting. Mistakes can lead to overstocking or outages, potentially resulting in lost sales, increased storage expenses, and decreased profits. This article discusses how critical beginning inventory is for efficient inventory management.

Ioana Neamt
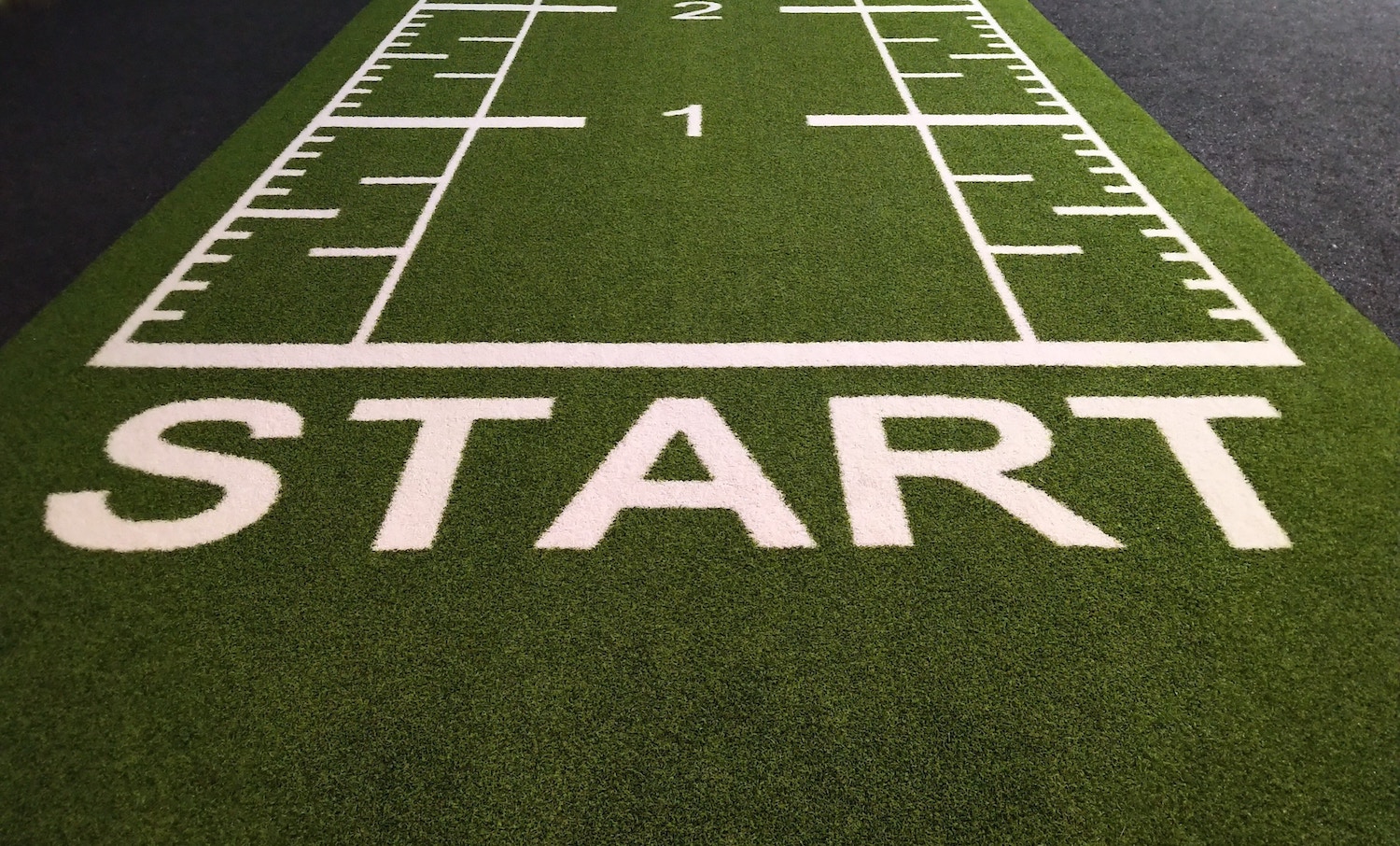
Do you remember, as a kid, the excitement of going to buy new school supplies at the start of the school year? And how quickly your parents used to remind you to consider the bunch of unused notebooks and pens from last year? That’s kind of what beginning inventory is.
