What is a configurable BOM? All you need to know
Learn about the processes of creating bespoke configurable BOMs to improve workflows and get the most for your buyers.

Ioana Neamt
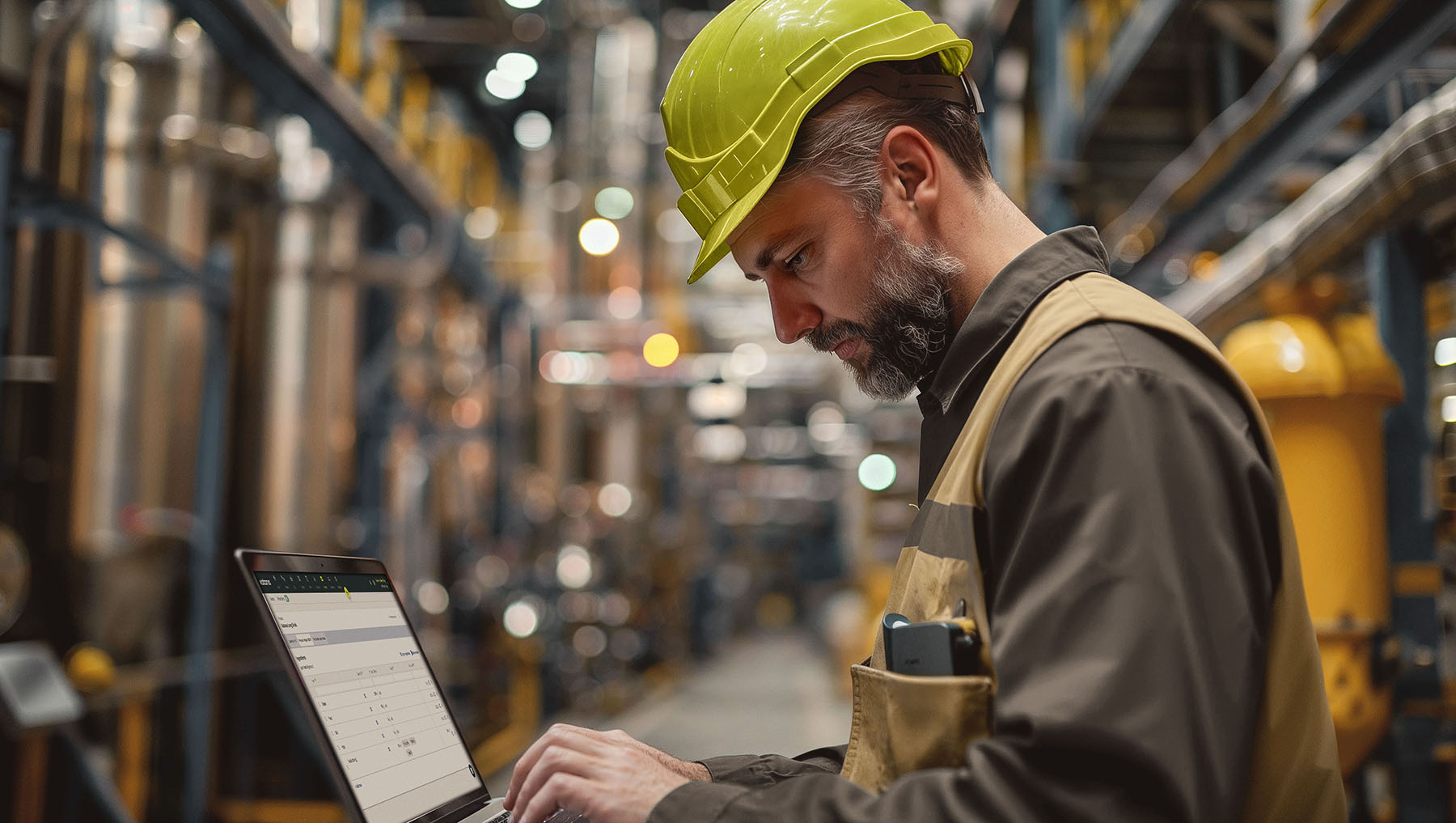
What is a configurable BOM, or CBOM? No, not the bodybuilder, he’s CBum. Sadly, neither is it the concealed weapon Inspector Gadget keeps in his trench coat to get him out of hilarious scrapes. It’s a bit more complex than that — and no catchy theme tune, either.
