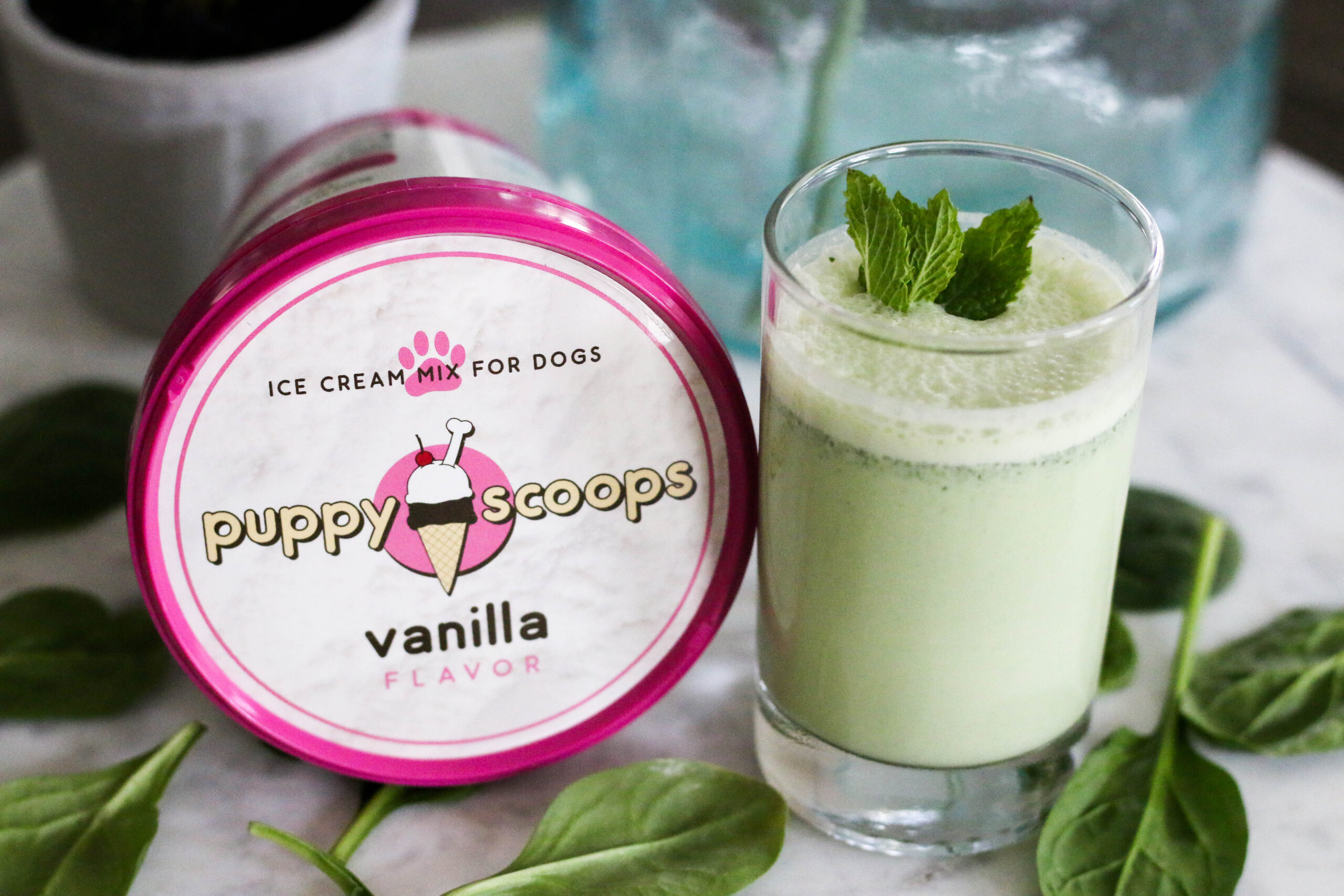
Puppy Cake has total control of their operations and inventory with Katana
Puppy Cake produces treats for your beloved pets for special occasions or just because you want to spoil them. According to Kelly, their biggest issue with manufacturing was forecasting ingredients purchasing and labor planning for several weeks out.
