The importance of BOM in material requirements planning (MRP)

Ioana Neamt
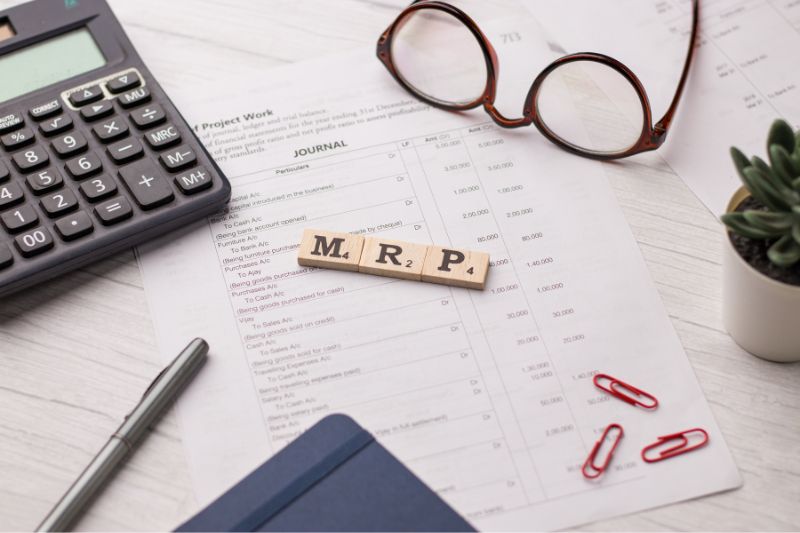
Manufacturing is in itself an intricate dance of multiple parts that keep each other in motion. Bill of materials (BOM) and material requirements planning are just two of the essential elements that work together to support other systems forward.
If you think about it like throwing a party, you can easily draw parallels between the organizing principles that make both happen. You need to know what each person requires, where best to source it, and in what order everything needs to be served (BOM). Based on that information, you can calculate the total amount of what is needed for the event, how much goes straight out vs how much is in storage until later.
What is a bill of materials?
One of the most important tools for any manufacturing business, the BOM is a highly strategic instrument that is well worth mastering. From bowling pins to laptops and beyond, pretty much everything we manufacture has a bill of materials “attached.” This documentation specifies every component that goes into a product, as well as how many of each element or what volume or weight.
What’s more, the same blueprint specifies the order and the way in which they all come together to form the finished product. See our deep dive into bill of materials if you want a detailed take on how to create one, what different types of BOM there are, the many purposes it can serve, and more.
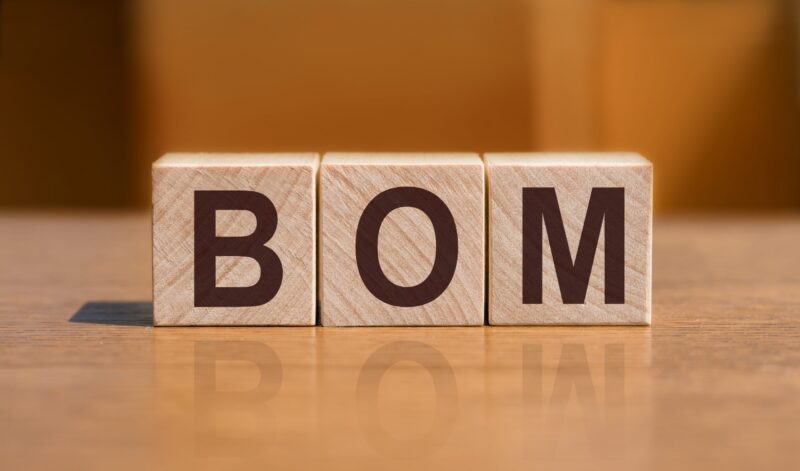
What is material requirements planning?
Material requirements planning, or MRP for short, refers to a system for production planning and inventory control that enables you to determine the number of purchases required to meet production needs, as well as the optimal timing for these purchases to be made.
It’s important to note that it should not be confused with manufacturing resource planning, which is generally abbreviated as MRP (II) or referred to as enterprise resource planning (ERP).
