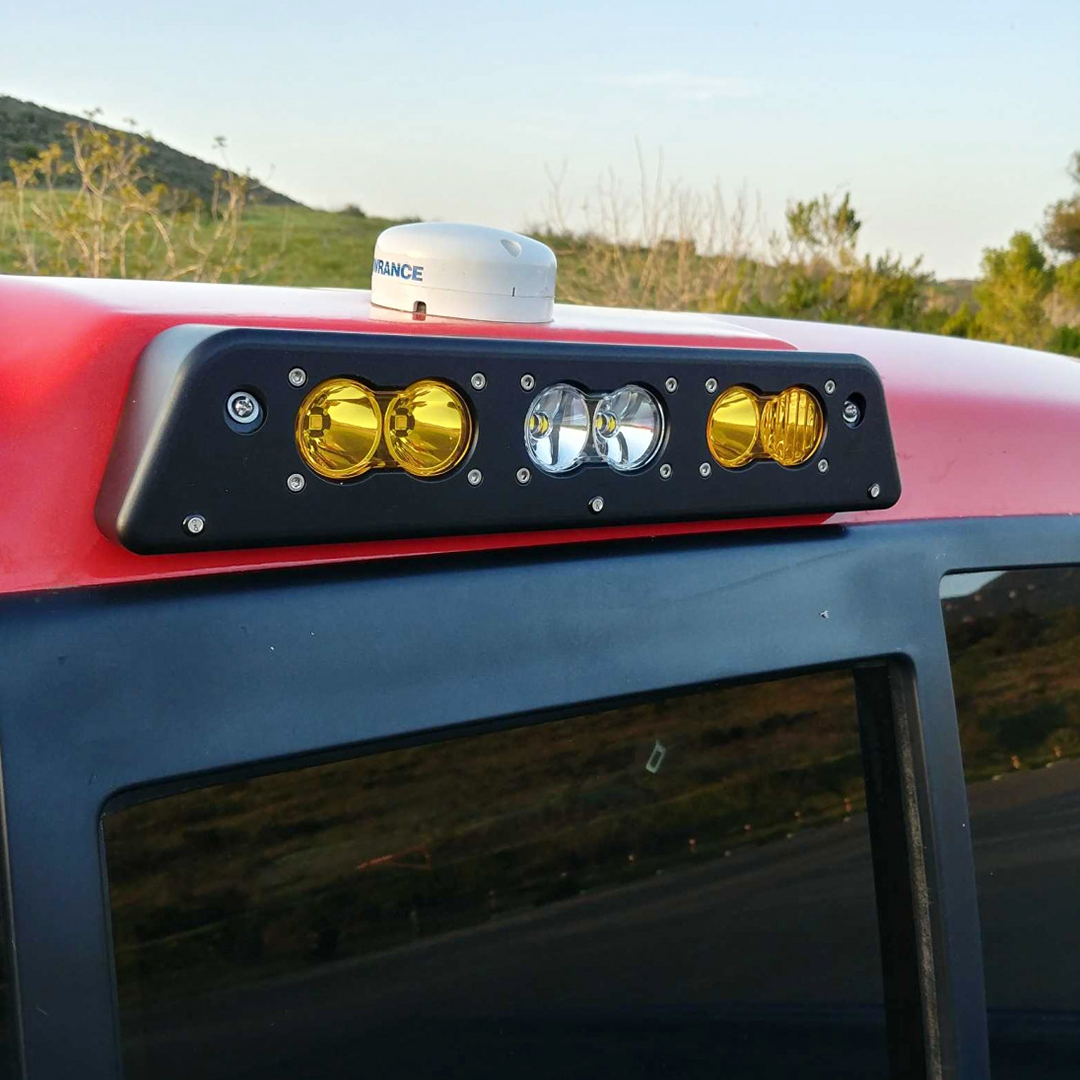
How GJ Motorsports cut 4 hours of admin time with automation
GJ Motorsports used Katana to optimize and simplify its manufacturing workflow, meaning less human intervention, hours saved weekly, and more space for the business to grow.
-4 hours
weekly manual updates
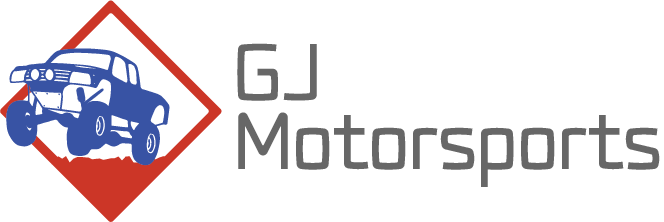
Website
Integrations
OpenCart, ShipStation, Easy Insight
Industry
Automotive
Location
Chicago, USA
About GJ Motorsports
GJ Motorsports is a Chicago-based aftermarket automotive parts manufacturer making accessories, primarily for pickup trucks. They make lighting products in their manufacturing facility where the main machining process occurs, while a few operations, such as anodizing and powder coating, and materials, are outsourced. In Katana, Thomas has 222 products and 120 materials, of which around 60 are sellable materials, and the rest are used for sub-assemblies.
