Case studies Customer success stories
Katana supports thousands of businesses in achieving their goals and pushing the boundaries of what’s possible.
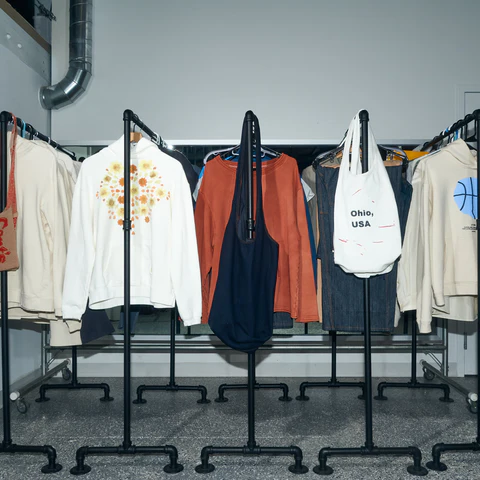
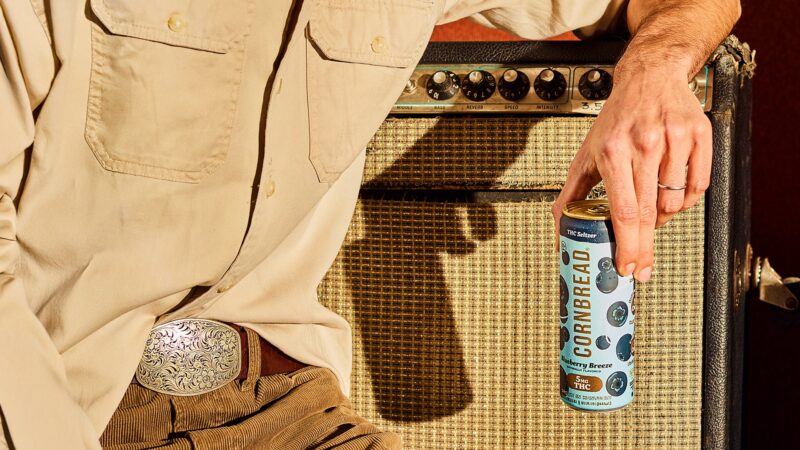
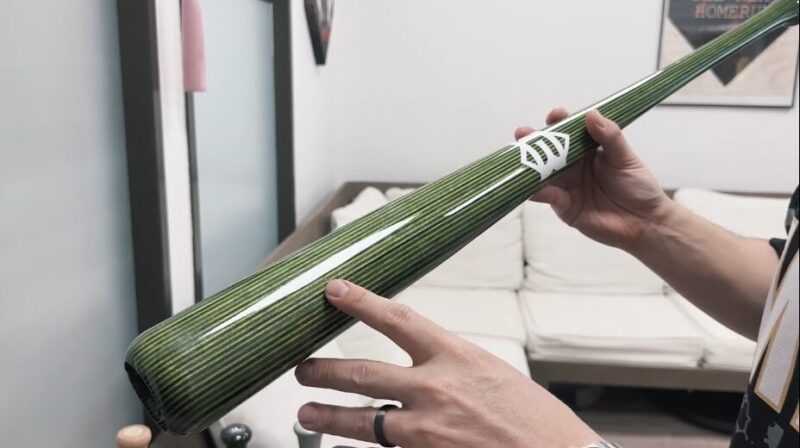
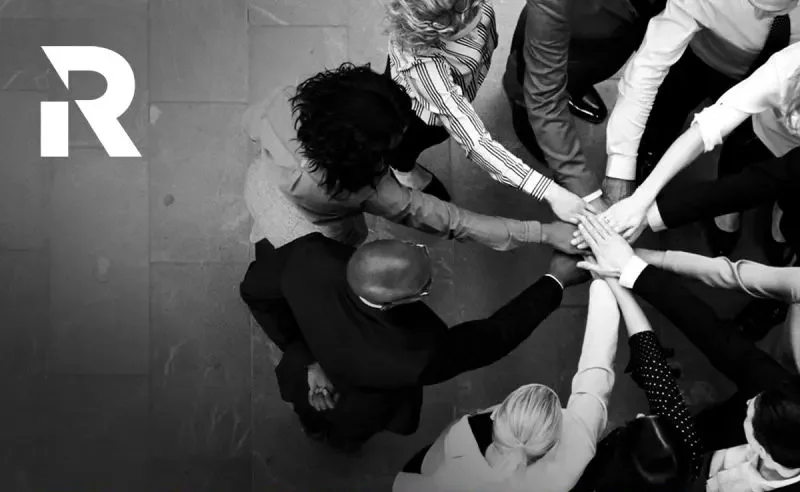
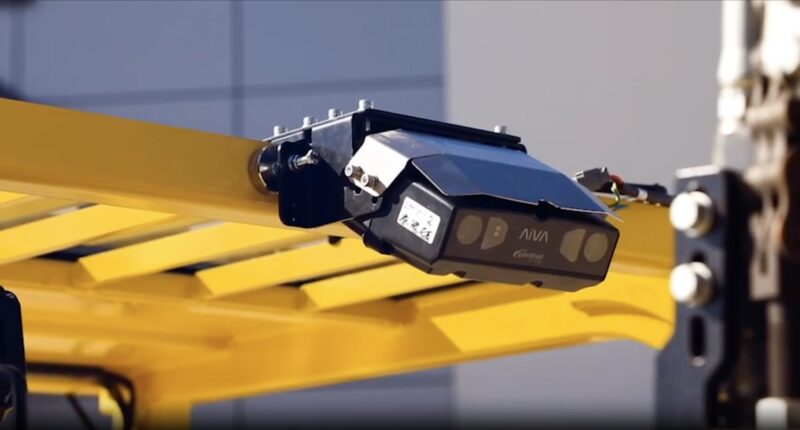
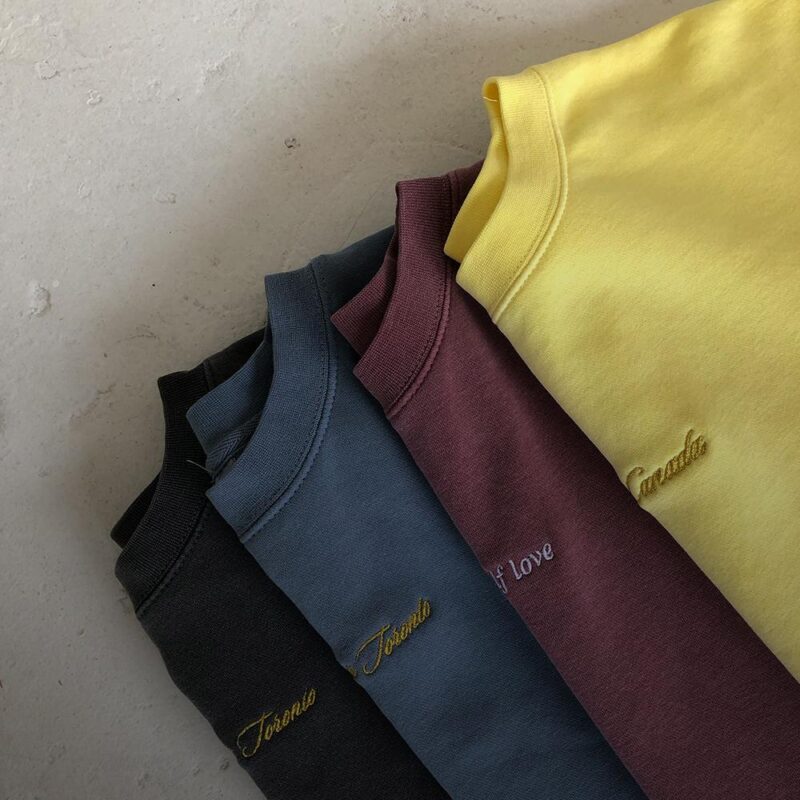