Measuring inventory can be done at different stages of the accounting period. The main star of this article is the stock counted at the start of an accounting period, aka the beginning inventory.
Much like a student’s school supplies represent the base for their academic pursuits, beginning inventory forms the foundation of resources that a business holds at the start of its fiscal year.
But beginning inventory means so much more to a business or a company. It helps businesses balance inventory levels and ease the production and order processes. Not to mention, it can also lead to waste reduction.
What is beginning inventory?
Beginning inventory refers to the cost of inventory recorded in a company’s accounting books at the start of an accounting period. The key word is “start.”
Also known as opening inventory, beginning inventory refers to the total value of a business’ unsold inventory once a new accounting period begins. This includes everything from raw materials to assemblies to finished products not yet sold to customers.
At its most basic level, the beginning inventory is carried forward as the value of the ending inventory of the preceding period. But in the grand scheme of business things, beginning inventory plays a role in calculating average inventory and influencing overall performance measurements. It can also lead to a more efficient overall operation by overseeing stock levels and improving forecasting capabilities regarding when and what to order.
Miscalculating beginning inventory can lead to overstocking or stockouts. In turn, these lead to missed sales opportunities, increased storage expenses, and, you guessed it, profit reduction.
But fear not. Below, you can find a handy step-by-step guide to beginning inventory, formula and all.
How to calculate beginning inventory
Beginning inventory is the total value of stuff you have to sell at the beginning of a certain time period, like a month or a year. So, if you do the math right, it should match up with what you had left over from the previous time.
If you’re looking to find out how to calculate beginning inventory, look no further than the trusty beginning inventory formula. Although it can help make the process clear and easy, get ready for some math class flashbacks.
Calculating beginning inventory relies on several other calculations like cost of goods sold (COGS), ending inventory, and inventory purchases. Here is the formula to calculate the beginning inventory.
Beginning inventory = Cost of goods sold + ending inventory – cost of inventory purchases
After splashing water onto our faces and recovering from past math-related school trauma, let’s put the beginning inventory formula into words we can grasp.
- Determine the cost of goods sold — Use the accounting record from the previous accounting period
- Calculate production cost — Multiply your ending inventory balance by the production cost of each item, and then do the same for the amount of new inventory
- Add totals — Combine the ending inventory and cost of goods sold
- Subtract inventory purchased — To find out the beginning inventory
The good news? You don’t need to figure it all out on your own. To save time and make things easier, a beginning inventory calculator is the simpler way to go. By using a beginning inventory calculator, you’ll get fast answers in little time, without the need for hefty staff.
What’s the difference between beginning and ending inventory?
We now know that beginning inventory refers to the stuff that’s still in stock at the start of an accounting cycle. Ending inventory is its equivalent at the end of said accounting cycle.
In other words, ending inventory is the cost of the inventory recorded at the end of the previous accounting period. Notably, it carries over into the new period, which is where beginning inventory comes in.
Basically, each accounting period’s beginning inventory is the ending inventory of the previous period. This is why ending inventory is crucial in calculating beginning inventory.
State of Inventory Management — Access the full report
Download the full report based on data from real businesses using Katana to explore key trends and actionable insights that will help you navigate an uncertain 2024.
How to best manage beginning inventory with Katana
Getting a hang of and perfecting beginning inventory is crucial for efficient business operations. This is where Katana steps in.
Katana is the place for comprehensive insights into all aspects of the business. Not only can Katana help track inventory levels, but it can also predict future requirements. This leads to a more streamlined operation of your business. Katana is the all-in-one solution for all your inventory needs, from beginning (inventory) to end.
Want to see how Katana can streamline your business operations? Request a demo now.

Ioana Neamt
Table of contents
Get inventory trends, news, and tips every month
Get visibility over your sales and stock
Wave goodbye to uncertainty with Katana Cloud Inventory — AI-powered for total inventory control