Here, we’ll explain configurable BOMs, and why they’re essential for any manufacturing business. But let’s first recap what a bill of materials (BOM) is in the first place.
What is a bill of materials (BOM)?
A bill of materials is a list of raw materials, components, parts, quantities, and just about anything else needed to manufacture a product.
One of the best ways to understand BOMs is to think about them as you would a cake recipe. They’re like a list of ingredients. When they come together with the right method, you get a perfect end product.
The problem with BOMs is that they’re a tad static and rigid. The business can’t adjust them if they want to for any reason. That’s why lots of manufacturers are now switching to CBOMs instead. Let’s talk about that.
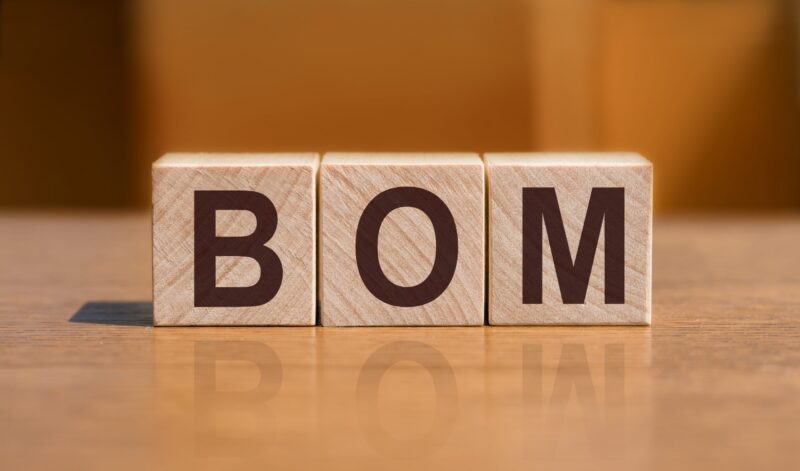
What is a configurable BOM?
Otherwise known as a CBOM, a configurable bill of materials is a customizable manufacturing tool. It allows the specific needs of buyers to be met when ordering products to be developed and made by a business.
CBOMs are used in a lot more industries than you might think. Any type of manufacturing situation that needs a degree of customization will use them. Think about things like medical devices, car parts, farm machinery, or even telecom systems.
Why does this matter? These days, everyone wants personalized service. A CBOM makes sure a customer can get exactly what they want every single time. Aside from that, it also helps the business understand exactly what they need to do to create the perfect custom product.
CBOMs are also essential for safety in manufacturing. A chocolate cake recipe without sugar or cocoa is a sad disappointment. But it’s not the end of the world. However, if we apply the same rule in manufacturing terms, a car brake assembly line with the wrong components for a customer’s use case puts lives in danger.
That’s why it’s so important to make sure our CBOM is correct. With proper CBOM processes in place, risks are mitigated and production processes streamlined.
CBOMs have a few other names. To paraphrase Troy McClure, “You might recognize them from such manufacturing acronyms as:”
- Variable BOM
- Dynamic BOM
- Modular BOM
- Adaptive BOM
They all refer to the same thing, though for this article, we’ll use CBOM or configurable BOM to keep things easy.
Download a free BOM template
If you need something to get you started, try out this free bill of materials template.
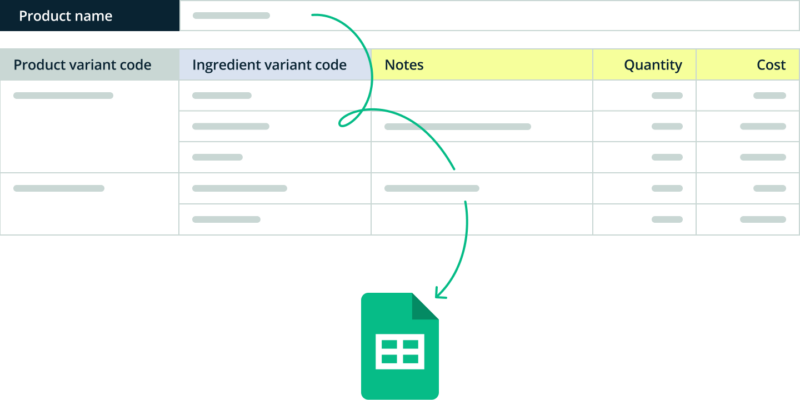
The challenges of configurable BOMs
Let’s get straight into the nitty-gritty. What are the challenges created by configurable BOMs?