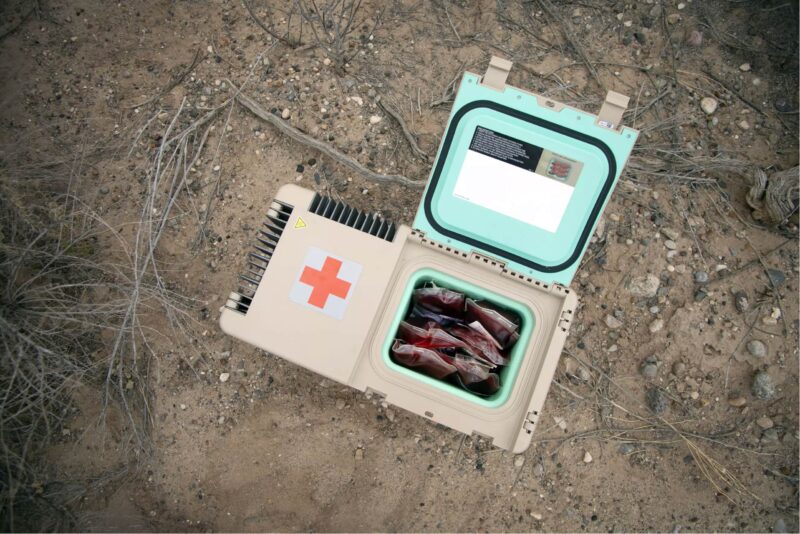
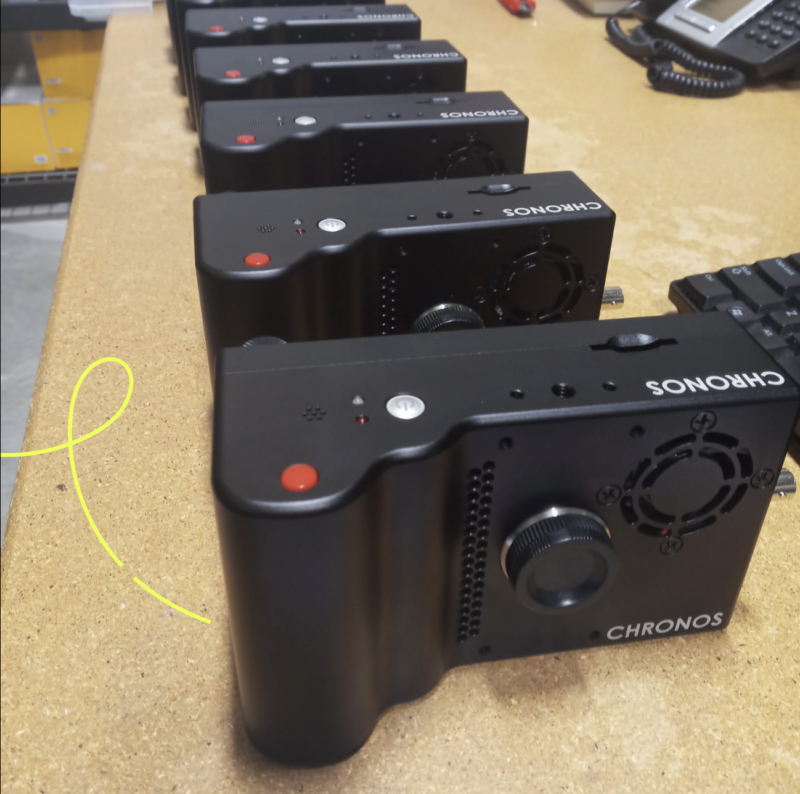
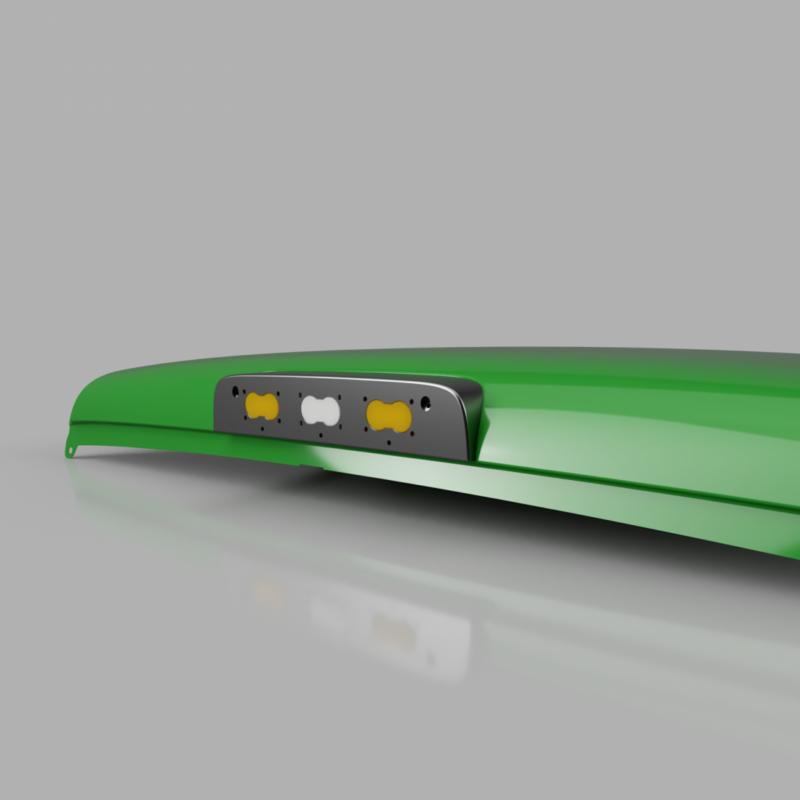
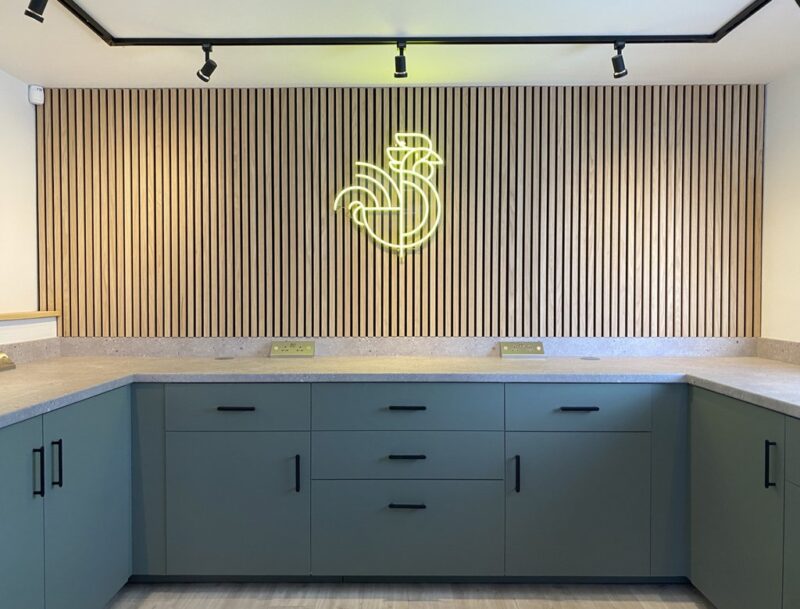
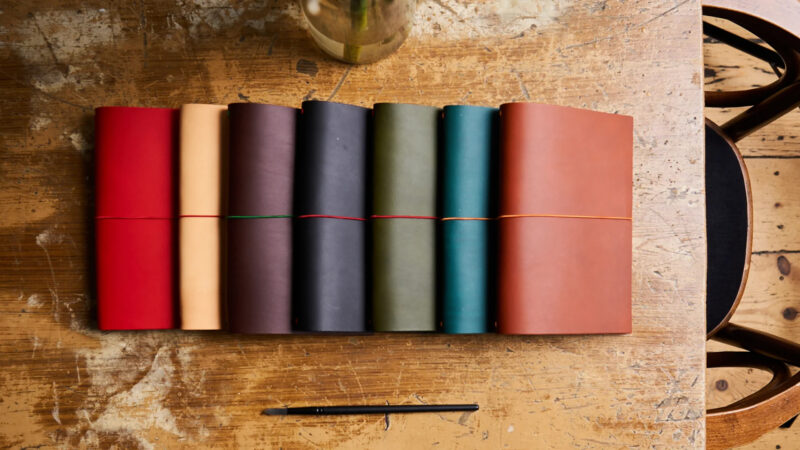
