Learn all about Katana and your inventory process flow
Inventory process flows in Katana
Katana Cloud Inventory is an inventory management system that helps manufacturers, wholesalers, and ecommerce merchants streamline their inventory process flow. Use the interactive map below to see exactly how Katana can help your business.
See how Katana Cloud Inventory effortlessly optimizes the different functions of inventory management.
Shop floor
Katana enhances manufacturing operations by enabling real-time tracking, scheduling, and reporting. With the Shop Floor App, businesses can create operators and assign tasks, allowing for real-time progress tracking. Get comprehensive insights into manufacturing costs, resource allocation, and material usage, facilitating more efficient and informed production management.
Warehouse
Katana helps optimize inventory process flow and sales order fulfillment by assigning tasks to operators and providing live updates. The Warehouse App allows for efficient picking and packing of sales orders, improves accuracy and speed through barcode scanning, and simplifies inventory organization by assigning default storage bins — for better inventory tracking and management.
Office
From integrating with leading software to automating your production planning, Katana gives you the toolset to centralize and manage many aspects of your business. The Planning and Forecasting add-on will help improve efficiency, compliance, and financial health. It will also assist you in enhancing cash flow management and improving your inventory process flow by preventing stockouts and overstock.
Storefront
With the rise of ecommerce and other selling strategies, you can think of your storefront as a place where customers buy your products if you’re creating your own inventory management flowchart. Using Katana, you can implement omnichannel selling strategies to manage your B2B, B2C, offline, and online sales channels all in one place. Start meeting demand with accurate inventory insights.
Shop floor
Katana enhances manufacturing operations by enabling real-time tracking, scheduling, and reporting. With the Shop Floor App, businesses can create operators and assign tasks, allowing for real-time progress tracking. Get comprehensive insights into manufacturing costs, resource allocation, and material usage, facilitating more efficient and informed production management.
Warehouse
Katana helps optimize inventory process flow and sales order fulfillment by assigning tasks to operators and providing live updates. The Warehouse App allows for efficient picking and packing of sales orders, improves accuracy and speed through barcode scanning, and simplifies inventory organization by assigning default storage bins — for better inventory tracking and management.
Office
From integrating with leading software to automating your production planning, Katana gives you the toolset to centralize and manage many aspects of your business. The Planning and Forecasting add-on will help improve efficiency, compliance, and financial health. It will also assist you in enhancing cash flow management and improving your inventory process flow by preventing stockouts and overstock.
Storefront
With the rise of ecommerce and other selling strategies, you can think of your storefront as a place where customers buy your products if you’re creating your own inventory management flowchart. Using Katana, you can implement omnichannel selling strategies to manage your B2B, B2C, offline, and online sales channels all in one place. Start meeting demand with accurate inventory insights.
Optimize your inventory process flow with Katana
Get the tools you need to streamline operations, improve efficiency, and ensure optimal stock levels
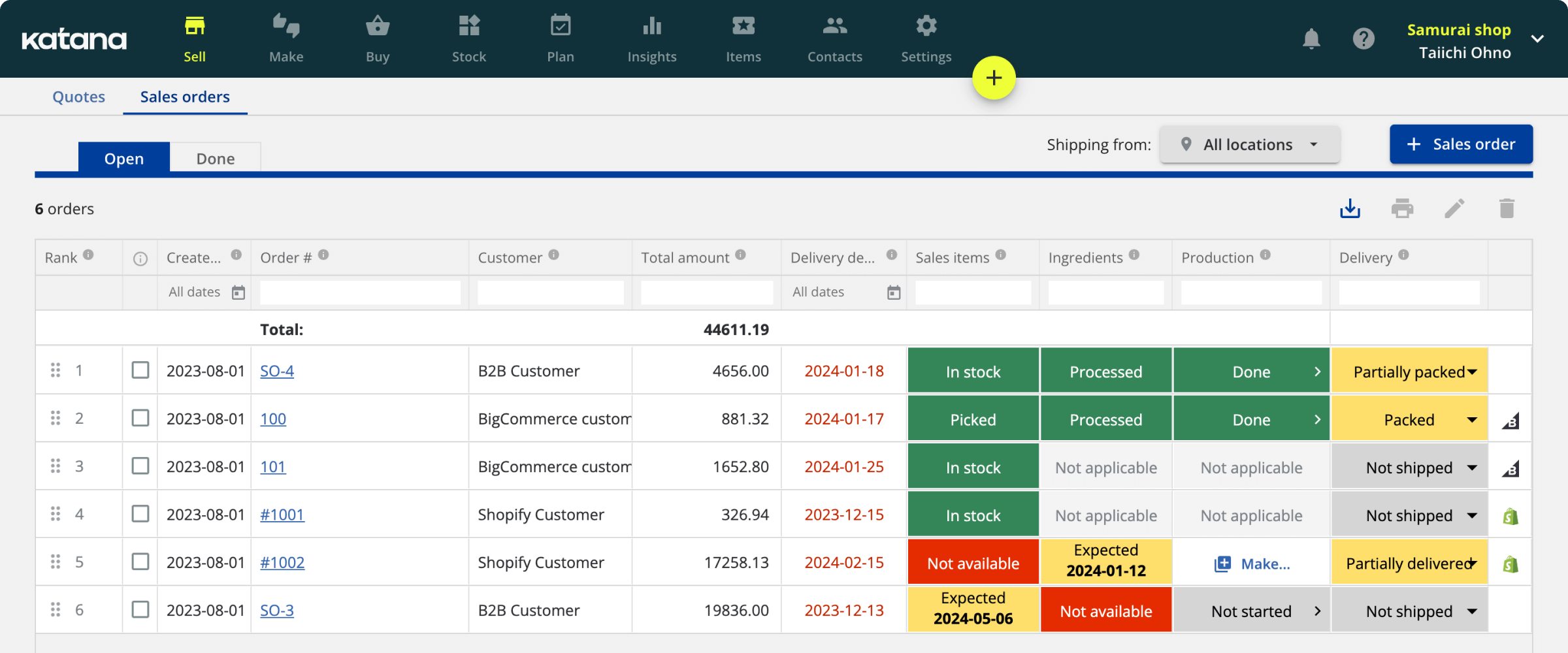