Thomas spends his days in the office, doing most of the design, sourcing, and procurement work. He also does a lot of work in Katana, dealing with order management, customer service, accounting, and more. His background is in software development, so he’s used his knowledge and skills to automate many workflows and ended up saving two full workdays every month by not having to do admin work.
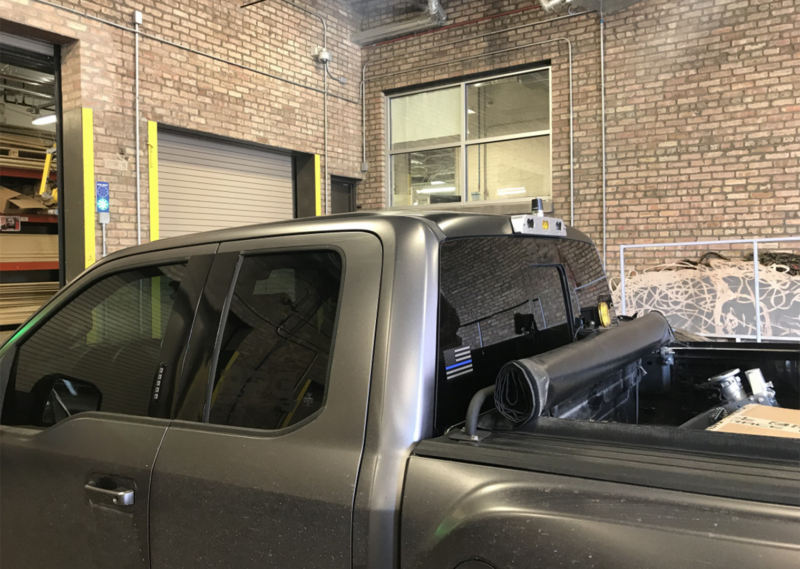
GJ Motorsports employs make-to-stock batch manufacturing and has an equal rate of B2B and B2C sales. GJ Motorsports also has one shop floor worker who takes care of the assembly, manufacturing, and shipping processes. They use Katana, OpenCart ecommerce platform, and ShipStation for perfectly automated processes.
Struggling with material stockouts and order delays
Before Katana, GJ Motorsports had a setup involving OpenCart and UPS WorldShip but lacked specific manufacturing modules to support manufacturing processes within their workflow. Without manufacturing features, managing production-related tasks such as creating production orders, tracking work-in-progress, managing inventory for production, and linking these processes with sales and order fulfillment became challenging.
They often ended up in situations where they ran out of materials and needed to delay manufacturing until a new purchase order was in place and items were delivered. Having a live view of inventory levels was an absolute must for both materials and products.
The limitations of their previous shipping and order fulfillment setup, which lacked tailored manufacturing modules and essential packing lists and suffered from a suboptimal integration between their ecommerce platform and shipping software, led them to adopt Katana to streamline and automate these critical aspects of their business operations more effectively.
I configured some automation between OpenCart and UPS WorldShip to deal with the shipping, but there were no manufacturing modules or packing lists, and overall it was very clunky.
Thomas Judge, Owner at GJ Motorsports
Katana’s integration with Easy Insight allows for automated reporting and data sharing. By leveraging Katana’s real-time inventory data, they can automatically generate and send weekly reports to the supplier, keeping them informed about stock levels, projections, and inventory requirements without requiring manual updates or physical visits.
The Shop Floor App in Katana allows for streamlined shop floor operations. They can easily set and manage assignments for different production tasks. Each product’s manufacturing process, involving multiple jobs, can be tracked and managed within the app. This visibility and ease of use enhance productivity and minimize errors in manufacturing.
Katana’s real-time updates and automation features ensure that once a manufacturing order is completed, the dashboard reflects the status of orders ready for shipping. This eliminates manual checks and coordination, enabling smoother workflow transitions from production to shipping.
Keeping costs low and customers happy with automation
By successfully integrating Katana with their existing systems using API and Zapier, GJ Motorsports gained seamless data transfer capabilities. This allowed them to automate processes and synchronize information across platforms, improving workflow efficiency and reducing manual data entry.
Since implementing Katana, we’ve grown our product offering, and that wouldn’t be possible without it. It has freed up my time so I can focus on designing and creating more products. It also means that I’m not working until 11 pm every night.
Integrating Katana with ShipStation gave GJ Motorsports a powerful toolset for seamlessly managing shipping and order fulfillment — resulting in faster order processing, accurate inventory updates, and enhanced customer satisfaction. The customizable workflows in Katana allowed them to tailor their manufacturing processes and inventory management according to their unique business requirements, further improving operational efficiency and flexibility.
More case studies
Get visibility over your sales and stock
Wave goodbye to uncertainty with Katana Cloud Inventory — AI-powered for total inventory control