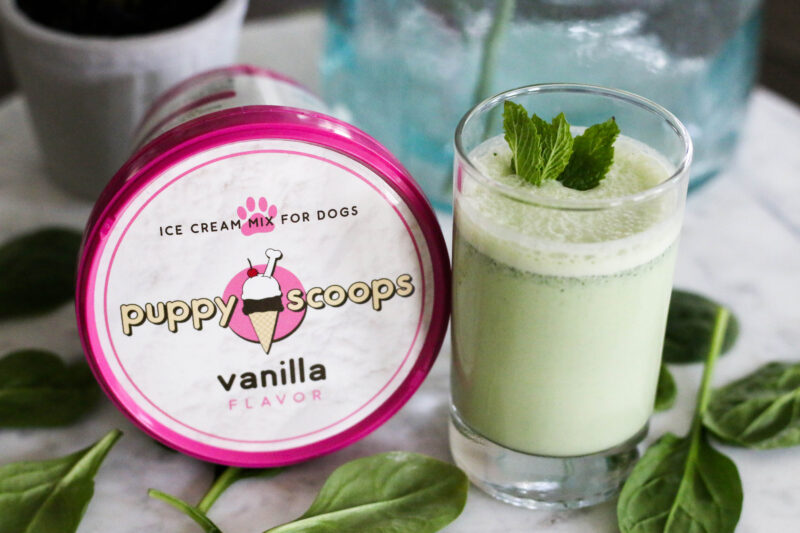
- 1
- 2
Get visibility over your sales and stock
Wave goodbye to uncertainty with Katana Cloud Inventory — AI-powered for total inventory control