100%
Improve the efficiency of day-to-day operations
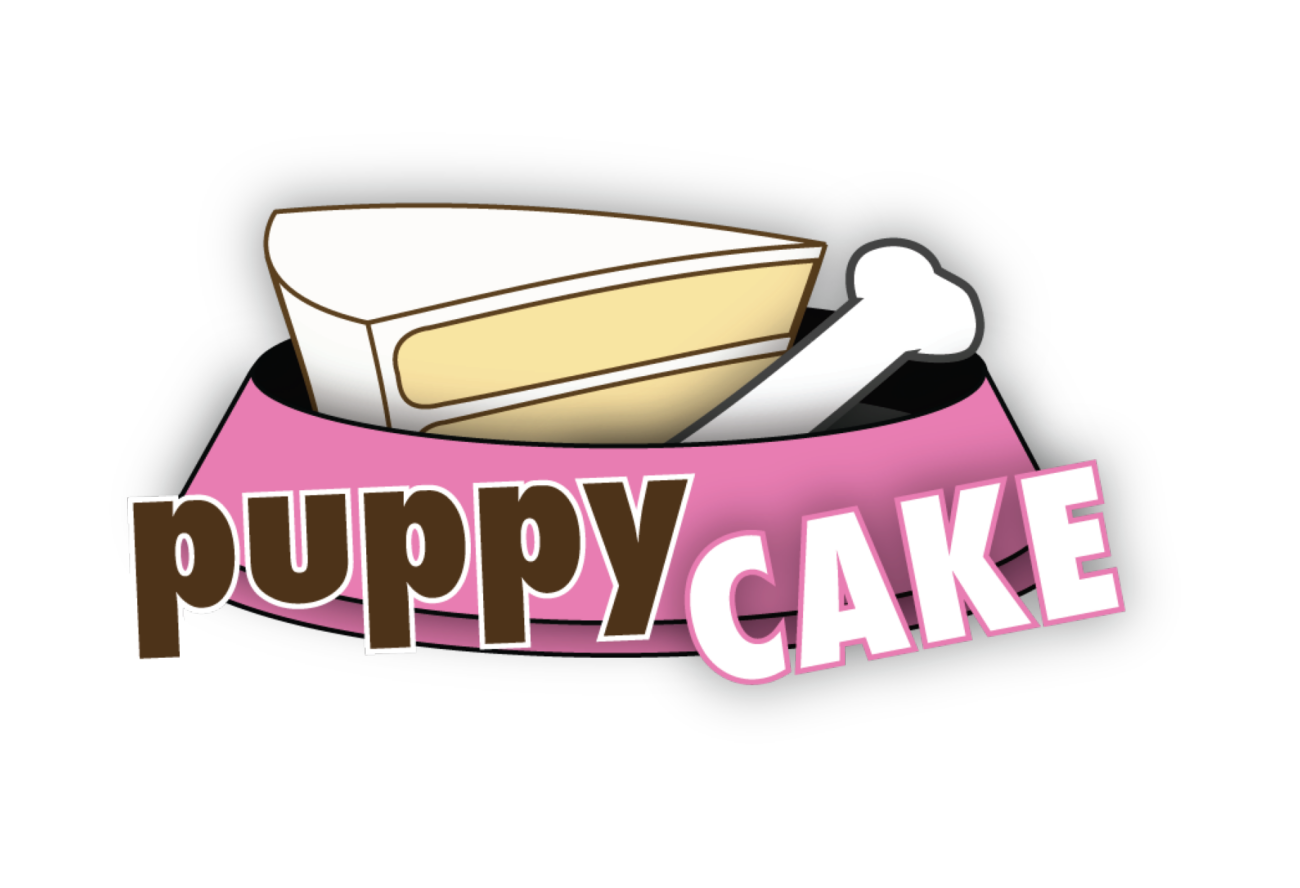
About Puppy Cake
Puppy Cake produces treats for your beloved pets for special occasions or just because you want to spoil them. No more feeling guilty eating dessert as your dog stares at you wanting something you can’t give them.
Puppy Cake is a company celebrating everything “doggo.” They sell everything from cooking ingredients, utensils, personalized cakes, and even clothes for humans and dogs alike.
They only use natural ingredients and hold themselves to the highest standard since they know how people’s pets are a part of the family. They even have a wheat-free alternative if you wish for if your dog to avoid certain food types.
Their products are all inspected by the PA Department of Agriculture.
Katana keeps accurate stock of our assemblies and ingredients so that I can plan out manufacturing and get instant feedback on whether or not I have enough resources in stock to complete an order.
Kelly Costello, Puppy Cake CEO
Challenges
According to Kelly, their biggest issue with manufacturing was forecasting ingredients purchasing and labor planning for several weeks out.
We struggled to figure out how many pounds of product we would need. We regularly ran out of ingredients or assemblies on a weekly basis because it was so difficult to plan it out.
Objectives
Puppy Cake quickly identified that they needed to get more control over their business, by:
- Improving the efficiency of their day-to-day operations by more than 75%
- Finding a new method of monitoring their material inventory management
- Developing, implementing, and improving scheduling to optimize production planning
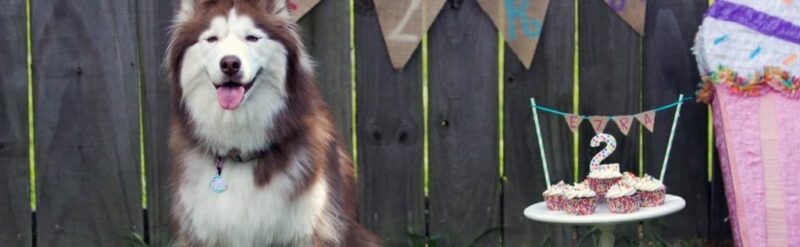
How Katana Helped
Puppy Cake was spoiling dogs with their treats. But they were struggling to achieve the perfect balance of inventory management, and their bottom-line was being affected by this.
That was until they found Katana. With Katana they have been able to:
- Improve the efficiency of day-to-day operations to 100%
- Get more control of their material inventory with our auto-booking feature
- Have a master production schedule with a clear overview of operations progress with a task list, so team members know what tasks are left to complete
We used Excel spreadsheets to attempt to keep stock of our ingredients and what was needed to accomplish different manufacturing processes. It was tedious and inaccurate.
Since abandoning the inefficient spreadsheets, Puppy Cake has been able to dramatically optimize their, operations, inventory control, and time management.
Katana’s auto-booking system allocates available material to the most recent manufacturing orders, so Puppy Cake can effortless see if they have enough resources to complete their operations.
However, if they wish to reprioritize the work order to finish an important order sooner, Katana’s nifty drag-and-drop feature means they can refocus their workflow. Katana will also redistribute allocated material to make sure the priority order is fulfilled first.
Katana’s visual and easy-to-use interface has allowed them to tighten up their control over their business. They have improved how they track material inventory and organize operations, helping them drastically reduce the number of production stoppages they were facing due to stock-outs.
More case studies
Get visibility over your sales and stock
Wave goodbye to uncertainty with Katana Cloud Inventory — AI-powered for total inventory control