Firstly, there can be size issues. Sometimes they become very large, with hundreds or thousands of items. This can make them difficult to manage consistently or get a solid overview of everything that’s happening within each process.
Secondly, customization can be a problem. It’s a great function to have for most things. However, in some instances, the sheer amount of custom options and selection conditions for CBOM items makes them unwieldy.
Third is a matter of time. There are some situations when creating a 100% BOM for a specific customer request or product configuration can take too long because of its size or the number of actions that need to be checked.
Finally, there can be problems when CBOMs are exported from one system to another, such as Excel (Microsoft’s Hall of Tortured Souls existed for a reason). This can cause issues with formatting, data consistency, and sometimes even loss of data. Not ideal.
Use cases for configurable BOMs
OK, so those are the challenges out of the way. Ready to explore how and why configurable BOMs are used? Let’s get positive.
They can be used to manage the manufacturing of complex products that have or require any of the following:
- Long lead times
- Mass customization
- Complex supply chains
CBOMs mean manufacturers can make exact specifications with specific instructions so that the right materials are used for a customized product. This helps reduce the risk of errors and improves efficiency as tasks can be automated.
Buyers can get a lot out of utilizing CBOMs, too, because manufacturers can offer a much greater variety of customization options. These can greatly improve the looks and performance of specific products and add value and interest, which adds to visual appeal when selling and marketing.
As if all that wasn’t great enough, they can be quickly and easily changed and updated when required, throughout the production process.
They’re also easy to link to other systems to help with bill of materials inventory management and assist with enterprise resource planning (ERP) or supply chain management (SCM) systems.
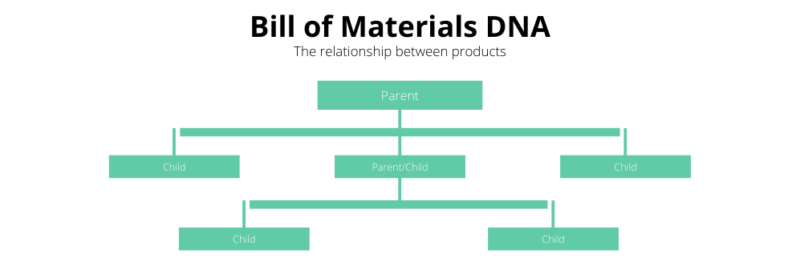
How to create a configurable BOM
Every manufacturer and product will have different needs when it comes to creating their configurable BOM management systems, but there are some simple guidelines to follow that make it easy to understand. We’ve broken this down into five sections:
- Define components
Start by looking at all the materials and components the product needs and work out the tech specs or industry standards that have to be met to ensure safety.
- Rules and dependencies
Next, define how these different materials and components can be included (or excluded) in a configurable BOM management system depending on the buyer’s request.
- Link with systems
It’s time to put our slightly larger nerd spectacles on. This is where the configurable BOM is then linked to either a product configurator, front-end system, or bill of materials software, and also to the ERP system, to keep everything from SCM to product lifecycle monitored accurately.
- Test and refine
We’re on the home stretch. The last step is to test, check, and refine the configurable BOM management system. Continuous monitoring is advised throughout the lifecycle of the CBOM, to make sure it’s working accurately and meeting the needs of the manufacturer and the buyer.
- Train teams
Finally, the relevant teams and workers must be trained on how to use the system.
Real-time BOM software
If you’ve grown out of Excel spreadsheets and need BOM management software that can scale with your business, book a demo and see how Katana can help.
Tips and best practices for configurable BOMs
It’s all well and good getting the CBOM set up, but it’ll only work well if it’s managed consistently and maintained with the correct information. You might be wondering how to do it.
Keep up-to-date records — Much like our cake analogy earlier on, it’s important to make sure your information (recipe) is always correct to ensure a 100% accurate end product. Consistently verifying the availability and specifications of components and materials is essential. As is making sure engineering rules and dependencies in the configurable BOM are correct. All this reduces the risk of errors and means buyers will be happy with what they get when they receive their product.