MRP I vs MRP II
For clarity, material requirements planning is the MRP I, and it is a tool used to calculate material costs, material availability, expected demand, forecasted demand, staffing ability, and machinery capacity.
MRP II, meanwhile, is an improved version of that system that builds on the initial set of features and expands functionality. A manufacturing resource planning system also enables advanced demand forecasting, machinery capacity scheduling, quality assurance, and general accounting. Take the time to find out more about the complexities of both in our detailed MRP system guide.
The benefits of BOM in MRP I
Bill of materials and material requirements planning are quite closely interconnected — the first clue is that materials are a key element even in their names. Let’s delve into why they are essential to each other and the ways in which their connection can support the success of your business.
We understand that the bill of materials provides, in great detail, a list of all the components, assemblies, and subassemblies that are required to manufacture a given product.
MRP uses this data to establish how much of everything is necessary in order to meet production needs, as well as when and where exactly they are needed.
Think of the BOM as the recipe for one cupcake that the MRP uses to determine what, when, and where is needed to meet the production needs of 30 cupcakes that you promised to bring to Friendsgiving.
Whether your manufacturing business is big or small, both these tools and the connection between them are essential for accurate planning, improved inventory management, reduced costs, and enhanced production efficiency.
Bill of materials template
Download this free bill of materials template and get your product composition under control.
Let’s look at their interdependence step by step:
- You follow the best practices of creating a BOM and put together the blueprint for your product.
- The MRP system then uses the BOM data to determine the number of components and the quantities of each that are needed for each product.
- Next comes production planning. The MRP system creates a production schedule based on inventory levels and demand forecasts.
- The MRP system then calculates the total component requirements adapted to the planned production schedule that was created using the BOM information.
- Inventory check is the next important step. MRP compares the calculated material requirements to current inventory levels to identify any possible shortages.
- If there are any shortages detected, the MRP generates purchase orders for the components that are not available in sufficient supply. These purchase orders specify the quantity, supplier, and delivery date when they are needed.
With BOM and MRP working in tandem, you can optimize both production planning and inventory management to avoid stockouts, delays, or any other issues that might hold back your activity.
Enhance your planning, scheduling, and production with Katana
In this day and age and at the pace that the industry is evolving, you quickly reach a point where Excel simply isn’t enough for the complexity and speed your business needs to operate. Bill of materials software and material planning systems are essentials, and it is never too early to adopt them.
Solutions like the Katana cloud-based enterprise resource planning offer features like bill of materials and inventory management that seamlessly work together to empower you to manage production, procurement, costing, and much more. Katana makes business easier by connecting everything you need and making it conveniently available to you in one place.
Here are just a few benefits that Katana brings to your fingertips:
- Automated manufacturing cost calculations based on your bill of materials and production
- Production prioritization based on the availability of materials
- Optimal inventory levels are maintained at all times
- Live data for accurate manufacturing, lead times, and purchasing decisions
- Manufacturing cost tracking based on your bill of materials and production
- The possibility of creating multilevel BOMs for accurate costing
- Automated inventory transactions and reorder points to prevent stockouts
- Product variance and materials management
Reach out for a demo to see Katana in action and understand all the ways in which it can boost the efficiency and margins of your business.
FAQs
MRP mainly stands for material requirements Planning, and it is essential to make sure you have the right stuff, at the right time, to make the things that you plan on selling. MRP works with your bill of materials data to automatically calculate everything you should have prepared and ready to go into manufacturing.
BOM and MRP are different, but they must work together, much like puzzle pieces, to achieve the bigger goal. The BOM, or bill of materials, establishes in great detail everything that goes into making any individual product. The MRP, or material requirements planning, handles the bigger calculations of what and when is needed to make any given quantity of that same product.
Although very closely related, MRP (material requirements planning) and MPS (master production schedule) are not one and the same. While both enable complex planning, MRP operates more on a granular level and serves to support MPS, along with other elements.

Ioana Neamt
Table of contents
bom-template
Get inventory trends, news, and tips every month
Get visibility over your sales and stock
Wave goodbye to uncertainty with Katana Cloud Inventory — AI-powered for total inventory control