Systems for changes and updates — It’s imperative to have a system in place to manage any updates or changes to your configurable BOM. This means production will stay on track, without disruption. Changes need to be consistently communicated to teams and departments across the board, so they’re aware and can alter their working processes accordingly.
Ensure there’s a centralized system — Everyone needs to sing from the same hymn sheet. That’s why using a centralized system for configurable BOM management is another key best practice. When everyone has access to the same information and works from the same data, there’s less room for error.
Link up with other systems — While there’s a need for a centralized, configurable BOM management system, it should also link up with other software such as SCM and ERP systems. This helps manufacturers to track and manage inventory levels more effectively throughout a project.
Performance monitoring — How’s the CBOM performing? Without regular monitoring and optimization, you won’t know. Analyzing data on the components and materials used and, checking for inefficient production processes is essential. Continuous monitoring and optimization alongside implementing improvements mean that product manufacturers can assess whether their processes are meeting business needs efficiently.
Train relevant teams and departments — We touched on this a little earlier, but training for team members on how to effectively use configurable BOMs is important. Whether it’s showing sales departments how to manage a sales order, or training production and supply chain teams on how to effectively manage a production process. Proper training ensures consistent use of BOMs and reduces work errors.
Keep in touch with suppliers and buyers — Throughout the collaboration process with your buyers, keep in touch to ensure that they’re happy with everything. Ensuring no tweaks need to be made to the processes means that the configurable BOM can be kept accurate and up-to-date. Do the same with suppliers to make sure all the right materials and components are available. This will help improve the accuracy and efficiency of the configurable BOM. Holding joined-up conversations between all entities adds an extra layer of efficacy to CBOM management.
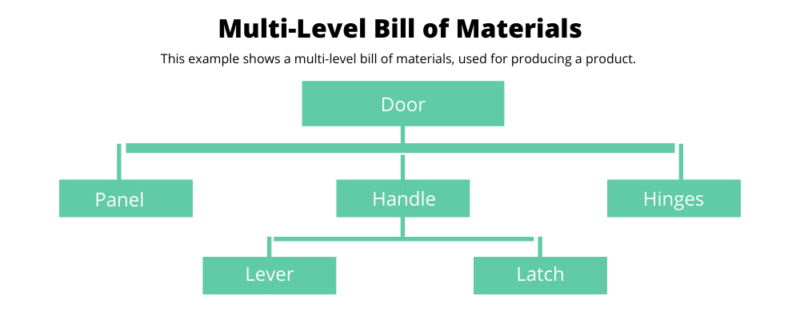
Katana’s BOM management software will streamline your processes
Implementing the most efficient manufacturing processes takes time and effort. Katana understands this and is here to help.
Our BOM software can truly offer you a competitive edge, with an array of tools that make the most of your manufacturing power and drive more business to your door. It helps you achieve complete control over your product composition to ensure accurate BOM management and safeguard product ownership, even as your business scales.
Katana offers real-time master production planning, production scheduling, and raw materials management that delivers results.
Ready to craft your own winning strategy? Get in touch today for a Katana demo. Together we can make your business grow.
Configurable BOM FAQs
It’s the Sunday name for a configurable bill of materials. It’s a customizable manufacturing tool that allows the needs of buyers to be met when they order products to be developed and made by manufacturers.
Configurable BOMs are needed to manage and produce products that potentially have a range of issues such as complex customization, long lead times, or come with complex supply chains.
They’re a great tool for manufacturers to use so that they can specify the exact materials and components that are required for a fully customized product. They effectively reduce errors in the manufacturing process, too.
Used across a wide range of industries and sectors from automotive through to medical and telecoms companies, they’re a versatile and adaptable system offering a huge variety of benefits to anyone manufacturing products to scale.
Yes. CBOMs mean that manufacturers can accommodate different configurations and options within the same product lines, without creating separate lists for each variant.

Ioana Neamt
Table of contents
bom-template
Get inventory trends, news, and tips every month
Get visibility over your sales and stock
Wave goodbye to uncertainty with Katana Cloud Inventory — AI-powered for total inventory control